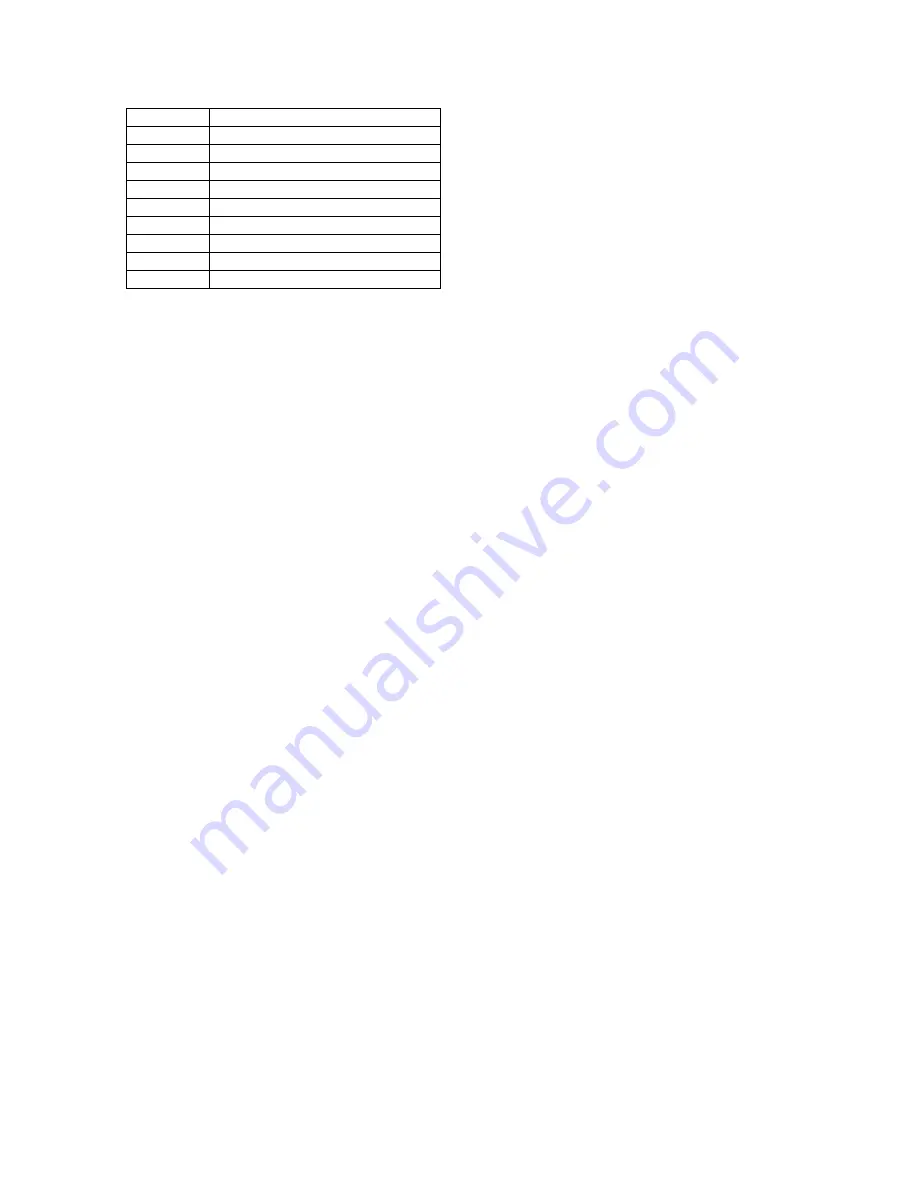
8
Type
Hydraulic fluid
Chevron
“Clarity” AW 15032
Exxon
“Univis” J 32
Mobil
D.T.E. 13 M
Gulf
“Harmony” AW-HVI-150-32
Shell
“Tellus T” 32
Texaco
“Rando” HDZ 32
Union
“Unax” AW-WR-32
Amsoil
AWH 15032
Sunvis
Low Pour H/032-product code 19300
Hydraulic fluid requirements
:
a)
Viscosity (fluid Thickness)
USA
METRIC
50 F 4450 SSU Max
10 C 95 Centistokes
100 F 130-200 SSU
38 C 27-42 C.S.
140 F 85 SSU Min.
60 C 16.5 C.S, Min.
Pour Point
- 10 F/-23 C Minimum (for cold startup)
Viscosity Index
(ASTM D 2220) 140 Minimum
Demulsibility
(ASTM D-1401) 30 Minutes
Maximum
Flash Point
(ASTM D-92) 340 F/171 C Minimum
Rust Inhibition
(ASTM D-665 A & B) Pass
Oxidation
(ASTM D943) 1000 Hours Minimum
Pump Wear Test
(ASTM D2882) 60 mg
Maximum
2.6 Tool Connecting Procedures
Stop the engine before connecting
the tool and, or hoses to the power
unit, and when switching hoses or
tools. Turn the hydraulic on/off valve
to the off position before starting the
engine. Make sure all hose are
connected for correct flow direction
to and from the tool being used.
When routing hose in the work area,
position them where personnel will
not be at risk of tripping over them or
where vehicles can run over the
hoses. Do not lay hose over sharp
objects.
WARNING: PRESSURIZED FLUID
ESCAPING FROM A DAMAGED
HOSE CAN PENETRATE THE
SKIN AND BE INJECTED IN THE
BODY CAUSING INJURY OR
DEATH.
CAUTION
:
DO NOT PULL ON
HOSES TO DRAG POWER UNIT.
2.7 Work Area Safety Precautions
- Never operate the tool when you
are tired, angry, emotionally
disturbed, or under the influence
of alcohol, drugs, medications, or
anything that could affect your
vision, alertness, coordination or
judgement.
- Establish a training program for all
operators to ensure safe
operation.
-
Do no operate the tool unless
thoroughly trained or under the
supervision of an instructor.
- Do not allow others to be near the
tool when starting it or while
operating. Keep bystanders and
animals out of the work area.
- Always wear safety goggles, ear,
leg, and head protection devices,
safety footwear, and snug fitting
clothes.
- Do not operate the tool near
energized transmission lines.
- Do not overreach. Maintain
proper footing and balance at all
times.