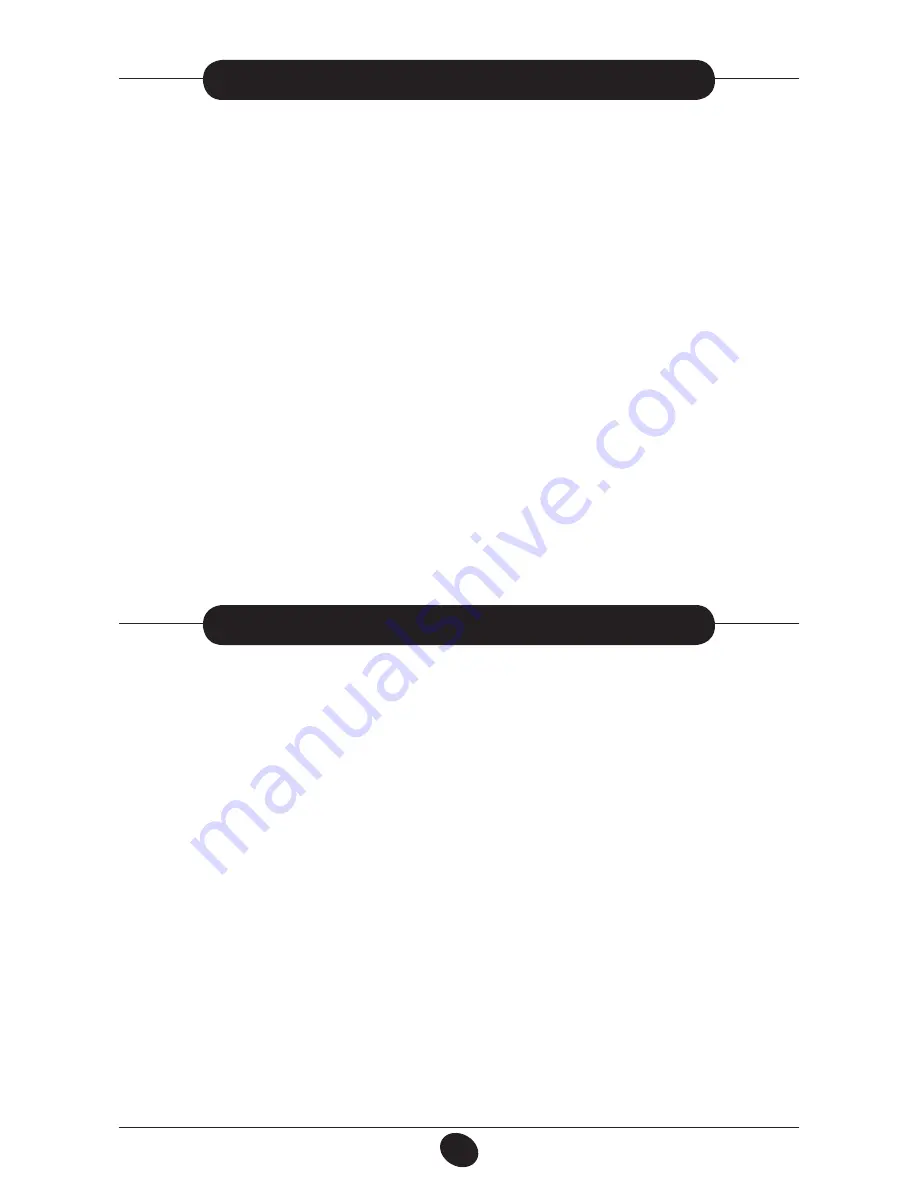
13
912.822.1 - GB
InstructIons pertaInInG to the InstaLLer
This boiler is designed to heat water at a lower than boiling temperature at atmospheric pressure. The boiler
must be connected to a central heating system and/or to a domestic hot water supply system in compliance
with its performances and output power.
IMPORTANT! The following components are not installed in the boiler as supplied. It is the installer’s
responsibility to provide them:
• Expansion vessel;
• Pressure safety valve;
• Circulation pump;
• Filling system cock.
Before connecting the boiler ensure the following operations have been completed:
a) Check that the boiler is fit for operation with the type of gas available. For more details see the notice on the
packaging and the label on the appliance itself.
b) Check that the flue terminal draft is appropriate; that the terminal is not obstructed and that no other applian
-
ce exhaust gases are expelled through the same flue duct, unless the flue is especially designed to collect
the exhaust gas coming from more than one appliance, in conformity with the standards and regulations in
force.
c) Check that, in case the flue has been connected to pre-existing flue ducts, thorough cleaning has been carried
out in that residual combustion products may come off during operation of the boiler and obstruct the flue
duct.
The following remarks and instructions are addressed to Service Engineers to help them carry out a faultless
installation. Instructions regarding lighting and operation of the boiler are contained in the ‘Instructions pertai-
ning to the user’ section.
Note that installation, maintenance and operation of the gas appliances must be performed exclusively by
qualified personnel in compliance with current standards.
Please note the following:
• Install the boiler in a permanent ventilated central heating boiler room.
• This boiler can be connected to any type of convector plates, radiators, thermoconvectors. Design the system
sections as usual though taking into account the available output / pump head performances, as shown in
chapter 10.4.
• Do not leave any packaging components (plastic bags, polystyrene, etc.) within children’s reach as they are
a potential source of danger.
• Initial lighting of the boiler must be effected by a Qualified Service Engineer.
• Make sure that the room where the boiler is installed has a sufficient supply of air to ensure complete combu
-
stion of the gas consumed by the appliance. Install unblockable ventilation grilles as necessary in accordance
with the Rules in force.
• Connect the boiler directly to an efficient flue to vent all fumes and combustion gases outdoors. Make sure
that the pipe connecting the boiler to the flue is not smaller in diameter than the boiler’s flue outlet. Make
sure that the flue is in good condition and free from holes or cracks that could reduce draw.
Failure to observe the above will render the warranty null and void.
8. general inForMation
9. instructions prior to installation