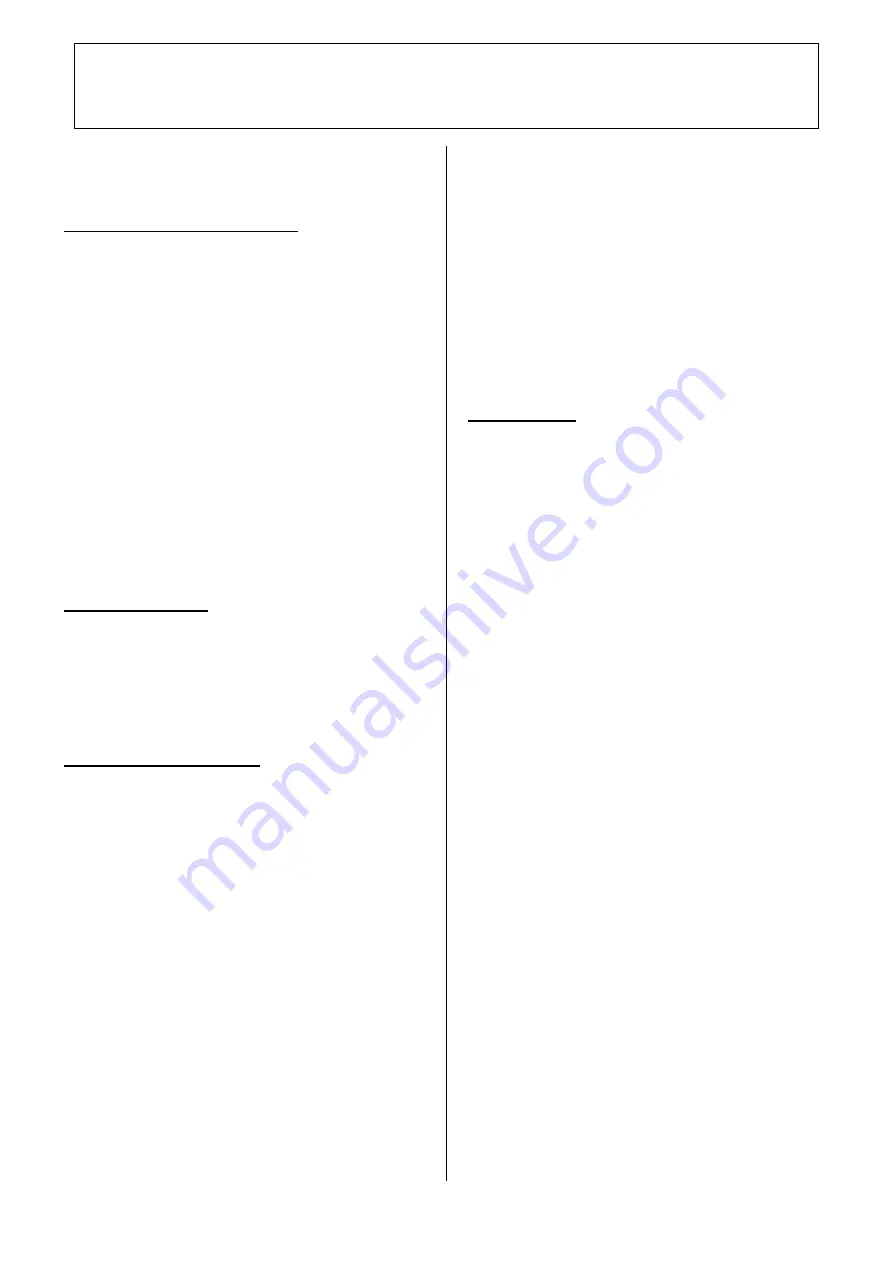
POTTERTON COMMERCIAL PRODUCTS DIVISION
SECTION 4
INSTALLATION, OPERATION AND MAINTENANCE MANUAL
DERWENT COMPACT PLUS – CONDENSING
PAGE 11
etc.). It must be possible for the condensate to drain
freely into a funnel. A trap must be installed between
the funnel and sewer system.
Connecting the Electrical Supply
The electrical supply should be 230V 1Ph 50Hz. A
6.3A fuse and a suitable two pole isolator having a
contact separation of at least 3mm in all poles has to
be provided by the installer for isolation of the boiler.
All on site wiring shall conform to IEE Regulations.
The live and neutral connections should be made to
the control panel terminal block. The earth connection
should be made 50mm longer. The length of the
conductors between the cord anchorage and the
terminals must be such that the current carrying
conductors become taut before the earth conductor if
the cable or cord slips out of the cord anchorage. The
wiring diagrams are included in this manual and also
on the door panel of the boiler.
For multiple boiler installations each boiler shall have
an isolator and fuse as detailed above to protect the
boiler and allow for maintenance.
Connecting the Flue
The fluehood has a vertical female outlet into which
the flue should be fitted and sealed fitted (dimensions
given in General Data). It is recommended that a
single skin stainless steel fully sealed flue system be
installed and the flue is suitable for condensing
boilers.
Connecting the Gas Supply
The connection should be made to the male
connection (size given in Table 2). A union and
isolating valve should be fitted close to the boiler to
allow disconnection of the boiler controls for
maintenance and repair.
The gas supply should be made through a suitable
meter and the local gas undertaking should be
consulted to determine the suitability of the meter and
gas supply to meet existing and additional demands
for gas.
The installation should be made in accordance with
the requirements of the Gas Safety (Installation &
Use) Regulations and all other regulations and Codes
of Practice
In particular, before connecting the boiler, ensure that
the gas supply has been purged of air and a manual
valve for isolation of the boiler is fitted in an accessible
position, readily identifiable, adjacent to the boiler.
The gas supply should be supported adequately.
For large single and multiple boiler installations
consideration should be given to the installation of
additional gas meters to assist in the monitoring of
boiler performance.
Attention is drawn to the need for adequately sized
pipework according to the maximum gas demand for
multiple boiler installations and each boiler shall be
provided with an isolating valve so that it is possible to
isolate the boiler from a common gas supply for
maintenance purposes. The gas train is fitted with a
low-pressure switch, which is set to operate at a
minimum gas pressure of 13mbar.
Boiler Controls
The operation of the boiler is under the control of it's
own control box, boiler thermostats, 2 air pressure
switches, gas pressure switch and overheat
thermostats.
In addition, the boiler should be controlled by a time
switch, frost thermostat, pump overrun facility and, for
multiple boiler installations, a boiler sequence
controller. The boiler can be controlled externally by
removing link D to G and providing a switch across
these terminals to control the boiler.
The high limit thermostat and burner lock out signals
can be picked up from terminals marked remote
indication. These are volt free contacts.
See boiler wiring diagram.
Summary of Contents for Derwent Compact Plus
Page 1: ...MAY 2004 ...