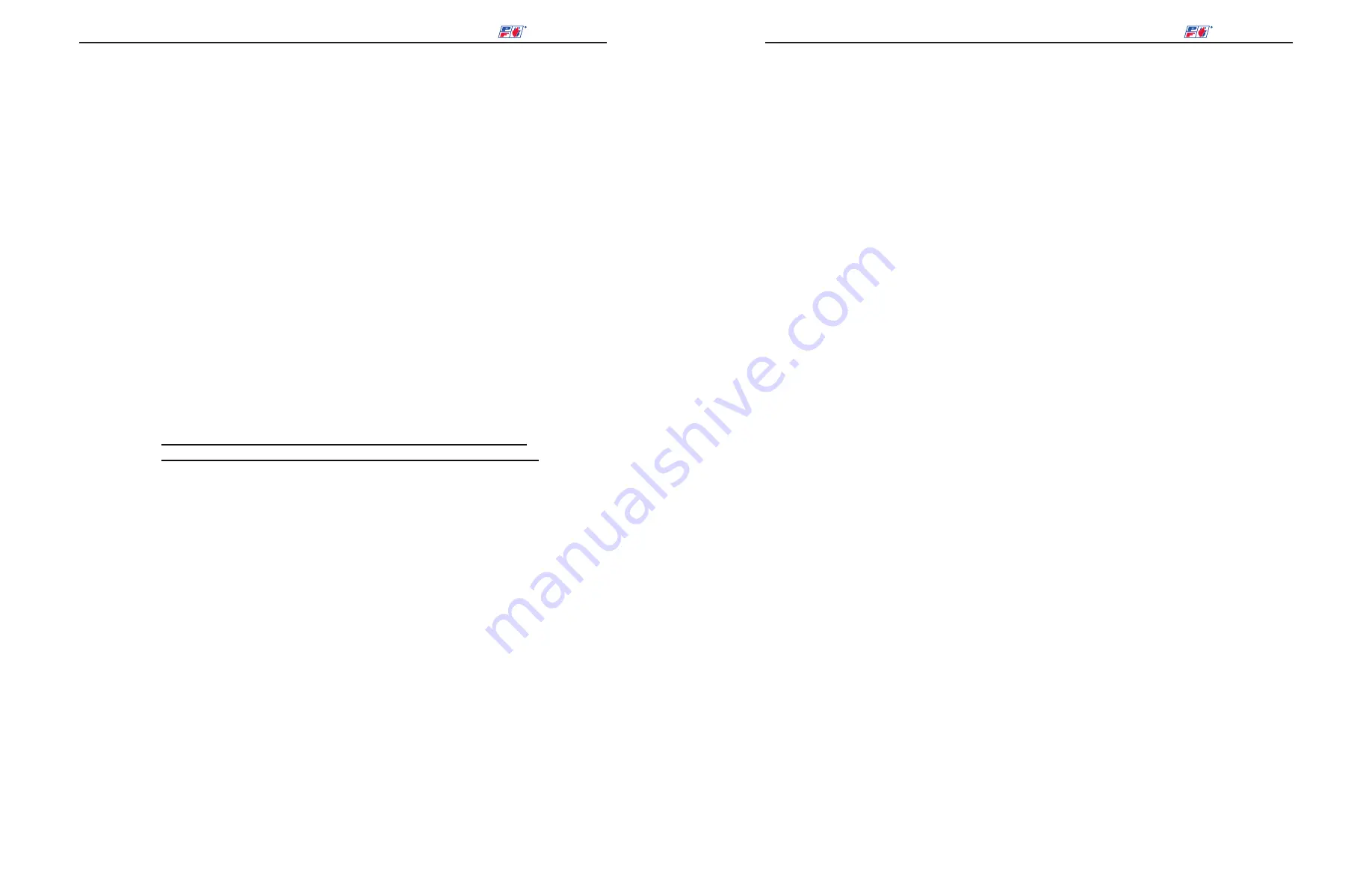
15
NOVA PLUS Installation & Operation Manual -
POWER FLAME INCORPORATED
ENTER
ESC
®
29.
If the burner operation is abnormal, refer to Trouble Shooting Suggestions, as well as
trouble shooting information included in the flame safeguard manufacturer’s bulletin
shipped with the burner. It is also strongly suggested that all test procedures outlined in
the flame safeguard control manufacturer’s bulletin be conducted.
30.
Complete the Burner Start Up Information and Test Data sheets on
page 22.
14.
GAS PILOT IGNITION ADJUSTMENT
Excessive gas pressure and insufficient air are the most common causes of pilot ignition failure.
Gas pressure should be read at the test tee on the pilot gas supply pipe with a manometer or 0
– 10” W.C. gauge. Look for stability of gas pressures at all times. Some job conditions or heat
exchangers may require larger air damper openings or different gas pressures than
recommended. For dependable pilot ignition, always use air damper setting to provide the
MOST air and LOWEST pilot gas pressure settings allowable for good pilot signal at all times.
1.
Remove pilot assembly and check for proper orifice size and spark gap. The spark gap
between the electrode and inside radius of the gas pilot assembly should be 1/8” – 3/32”.
See Figure 11.
FIGURE 7
Typical Pilot
D)
Element Temperature Safety limit
Each burner is equipped with an RKC Instrument model SA100L
temperature controller mounted within the burner control panel. The
controller is attached to a thermocouple mounted on the inside of the
fiber matrix element. Some models have a second temperature
controller which attaches to an infrared thermocouple. This infrared
thermocouple senses the temperature inside the fiber matrix element.
The controller is a safety device designed to shut down the burner if
the internal temperature exceeds 350 degrees F.
The controller has two digital readouts. The upper number represents
the current temperature at the thermocouple. The lower number
represents the setpoint. The start-up technician must ensure the
factory setpoint of 350 degrees F is correctly set. If not, the setting can
be adjusted by pressing the Set button. At this time the first digit of the
setpoint field will flash. The setpoint can be adjusted by pressing the
up or down buttons as needed to select 350 degrees. Press Set three
times to return the display to the main screen which shows the current
temperature over the setpoint. Press the Reset button. The setpoint is
now reset to the new value.
This device is an integral safety limit of the burner do not
disconnect or change the setting above the factory setting.
2)
Disconnect both wires at the air flow switch and temporarily clip them
together. Make sure that they cannot ground against anything, since they
will be powered with 110 volts during the test.
3)
Put a continuity meter across the common and normally open terminals
on the air switch.
4)
Close the gas train checking cock.
5)
Start the blower motor. The meter should read electrical continuity as
soon as the blower starts.
6)
Disconnect the wire which energizes coil of blower motor relay (starter),
or open the main power disconnect switch to the burner. Within 3 to 4
seconds after the blower motor is de-energized, the meter should indicate
an open air flow switch circuit (no continuity).
7)
If the switch does not open in 3 to 4 seconds, re-adjust accordingly. Turn
the air flow switch adjustment screw clockwise to shorten cut-off response
time and counter-clock-wise to lengthen cut-off response time.
8)
Turn the burner power off. Remove the shorting clip from the two
disconnected wires, cover them with electrical tape and let them hang loose
(they will be powered with 110 volts, so don’t let them ground out).
9)
Open the gas train checking cock. Turn the burner on. With the wires
disconnected, the burner should go into a purge cycle, although neither
the ignition nor the main fuel valve circuits will be energized. If they do
energize, there is a wiring problem. Correct as required.
10)
Turn power off. Reconnect the air flow switch wires to the air flow switch
terminals. Place burner back into normal operation.
28.
The Owner’s Operating Instructions,
page 26
of this manual, should be posted in a
clearly visible location close to the burner.
12
NOVA PLUS Installation & Operation Manual -
POWER FLAME INCORPORATED
DC4 DRAFT CONTROL
ENTER
ESC
®
10. Re-start the burner. With the pilot gas cock closed, the burner will go through a blower
pre-purge period, after which the gas pilot ignition transformer will be energized, although
no pilot will be established. (At no time should there be any flame signal reading, nor
should the main gas valve attempt to open.) At the end of the pilot trial for ignition and
blower purge period, the flame safeguard control should shut the system down in a safety
lockout mode, requiring manual reset of the flame safeguard control to restart the burner.
11. Wait three minutes, reset the flame safeguard control safety switch (restarting the burner)
and open the pilot gas cock. When the blower pre-purge period ends and the burner is
energized – if the flame safeguard control has a test/run switch – flip the switch to the test
position while the pilot is on and make adjustments as required.
See pages 15 & 16
for pilot
ignition adjustments. Recycle the burner several times to make certain pilot operation is
reliable.
12. With pilot adjustments completed, reset the switch to the Run position, which will allow the
sequence to proceed to the automatic gas valve energizing position.
13. When the main automatic gas valve begins to open, slowly open the checking gas cock to
light off the main flame. The main flame should light immediately. If not, it may be
necessary to eliminate air from the main gas line and/or adjust main gas pressure
regulator flow rates.
14. Adjust the burner as necessary to provide smooth ignition of the main flame. If the flame
signal drops significantly when the main automatic gas valve opens, slightly increase the
pilot gas pressure to attain a stable flame signal value.
15.
Refer to item 27, page 13,
carefully for recommended limit control and other control devices
operational checkout.
16. Initial adjustments should be made at the low fire position. All Power Flame burners are
factory tested and adjusted. However, to determine that the metering butterfly valve is, in
fact, in the low fire position, observe the end of the metering valve shaft. The slot in the
end of the shaft indicates the position of the valve. When the slot is in the horizontal
position (parallel with the gas flow direction), the valve is fully open. On servo operated
systems, verify the valve position by viewing through the end of the pipe.
17. Tighten (finger tight) the hex bolt to the linkage rod at the swivel on the modulating motor
driver arms and run the motor through its full travel to ensure that the linkage is free and
that limits on the metering device and air dampers are not exceeded.
18. Turn the burner on and let it advance to the main flame light off position. Take action as
necessary to hold the linkage at the low fire position by using a manual potentiometer or
electrically disconnecting the modulating motor. Power Flame burners are tested at the
factory and linkage adjustments for modulation are made at that time.
19. With the burner in the factory set low fire position, (verify by checking mixing spool air
pressure of typically 0.2” to 0.5”) adjust air and fuel linkage to good fuel/air ratio low fire
settings (6 – 9% O
2
little or no CO). Mark the linkage at the new settings.
20. Increase the firing rate to the midway point. Set the fuel/air ratios to achieve good
combustion values (6 - 9% O
2
little or no CO). Mark the linkage as a reference point for
this new mid fire position.