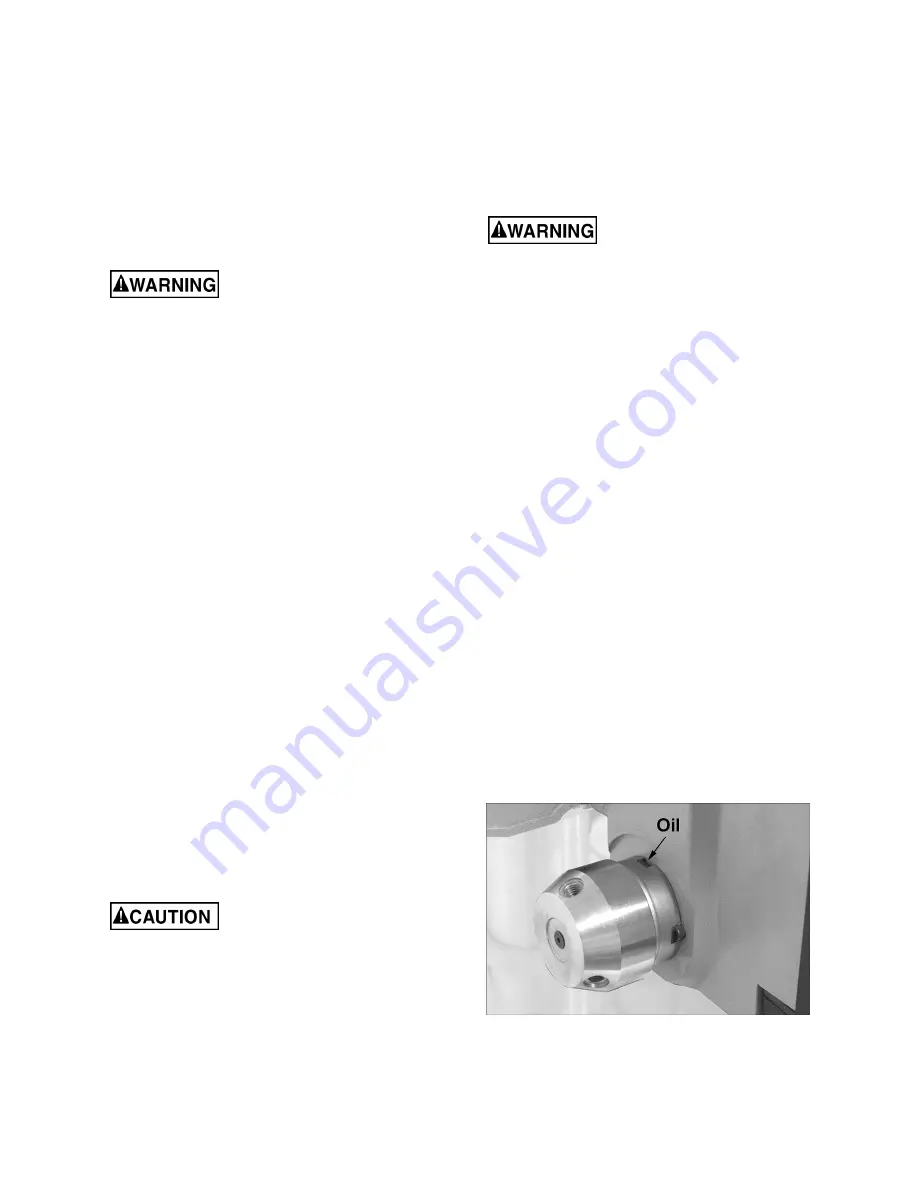
17
10.0
Operation
10.1
Installing bits
Insert bit (not provided) into chuck jaws with about
1” insertion. When using a small bit, do not insert it
so far that the jaws touch the flutes of the bit. Make
sure bit is centered in chuck before tightening chuck.
Insert chuck key into hole in side of chuck, and turn
key clockwise to tighten bit in chuck.
10.2
Positioning work piece
Whenever possible, use
clamps or work hold-downs to secure the work
piece to the table.
Always secure the work piece to prevent it being
torn from the operator’s hand. Using the column as
a work stop is not recommended; instead, use
holding devices such as clamps. When using the
table in tilted position, make sure the table is
securely tightened and the work piece is clamped
sufficiently.
For clean, splinter-free holes, place a piece of scrap
wood on the table below the work piece.
Perform operations with a minimum extension of the
quill. Adjust table position rather than using
excessive quill travel.
Feed bit into the material with only enough force to
allow the bit to work. Feeding too slowly may cause
burning of the work piece. Feeding too quickly may
cause the motor to slow and/or the bit to break.
10.3
General Inspection
Before each operation of your PM2820EVS drill
press, make a habit of checking that all locking
handles, set screws, bolts, etc., are tight on the table
and head. Confirm that drill bit is securely inserted
inside chuck jaws.
Clear all items, such as tools and rags, away from
machine.
Before attempting regular work, get the feel of the
drill press by practicing on scrap material. For best
results, always use sharp bits and proper feed rates.
10.4
Speed setting
Do not change Hi-Lo gear
setting while machine is running. Failure to
comply may result in damage to machine.
There are several factors which determine the best
speed to use in any drill press operation, such as
kind of material being worked, size of hole, type of
drill, and quality of cut desired.
A general rule of thumb is, the smaller the drill, the
greater the required RPMs. And the speed should
be faster for soft materials and slower for harder
materials.
11.0
User-maintenance
Before doing maintenance on
the machine, disconnect it from electrical
supply by pulling out the plug or switching off
the main switch. Failure to comply may cause
serious injury.
Bearings on the drill press are self-contained and
permanently lubricated; no further lubrication is
needed.
After each use:
Clean sawdust from the table with a brush (do not
use bare hands).
Periodically:
Apply a light film of oil to the quill and column. This
will reduce wear, prevent rust and assure ease of
operation.
Apply grease to the rack on the column.
Check that bolts are tight and the electrical cord is
in good condition.
Exposed metal surfaces of table and base should be
kept clean and free of rust. Protective sprays or
paste wax are available from most hardware stores.
Note: Avoid wax that contains silicone or other
synthetic ingredients; these materials can find their
way into lumber and make staining and finishing
difficult.
Annually:
The quill return spring should receive SAE 20 oil
once yearly. Apply the oil beneath the coil spring
cover (see Figure 11-1) using a squirt can.
Figure 11-1
Summary of Contents for PM2820EVS
Page 23: ...23 13 2 1 PM2820EVS Quill and Laser Assembly Exploded View ...
Page 26: ...26 13 3 1 PM2820EVS Control Panel Exploded View ...
Page 29: ...29 13 5 1 PM2820EVS Work Table Assembly Exploded View ...
Page 34: ...34 15 0 Electrical Connections for PM2820EVS Drill Press ...
Page 36: ...36 427 New Sanford Road LaVergne Tennessee 37086 Phone 800 274 6848 www powermatic com ...