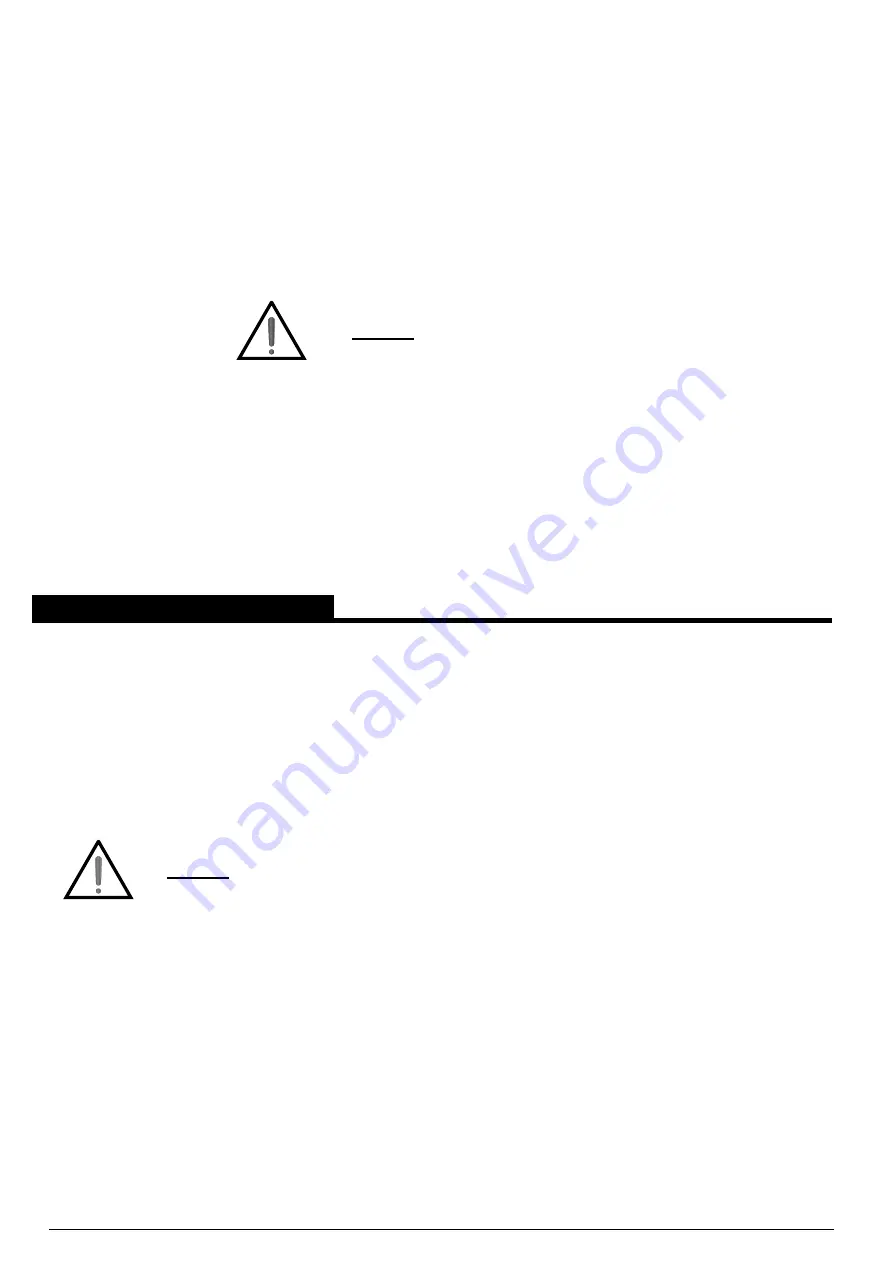
Operating manual liquid ring vacuum pumps TRVK - TRSK
20
NOTE:
HYDROSYS systems engineered with multiple pumps are fitted with isolating valves at suction, discharge, and
service liquid lines of each pump. When one or more pumps are not operating it is required to isolate the idle
pump(s) by closing these valves. When the pumps are put back into service the said valves (at suction and
discharge) must be opened.
11.2 - OPERATION
After starting the vacuum pump check the following:
- the vacuum level is as desired or adjust the flow regulating valve to the required vacuum
- flow and temperature of service liquid and/or cooling liquid are as expected (within 25% tolerance)
- motor does not draw more amperage than shown on its nameplate
- the pump-motor assembly does not have abnormal vibrations and noises such as cavitation
- the operating temperature at full load, does not exceed approximately 85°C
- there are no leaks from mechanical seals, joints and flushing or cooling liquid lines
- liquid level in separator is between the minimum and the maximum
- the packing stuffing boxes are correctly flushed.
NEVER OPERATE THE PUMP DRY!
If the gas discharge is not open to the immediate atmosphere but it is piped to other locations, the pump discharge should
be checked for back-pressures that could cause higher power consumption and loss of pump capacity
.
11.3 - SHUT DOWN
First close the service liquid flow and cooling liquid flow (if applicable) then shut down the circulating pump (if there is one).
Where possible, gradually decrease the vacuum level to 400/900 mbar in about 10 seconds max.
The discharged service liquid from pump helps producing a slow deceleration rather than sadden stop
.
Turn off the power to motor and close any accessories and flushing lines.
Make sure the non return valves, or similar, at suction and discharge lines are leak tight.
Should the system be idle for an extended period of time it is recommended to disconnect the electricity to the motor
panel, drain all liquids from pump, separator and piping. Refer to chapter 6 for storage procedures.
12 - OPERATING MAINTENANCE
Periodically check the working conditions of the system by means of the instrumentation on the installation (pressure
gauges, vacuum gauges, temperature gauges, ampmeters, etc.) and if the pump is consistently handling the application
for which it was selected.
The operation of the pump should be without abnormal vibrations or noises, if any of these problems is noticed, the pump
should be stopped immediately, search for the cause and make the necessary corrections.
It is good practice to check the pump/motor alignment, the running conditions of the bearings and of the mechanical seals
(see chapter 13) at least once a year, even if no abnormalities have been noticed.
If there is a deterioration of the pump performance, which is not attributable to changes in system demands, the pump
must be stopped and proceed with necessary repairs or replacement.
If the mechanical seals are fitted with external flushing and/or quenching lines their pressures, temperatures and flows
must be checked constantly.
NEVER ALLOW THE PUMP TO OPERATE IN THE CAVITATION AREA!
Cavitation has the characteristic metallic sound, like if gravel was rotating inside the pump, and it causes also high pump
vibrations. This happens when the pump is running at absolute pressures close to the vapour tension of the service liquid
at the running conditions.
This is a damaging condition for the impellers, port plates and casings. The cavitation causes erosion taking away metal
particles and attacking the surface of the pump components. This is particularly damaging if the pump is handling
corrosive gases, see chapter 14 for suggestions to correct the problem.
The pump series TRVK can be pre-fitted with an anti-cavitation system.
Such a system allows connection of each discharge plate (at the gas discharge port side) to the upper part of the separator
tank so that only air can be aspirated when the limits of cavitation are reached.
Alternatively, the above-mentioned connection can be fitted with a valve for the introduction of air to the pump.
Such a system permits a reduction in cavitation without excessively reducing the performance of the pump while
guaranteeing high vacuum.
During operation it must be avoided to have sudden and frequent variations from high to low vacuum. (e.g.: suddenly
opening the suction valve when the pump is operating at pressures lower than 200 mbar).
This would flood the pump creating high power absorption that would put heavy stress on the motor and coupling.
Particular attention should be put on the quantity of the service liquid flow. The flow will depend upon the type of installation
(see chapter 9), the pump size, and/or the desired temperature rise.
Summary of Contents for TRSK 2002/1
Page 1: ... NA4 IS VUOC IN00 Rev 3 8_11 2020 OPERATING MANUAL LIQUID RING VACUUM PUMPS TRVK TRSK ...
Page 10: ...Operating manual liquid ring vacuum pumps TRVK TRSK 10 90 OK NO Fig 2 Fig 4 Fig 1 Fig 3 ...
Page 28: ...Operating manual liquid ring vacuum pumps TRVK TRSK 28 blank page ...
Page 29: ...Operating manual liquid ring vacuum pumps TRVK TRSK 29 blank page ...
Page 30: ...Operating manual liquid ring vacuum pumps TRVK TRSK 30 blank page ...