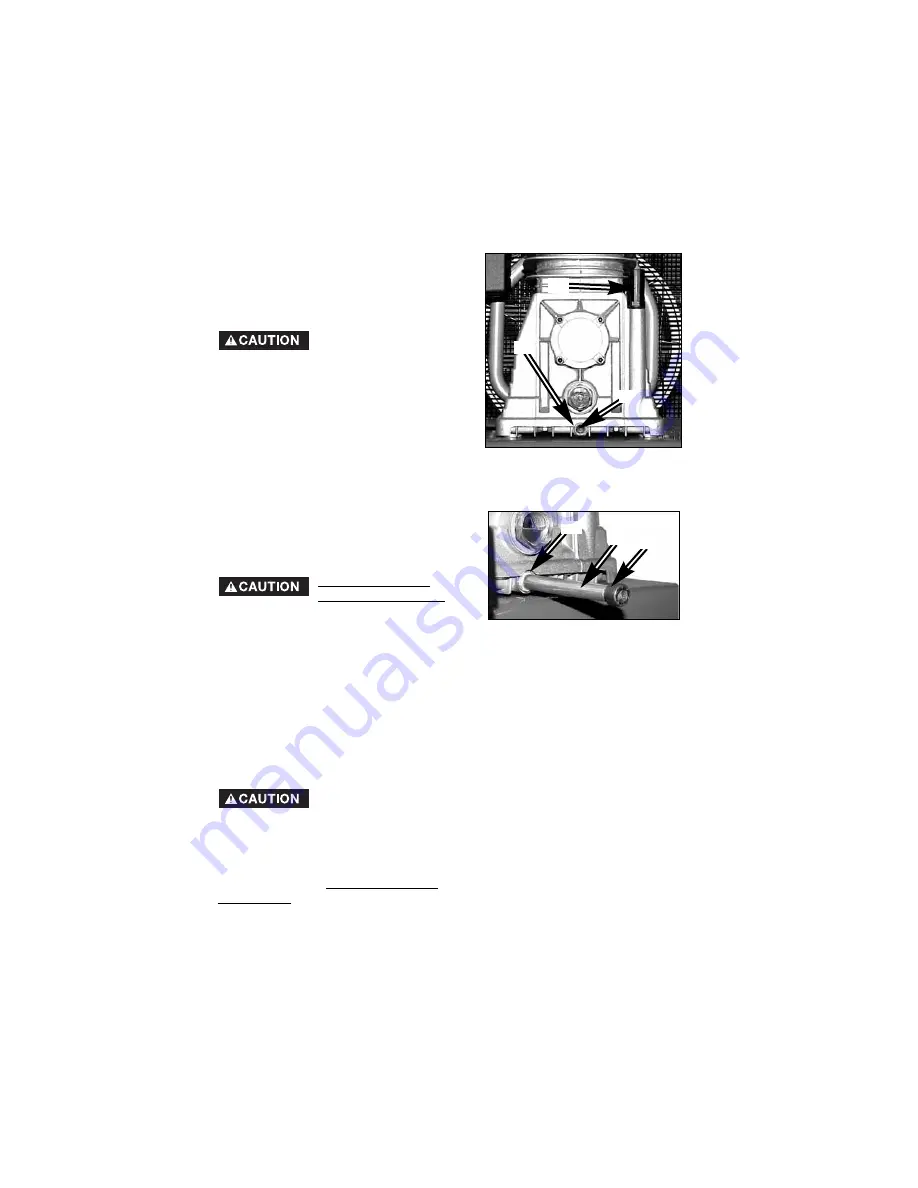
9-ENG
D22944
9-ENG
D22944
9-ENG
2. Obtain the drain plug extension
(D), from the parts bag.
3.
Apply thread sealant tape to the
threads of the drain plug exten-
sion (D).
4.
Assemble the washer (C), drain
plug extension (D), and drain
plug (B) as shown in Figure.
5.
Tighten securely.
6.
Remove the oil fill plug (A.
7.
Fill the crankcase with the rec-
ommended oil.
NOTE:
Use an air
compressor oil such as SAE-30
(API CG/CD heavy duty motor
oil). Under extreme winter condi-
tions use SAE-20 weight oil.
8.
Replace the oil fill plug (A) and
tighten securely.
A
C
B
ASSEMBLY
Tools Required for Assembly
1 - 9/16" socket or open end wrench
1 - electric drill
Unpacking
1.
Remove all packaging.
It may be neces-
sary to brace or
support one side of the outfit
when removing the pallet because
the air compressor will have a
tendency to tip.
2.
Remove and discard the (4)
screws and washers holding the
compressor to the pallet.
3.
With the help of another person
carefully remove air compressor
from pallet and place on a level
surface.
To Add Oil To Pump
Compressors are
shipped without oil.
A small amount of oil may be pres-
ent in the pump upon receipt of the
air compressor. This is due to plant
testing and does not mean the
pump contains oil. Do not attempt
to operate this air compressor
without first adding oil to the
crankcase. Serious damage can
result from even limited operation
unless filled with oil and broken in
correctly. Make sure to closely fol-
low initial start-up procedures.
Multi-Viscosity
motor oils, like
10W 30, should not be used in an
air compressor. They leave carbon
deposits on critical components,
thus reducing performance and
compressor life. Use air compres-
sor oil only.
1.
Remove the oil drain plug (B) and
washer (C).
C
D
B
9-ENG