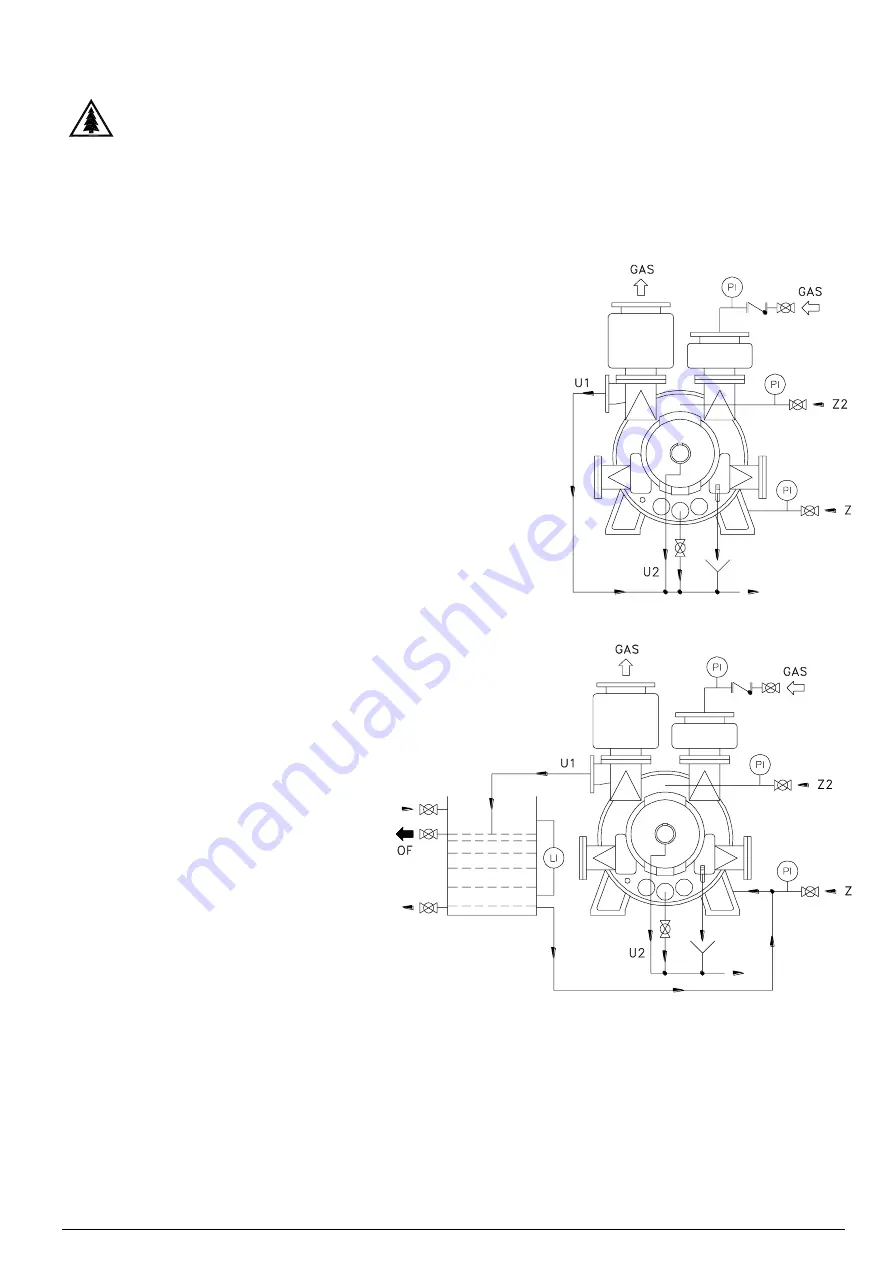
Operating manual liquid ring vacuum pumps TRVK - TRSK
17
9.3 - INSTALLATION SCHEMATICS FOR LIQUID RING VACUUM PUMPS
The working principle of the vacuum pump requires a continuous flow of fresh and clean liquid that enters the pump at
the service liquid connection identified by the letter “Z” (see following chapter). The liquid is discharged together with the
handled gas through the pump discharge flange.
Take care of their disposal according to the laws into force and to a safe local environment management.
The quantity of said liquid will vary with pump size and degree of working vacuum (see performance curves).
The service liquid absorbs the compression heat generated by the pump compression therefore its temperature will rise
by some 4°C to 8°C according to working point.
There are three basic installation schematics listed below that may be considered, depending upon the quantity of service
liquid that is desired and possible to be recycled.
9.3.1 - Service liquid: Once-through system (no recovery)
All the service liquid is supplied from an external source.
The liquid is separated from the gas in the manifold separator and drains
directly through the discharge connection located at the bottom of the
manifold separator itself.
This is the most common installation scheme and can be applied when it
is available an abundant constant flow of fresh liquid and/or when the
liquid contamination problem never exist, liquid that can be harmful for the
surrounding environment: therefore provide a proper disposal according
to laws into force.
The service liquid should be supplied at the pump connection with a
pressure of 0.2 to 0.4 bar maximum to avoid flooding the pump with too
much liquid.
If this is not possible it is recommended to install a reservoir fitted with a
float valve, this tank is supplied with the liquid that is then pulled by the
pump as required by the operating conditions.
The liquid level in the reservoir should be approximately at the pump shaft
centreline.
Schematic fig. 18 illustrates the once-through system.
9.3.2 - Service liquid: Partial recovery system
This type of installation is used where it is
desired to minimise the use of fresh service
liquid.
The service liquid enters and leaves (take care
of its eventual disposal according to the laws
into force and to a safe local environment
management) the pump same as the once
through system, however part of the liquid is
recycled from the discharge separator and the
balance is continuously supplied from an
external source. The excessive liquid is drained
through the separator overflow connection.
The temperature of the mixed liquid supplied to
the pump will be higher than the temperature of
the make-up liquid. Its final temperature will
depend upon the amount of the recycled liquid.
It is important to remember that with higher
service
liquid
temperature
the
pump
performance will decrease (see chapter 17)
with the possibility of operating the pump in the
cavitation area.
When the separator tank is installed along side
of the pump (our type HSP), its liquid level
should not be above the pump shaft centreline.
Schematic fig. 19 illustrates the system with partial recovery of the service liquid.
C
= Cooling circuit
OF
= Overflow
U1
= Service liquid discharge
U2
= Packing flushing liquid discharge
Z
= Service liquid inlet
Z2
= Inlet flushing liquid for packing
Fig. 18
Fig. 19
Summary of Contents for TRSK 2002/1
Page 1: ... NA4 IS VUOC IN00 Rev 3 8_11 2020 OPERATING MANUAL LIQUID RING VACUUM PUMPS TRVK TRSK ...
Page 10: ...Operating manual liquid ring vacuum pumps TRVK TRSK 10 90 OK NO Fig 2 Fig 4 Fig 1 Fig 3 ...
Page 28: ...Operating manual liquid ring vacuum pumps TRVK TRSK 28 blank page ...
Page 29: ...Operating manual liquid ring vacuum pumps TRVK TRSK 29 blank page ...
Page 30: ...Operating manual liquid ring vacuum pumps TRVK TRSK 30 blank page ...