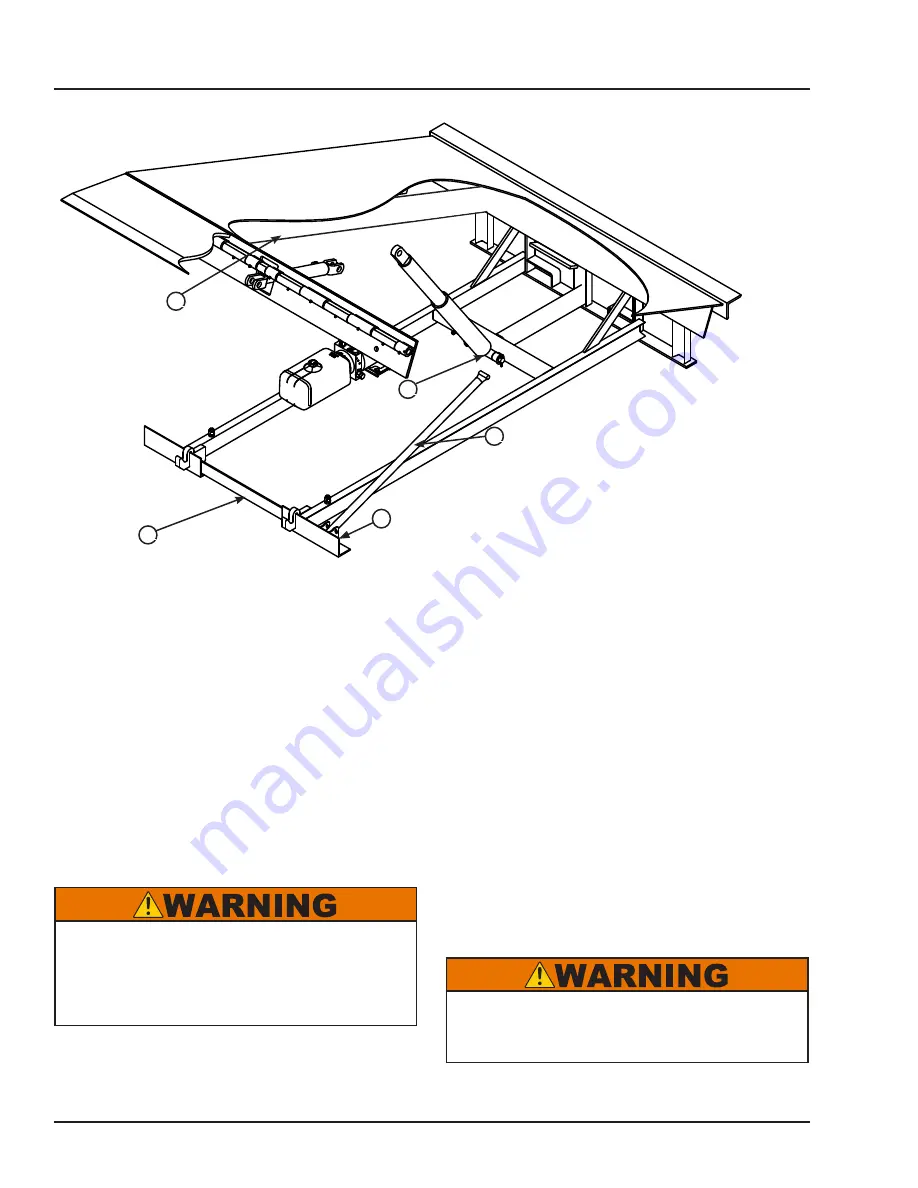
18
4111-0012 — Sept. 2018
© 2018 Systems, LLC
INSTALLATION
17. Shim and weld the maintenance prop:
a. Install shims under maintenance prop (
D
)
where prop attaches to leveler frame. Make sure
prop is solidly shimmed.
b. Raise maintenance prop (
D
) to the service
(upright) position and lock prop in this position
using an OSHA approved locking device.
18. Install shims at locations (
B and E
) using an
appropriate shimming method (see Figure 13). Both
platform cylinder trunnions must be solidly shimmed
the entire length of the trunnion. Make sure the
trunnions are level from side-to-side as well as from
front-to-back.
19. Finish weld all shims using a fillet weld.
• Weld all shims within each shim stack to each
other, then weld the shim stack to the leveler
frame.
• Weld the front leveler frame shim stacks to the
front pit curb steel.
DO NOT use the maintenance prop to support the
raised platform until the maintenance prop has
been properly shimmed and welded. The shims
must be welded to each other, and also to the
leveler frame.
Make sure the platform is properly supported in the
raised position before entering the pit to finish weld
the shims.
Figure 12
C
A
B
D
A — Platform Joists
B — Shim Location (Under Platform Cylinder Trunnions)
C — Removable “Clean Sweep” Frame Section
D — Maintenance Prop
E — Shim Location (Under Maintenance Prop)
E
Summary of Contents for LHP Series
Page 13: ...11 4111 0012 Sept 2018 2018 Systems LLC This page intentionally left blank INSTALLATION ...
Page 25: ...23 4111 0012 Sept 2018 2018 Systems LLC INSTALLATION This page intentionally left blank ...
Page 31: ...29 4111 0012 Sept 2018 2018 Systems LLC MAINTENANCE This page intentionally left blank ...
Page 42: ...40 4111 0012 Sept 2018 2018 Systems LLC PARTS B A D C Lip and Platform Parts ...
Page 47: ...45 4111 0012 Sept 2018 2018 Systems LLC PARTS This page intentionally left blank ...
Page 49: ...47 4111 0012 Sept 2018 2018 Systems LLC PARTS This page intentionally left blank ...
Page 50: ...48 4111 0012 Sept 2018 2018 Systems LLC This page intentionally left blank MISCELLANEOUS ...