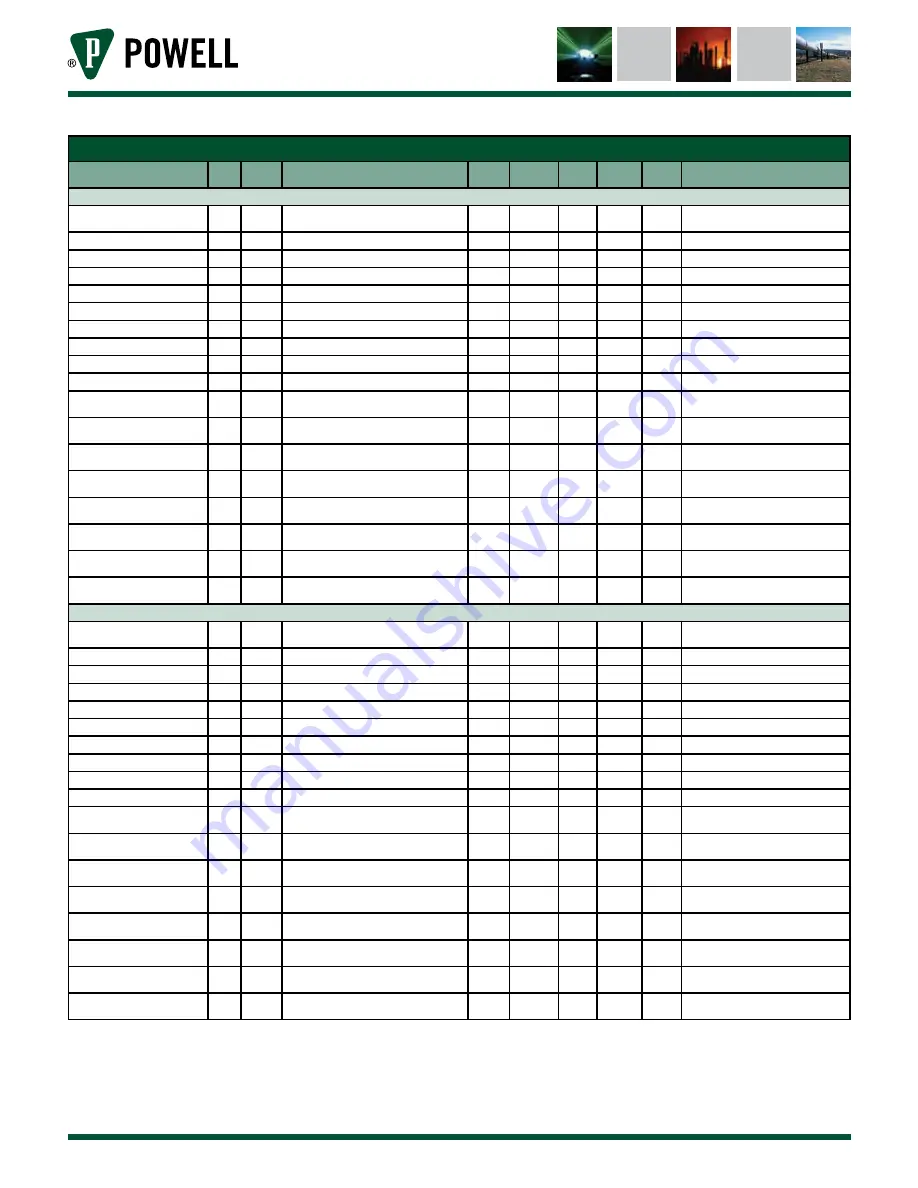
Powered by Safety
®
55
Appendix D
01.4IB.48041
Table AB MODBUS Memory Map (cont.)
Register Name
Read /
Write
Register
Type
Description
Default
Range,
format:
UOM
Register #
Modbus
Offset #
Interpretation
Alarm Slot 3 - 30140 to 30157
Alarm Type
R
Input
Alarm Type
0
0, 1, 2
N/A
30140
141
0 = Disabled, 1 = Absolute Temperature
2 = Absolute Current
Latching
R
Input
Latching Alarm
0
0, 1
N/A
30141
142
0 = Non-Latching, 1 = Latching
Warning Threshold On
R
Input
Threshold to enter warning condition
N/A
0 - 65535
N/A
30142
143
Depends on alarm type
Warning Threshold Off
R
Input
Threshold to leave warning condition
N/A
0 - 65535
N/A
30143
144
Depends on alarm type
Alarm Threshold On
R
Input
Threshold to enter alarm condition
N/A
0 - 65535
N/A
30144
145
Depends on alarm type
Alarm Threshold Off
R
Input
Threshold to leave alarm condition
N/A
0 - 65535
N/A
30145
146
Depends on alarm type
Source Channel Low
R
Input
Low word of source channels bit-mask, bits 0 - 15
N/A
0 - 65535
N/A
30146
147
Source Channel Mid 1
R
Input
Source channels bit-mask, bits 16 - 31
N/A
0 - 65535
N/A
30147
148
Source Channel Mid 2
R
Input
Source channels bit-mask, bits 32 - 47
N/A
0 - 65535
N/A
30148
149
Source Channel High
R
Input
High word of source channels bit-mask, bits 48 - 63
N/A
0 - 65535
N/A
30149
150
Warning Channel Low
R
Input
Bit-mask of source channels in warning condition
Bits 0 - 15
N/A
0 - 65535
N/A
30150
151
Warning Channel Mid 1
R
Input
Bit-mask of source channels in warning condition
Bits 16 - 31
N/A
0 - 65535
N/A
30151
152
Warning Channel Mid 2
R
Input
Bit-mask of source channels in warning condition
Bits 32 - 47
N/A
0 - 65535
N/A
30152
153
Warning Channel High
R
Input
Bit-mask of source channels in warning condition
Bits 48 - 63
N/A
0 - 65535
N/A
30153
154
Alarm Channel Low
R
Input
Bit-mask of source channels in alarm condition
Bits 0 - 15
N/A
0 - 65535
N/A
30154
155
Alarm Channel Mid 1
R
Input
Bit-mask of source channels in alarm condition
Bits 16 - 31
N/A
0 - 65535
N/A
30155
156
Alarm Channel Mid 2
R
Input
Bit-mask of source channels in alarm condition
Bits 32 - 47
N/A
0 - 65535
N/A
30156
157
Alarm Channel High
R
Input
Bit-mask of source channel in alarm condition
Bits 48 - 63
N/A
0 - 65535
N/A
30157
158
Alarm Slot 4 - 30160 to 30177
Alarm Type
R
Input
Alarm Type
0
0, 1, 2
N/A
30160
161
0 = Disabled, 1 = Absolute Temperature,
2 = Absolute Current
Latching
R
Input
Latching Alarm
0
0, 1
N/A
30161
162
0 = Non-Latching, 1 = Latching
Warning Threshold On
R
Input
Threshold to enter warning condition
N/A
0 - 65535
N/A
30162
163
Depends on alarm type
Warning Threshold Off
R
Input
Threshold to leave warning condition
N/A
0 - 65535
N/A
30163
164
Depends on alarm type
Alarm Threshold On
R
Input
Threshold to enter alarm condition
N/A
0 - 65535
N/A
30164
165
Depends on alarm type
Alarm Threshold Off
R
Input
Threshold to leave alarm condition
N/A
0 - 65535
N/A
30165
166
Depends on alarm type
Source Channel Low
R
Input
Low word of source channels bit-mask, bits 0 - 15
N/A
0 - 65535
N/A
30166
167
Source Channel Mid 1
R
Input
Source channels bit-mask, bits 16 - 31
N/A
0 - 65535
N/A
30167
168
Source Channel Mid 2
R
Input
Source channels bit-mask, bits 32 - 47
N/A
0 - 65535
N/A
30168
169
Source Channel High
R
Input
High word of source channels bit-mask, bits 48 - 63
N/A
0 - 65535
N/A
30169
170
Warning Channel Low
R
Input
Bit-mask of source channels in warning condition
Bits 0 - 15
N/A
0 - 65535
N/A
30170
171
Warning Channel Mid 1
R
Input
Bit-mask of source channels in warning condition
Bits 16 - 31
N/A
0 - 65535
N/A
30171
172
Warning Channel Mid 2
R
Input
Bit-mask of source channels in warning condition
Bits 32 - 47
N/A
0 - 65535
N/A
30172
173
Warning Channel High
R
Input
Bit-mask of source channels in warning condition
Bits 48 - 63
N/A
0 - 65535
N/A
30173
174
Alarm Channel Low
R
Input
Bit-mask of source channels in alarm condition
Bits 0 - 15
N/A
0 - 65535
N/A
30174
175
Alarm Channel Mid 1
R
Input
Bit-mask of source channels in alarm condition
Bits 16 - 31
N/A
0 - 65535
N/A
30175
176
Alarm Channel Mid 2
R
Input
Bit-mask of source channels in alarm condition
Bits 32 - 47
N/A
0 - 65535
N/A
30176
177
Alarm Channel High
R
Input
Bit-mask of source channel in alarm condition
Bits 48 - 63
N/A
0 - 65535
N/A
30177
178
Summary of Contents for BriteSpot Plus
Page 4: ...Powered by Safety 01 4IB 48041 BriteSpot Plus This page is left blank intentionally ...
Page 29: ...Powered by Safety 19 Installation 01 4IB 48041 Figure 20 Panel Mount Clip Installation X X ...
Page 57: ...Powered by Safety 47 Appendix A 01 4IB 48041 Figure 64 10250 BSPL 18C1P1E0X0 Dimensions ...