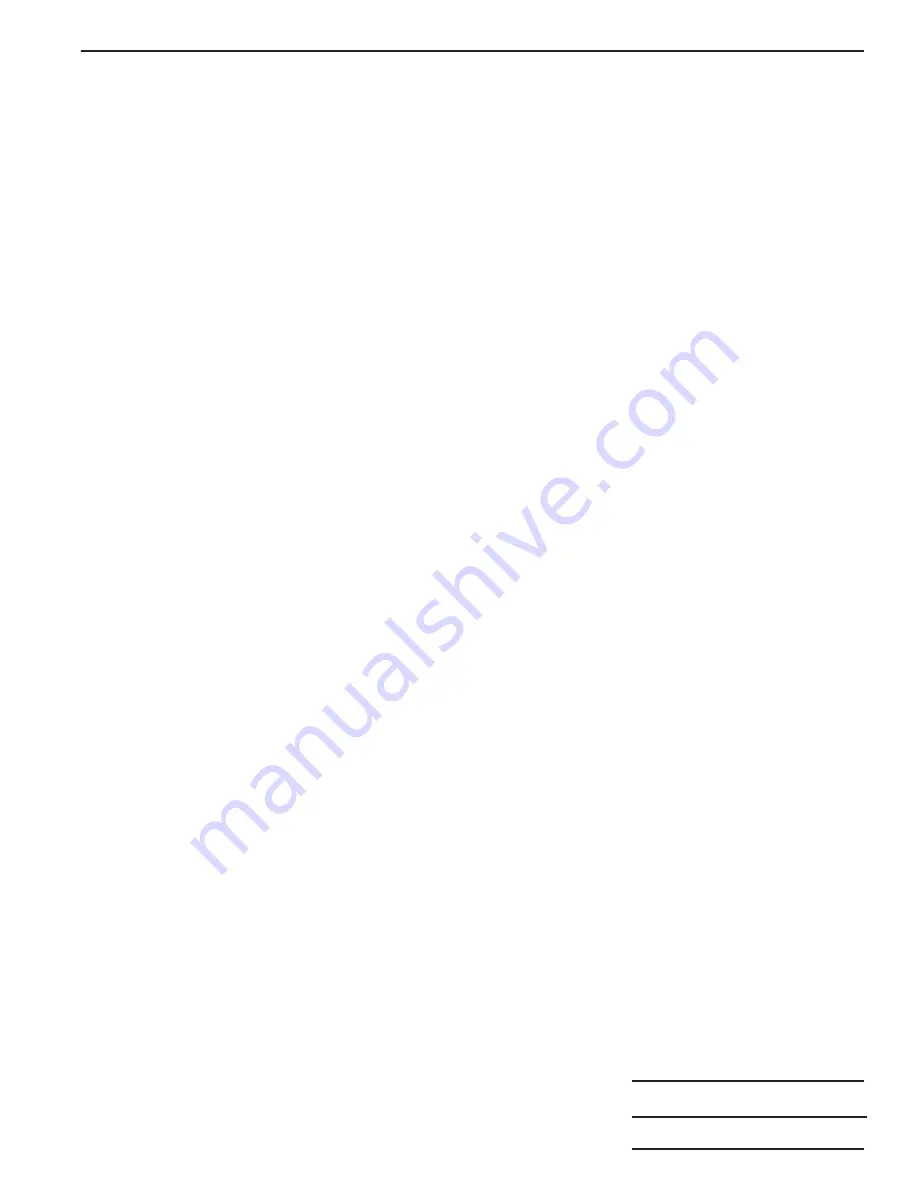
Operating Instructions
Form No. 102838
PREVENTIVE MAINTENANCE
NOTE: Any repairs of servicing that requires dismantling the pump must be performed in a dirt-free
environment by a qualified technician.
Bleeding Air from the System
Upon initial startup or after prolonged use, a significant amount of air may accumulate within the hydraulic system.
This entrapped air can cause the cylinder to respond slowly or behave in an unstable manner. To remove the air, run
the system through several cycles (extending and retracting cylinders) free of any load.
NOTE: The cylinder must
be at a lower level than the pump to allow air to be released through the pump reservoir.
Inspecting the Hydraulic Fluid Level
Check the oil level in the reservoir periodically. With all cylinder(s) retracted, the oil level should be 1" from the filler
cap. Drain, clean and replenish the reservoir with Power Team hydraulic fluid yearly or more often if necessary. The
frequency of oil change will depend upon the general working conditions, severity of use and overall cleanliness and
care given the pump.
Maintenance Cleaning
1. Keep the outer surface of the pump as free from dirt as possible.
2. Protect all unused couplers.
3. Keep all hose connections free of dirt and grime.
4. Keep the filler cap clean and unobstructed at all times.
5. Equipment connected to the pump must be kept clean.
6. Use only Power Team hydraulic fluids in this pump. Change as recommended.
Draining and Cleaning the Reservoir
IMPORTANT: Clean the pump exterior before the pump interior is removed from the reservoir.
1. Remove the screws that fasten the pump assembly to the reservoir. Remove the pump assembly from the
reservoir. Do not damage the gasket, filter or relief valve.
2. Drain the reservoir of all fluid. Refill half full with clean Power Team hydraulic fluid.
3. Place the pump assembly back onto the reservoir and secure with two machine screws assembled on opposite
corners of the housing.
4. Run the pump for several minutes. Remove the two cover screws and lift off the pump assembly again. Drain and
wipe out the reservoir with a clean, lint-free cloth.
5. Fill the reservoir with Power Team hydraulic fluid to 1" from the filler cap. Place the pump assembly (with gasket)
on the reservoir and install the screws. Tighten securely and evenly.
Adding Oil to the Reservoir
1. Cylinder(s) must be fully retracted and the motor off when adding oil to the reservoir.
2. Clean the entire area around the filler cap before removing the filler cap.
3. Use a clean funnel with filter when adding oil.
4. Use only Power Team hydraulic fluids.
5. Fill to 1" from the filler cap.
Sheet No.
2 of 3
Rev. 7
Date: 25 May 2012