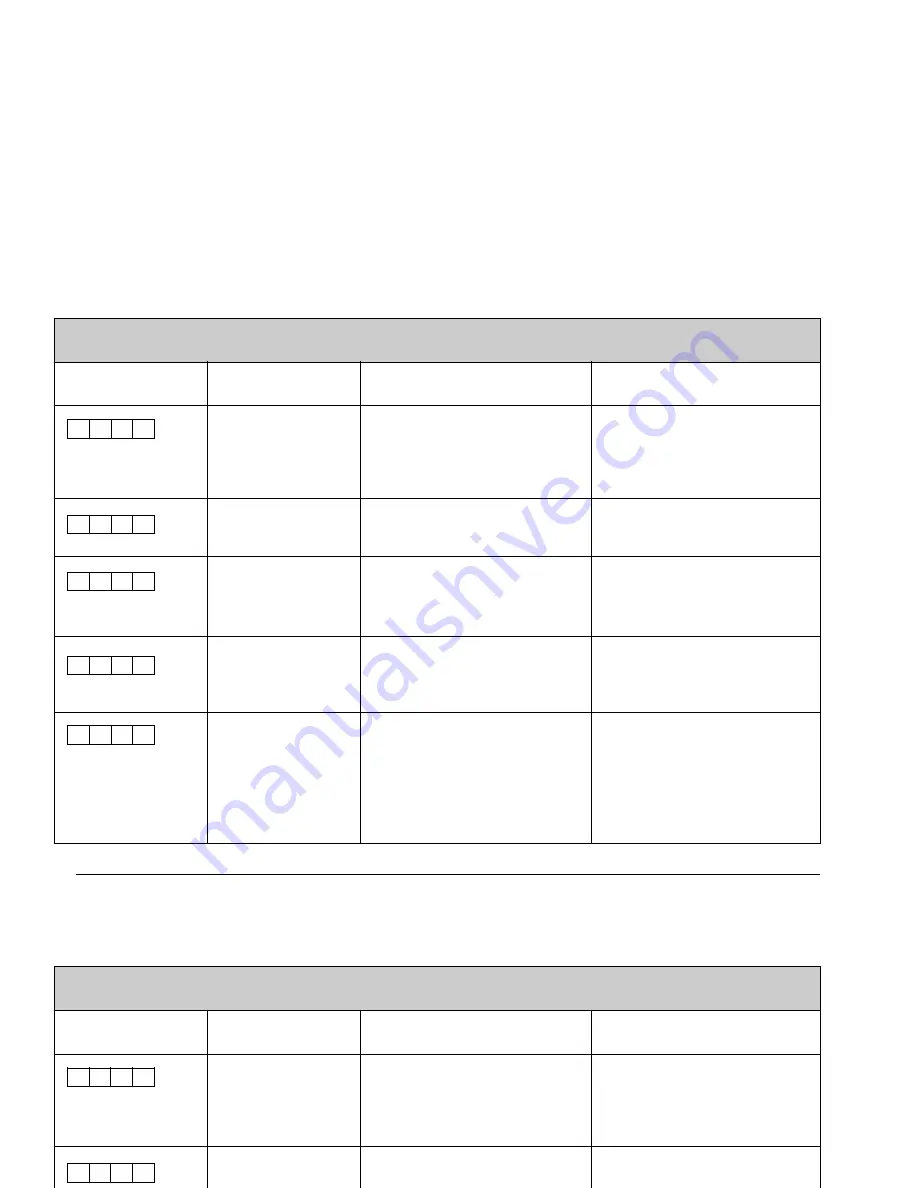
Service display
error code
in display
malfunction
possible reason
remedy
brushes stop
(thermal circuit
breaker dropped)
brushes stop (stall
protector responded)
brush lift-out and
brush motor stop
(stall protector
responded)
side brush stops
(thermal circuit
breaker dropped)
side brush stops
(stall protector
responded)
●
tape or similar foreign matter
stuck between brush and shaft
●
motor overheated
●
foreign matter, tape or similar
stuck in the brush
●
foreign matter between
brush head and machine
●
foreign matter stuck between
brush and shaft
●
motor overheated
●
foreign matter, tape etc.
block the side brush
●
check brushes for foreign
matter and remove
●
allow motor to cool down; if
problem persists, check for
reason
●
check brush head for foreign
matter and remove
●
check brush head for foreign
matter and remove
●
check side brush for foreign
matter and remove
●
allow motor to cool down
●
check side brush for foreign
matter and remove
42
1.
2.
5.
2.
1.
2.
6.
1.
1.
2.
6.
3.
1.
3.
5.
1.
1.
3.
6.
1.
Service display
error code
in display
malfunction
possible reason
remedy
brushes stop
(thermal circuit
breaker dropped)
brushes stop (stall
protector responded)
brush lift-out and
brush motor stop
(stall protector
responded)
side brush stops
(thermal circuit
breaker dropped)
side brush stops
(stall protector
responded)
●
tape or similar foreign matter
stuck between brush and shaft
●
motor overheated
●
foreign matter, tape or similar
stuck in the brush
●
foreign matter between
brush head and machine
●
foreign matter stuck between
brush and shaft
●
motor overheated
●
foreign matter, tape etc.
block the side brush
●
check brushes for foreign
matter and remove
●
allow motor to cool down; if
problem persists, check for
reason
●
check brush head for foreign
matter and remove
●
check brush head for foreign
matter and remove
●
check side brush for foreign
matter and remove
●
allow motor to cool down
●
check side brush for foreign
matter and remove
90
1.
2.
5.
2.
1.
2.
6.
1.
1.
2.
6.
3.
1.
3.
5.
1.
1.
3.
6.
1.