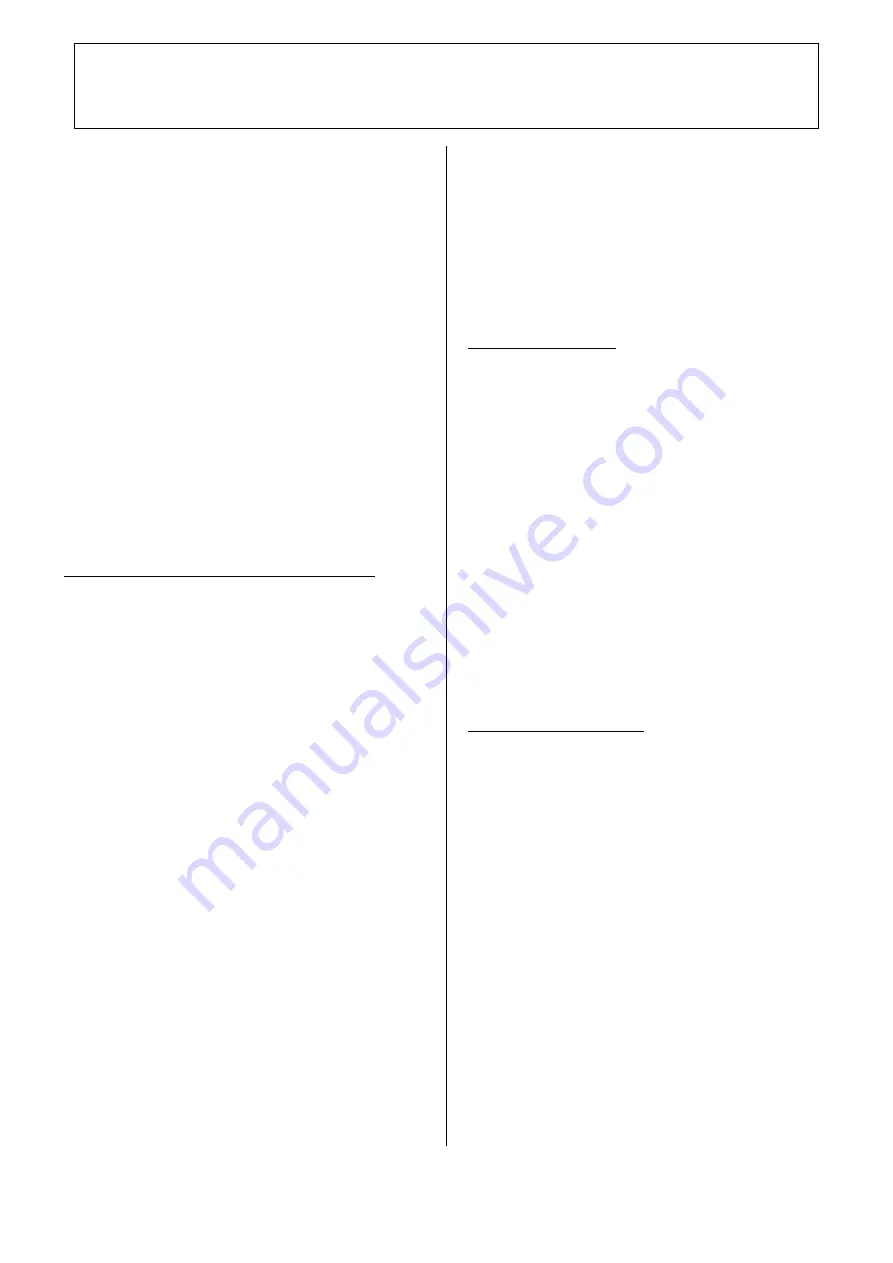
POTTERTON COMMERCIAL PRODUCTS DIVISION
SECTION 4
INSTALLATION, OPERATION AND MAINTENANCE MANUAL
DERWENT COMPACT PLUS – CONDENSING
PAGE 9
water and wash gently, in the case of eye contact,
flush abundantly with water, if irritation persists
seek medical advice.
2
High Temperature Glass Fibre Insulation
–
Wear gloves, overalls and safety glasses. In the
case of an irritation rinse the affected area with
water and wash gently, in the case of eye contact,
flush abundantly with water, if irritation persists
seek medical advice.
3
Adhesive
– Wear gloves, overalls. In the case of
an irritation rinse the affected area with water and
wash gently, in the case of eye contact, flush
abundantly with water, and if irritation persists
seek medical advice. Inhalation – continued
exposure should be prevented.
4
Sealing Rope
- Wear gloves, overalls. In the case
of an irritation rinse the affected area with water
and wash gently, in the case of eye contact, flush
abundantly with water, and if irritation persists
seek medical advice.
Potterton Commercial Customer Check List
The items listed below have been put together as a
guide to actions that should be completed before the
erection/assembly of a boiler takes place.
1 Site access available for persons carrying out the
proposed work.
2 Site Managers/Personnel aware that work will be
taking place.
3 Risk Assessments carried out on possible risks
which may effect the persons carrying out the
proposed work.
4 When boilers are to be stripped and rebuilt, labour
and transport should be provided for moving the
sections from the delivery point to the final
erection point. If this is unable to be provided
notice prior to attending site should be given.
5 Sections/casing etc, should be kept in a clean and
dry area prior to erection/assembly.
6 Water should be available.
7 A drain off area should be available.
8 Power should be available.
9 A site representative should be available at all
times.
10 Clear instructions supplied to the persons carrying
out the proposed work regarding positioning the
boiler.
11 Fire evacuation procedures, facilities availability,
specific Health & Safety information, etc, should
be provided.
Items 7 to 10 are essential if boilers require pressure
testing.
UNPACKING BOILER
For all boiler sizes remove the wooden box, shrink
wrap polythene and the cardboard protecting the
boiler. The boiler block is held to the pallet by fixing
brackets on the iron feet.
Before removing the boiler from the pallet a risk
assessment should be carried out to ensure safe
removal. This should take into account that any
person or persons moving or lifting boilers or any
part there of should be trained in manual handling
techniques and if necessary use suitable lifting
equipment to reduce the risk of injury to
themselves or other people.
When moving the boiler block into position the
burner assembly should be removed if there is
any likelihood of damage occurring.
Jacks and crowbars should not be used against
the flow and return manifolds.
Boiler Main Components
The boiler is composed of the following main
components:
1. Gas Valve assembly including intermittent pilot.
2. Low NOx burner bars.
3. Primary Heat Exchanger (Cast Iron).
4. Pipework assembly connection between primary
and secondary heat exchangers.
5. Secondary Heat Exchanger (Stainless Steel).
6. Damper for air flow control.
7. Fan.
8. Air pressure switches.
9. Hydraulic assembly for water flow distribution in
the secondary heat exchanger.
10. Control & Safety Equipment.
11. Set-up components.
Summary of Contents for Derwent Compact Plus
Page 1: ...MAY 2004 ...