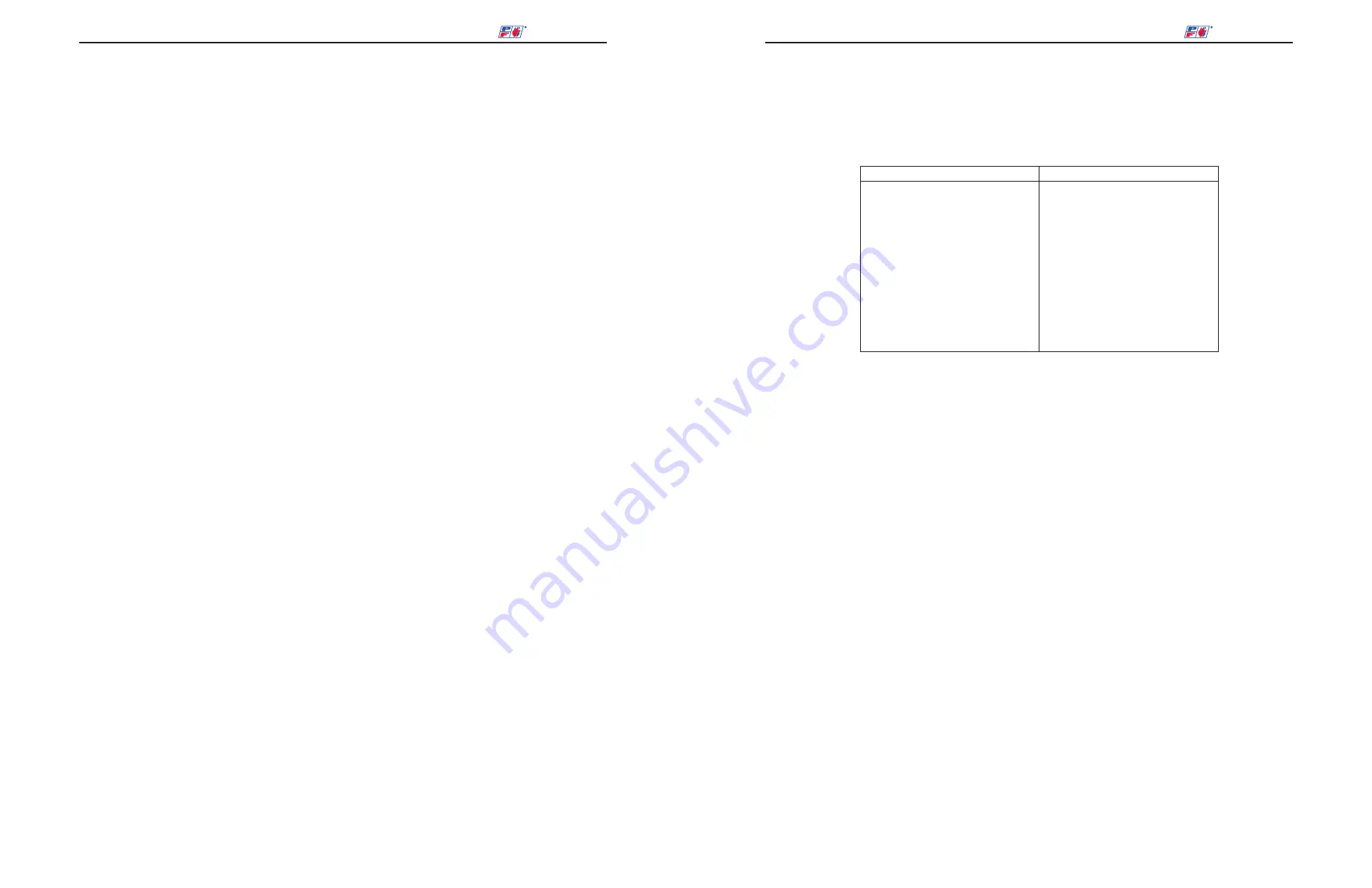
17
NOVA PLUS Installation & Operation Manual -
POWER FLAME INCORPORATED
DC4 DRAFT CONTROL
ENTER
ESC
®
E.
Occasional low voltage supply. Have local utility correct. Make certain that the
burner control circuit transformer (if supplied) is correct for the voltage being
supplied.
F.
Occasional low gas supply pressure. Have utility correct.
G.
Element air pressure switch opens during purge. Reset switch to remain closed
just under maximum purge pressure.
3.
Burner Motor Runs, but Pilot Does Not Light
A.
Gas supply to burner shut off – make sure all manual gas supply valves are
open. Automatic high pressure valve at meter such as Sentry type tripped shut
due to high gas pressure – reset valve and correct cause for trip out.
B.
Pilot solenoid valve not opening – listen and feel for valve actuation. Solenoid
valve not being powered – check electrical circuitry. Replace coil or entire valve
if coil is burned out.
C.
Defective gas pilot regulator – replace.
D.
Gas pressure too high or too low at pilot orifice. Check orifice size in gas pilot
assembly. Replace if incorrect. Refer to gas pilot adjustments for correct
settings. Readjust as required.
E.
Defective ignition transformer – replace. Incorrect ignition electrode settings –
refer to gas pilot adjustments for correct settings.
F.
Defective flame safeguard control or plug in purge timing card. Replace as
required.
G.
Air flow switch not making circuit – check out electrically and correct pressure
adjustment on switch, if required. Defective air flow switch – replace. Air switch
negative pressure sensing tube out of position – reposition as necessary.
4.
Burner Motor Runs and Pilot Lights, but Main Gas Flame Is Not Established
A.
Main shutoff or test cock closed. Check to make certain fully open.
B.
Pilot flame signal reading too low to pull in flame safeguard relay. Refer to gas
pilot settings section and readjust as required.
C.
Defective automatic main or auxiliary gas shut off valves. Check electrical
circuitry to valves. Replace valves or correct circuitry as required.
D.
Defective flame safeguard control or plug in amplifier. Check and replace as
required.
E.
Butterfly valve set incorrectly on modulating burner. Readjust as required.
Table 3
Acceptable Stable Pilot and/or Main Flame Current Readings
Control
U.V.
Infrared
R7800
1.25-5.0 DC Volts
1.25-5.0 DC Volts
E
MK7
5 min., 10 or greater normal
5 min., 10 or greater normal
110
10 min., 20 or greater normal
10 min., 20 or greater normal
15.
TROUBLE SHOOTING SUGGESTIONS
1.
Burner Fails to Start
A.
Defective On/Off or fuel transfer switch. Replace
B.
Control circuit has an open control contact. Check limits, low water cutoff, proof
of closure switch and others as applicable.
C.
Bad fuse or switch open on in-coming power source. Correct as required.
D.
Motor overloads tripped. Reset and correct cause for trip out.
E.
Flame safeguard control safety switch tripped out. Reset and determine cause
for apparent flame failure.
F.
Loose connections or faulty wiring. Tighten all terminal screws and consult
wiring diagram furnished with the burner.
G.
Flame safeguard control starting circuit blocked due to flame relay being
energized. Possible defective scanner – replace. Possible defective amplifier –
replace. Scanner actually sighting flame due to leaking fuel valve – correct
unwanted flame cause. Defective flame safeguard control – replace.
H.
Defective blower motor. Repair or replace.
I.
LFI air switch open. Verify damper is in the low fire position or reset switch.
2.
Occasional Lockouts For No Apparent Reason
A.
Gas pilot ignition failure. Refer to pilot adjustment section and readjust to make
certain that the ignition is instant and that flame signal readings are stable and
above minimum values. Use a manometer or 0 to 10” W.C. gas pressure gauge
on pilot test tee to make certain that pressure is as recommended.
B.
Gas pilot ignition. Verify that there are no cracks in the porcelain and that
transformer end and electrode end plug in connections are tight.
C.
Loose or broken wires. Check all wire nut connections and tighten all terminal
screw connections in panel and elsewhere as appropriate.
D.
Ensure that when main flame lights, the air flow switch is not so critically set as to
allow occasional momentary opening of the air switch contacts.
10
NOVA PLUS Installation & Operation Manual -
POWER FLAME INCORPORATED
DC4 DRAFT CONTROL
ENTER
ESC
®
12. BURNER START UP AND SERVICE TEST EQUIPMENT REQUIRED
The following test equipment is required to ensure proper start up and adjustment of burner
equipment to obtain maximum efficiency and reliability of operation.
For any Gas
Flue Gas Analyzer with O
2
,
NOx, CO capability (Required)
Stack thermometer
Draft gauge or inclined
Manometer
Combination volt/ammeter
D.C. microammeter or D.C.
U-Tube manometer 0-16”
W.C. or calibrated 0-10” and
0-35” W.C. pressure gauges.
PSIG 0-5#
(Higher pressure ranges may
be necessary depending upon
gas inlet supply pressure)
Voltmeter, as required by
Flame safeguard
Measure the excess O
2
and test for CO to make certain that the burner is adjusted so that it has an
excess 0
2
of typically 6% to 9% when firing without FGR (flue gas recirculation). The excess 0
2
level
when using FGR will typically be 5% to 7%. This is the typical excess O
2
range required for the premix
burner to obtain reduced NOx emissions. If higher excess O
2
is required to obtain a particular emission
level the CO level must be checked thoroughly. CO is a dangerous product of incomplete combustion
and is associated with combustion inefficiency and increased fuel cost. Any CO readings on any fuel
should be near 0% or less than 50 ppm.
13.
BURNER START UP SEQUENCE INSTRUCTIONS
1.
Prior to burner start up – contact the local gas company to determine if any correction
factors have to be applied to their indicated meter flow rates. This information is important
as relates to achieving specific heat exchanger BTU/HR inputs.
Refer to Figure 2, page 4
and the burner rating plate for additional firing rate information.
2.
Refer to
Figure 6, page 11
for air switch locations and pressure settings.
3.
Refer to the gas piping diagram furnished with the burner. Check gas piping, controls and
valves for leaks and compliance with codes.
4.
Check all linkages and servo couplings for proper position and tightness
5.
Close main checking and pilot gas cocks. Install one gas pressure gauge on the manifold
(orifice tee) to read burner firing head pressure (use 0-32” W.C. gauge or a manometer).
Install a second gas pressure gauge to read gas supply pressure between the main gas
cock and the inlet to the main gas pressure regulator (use a 0-5 psi gauge or as
appropriate). If there is no tapping in this location, install a tee at the point where the pilot
gas supply is connected to the main gas line. Slowly open the main gas cock in order to
determine that the incoming gas pressure is within the specified limits of the main and pilot
gas pressure regulators, automatic fuel valves and gas pressure switches.