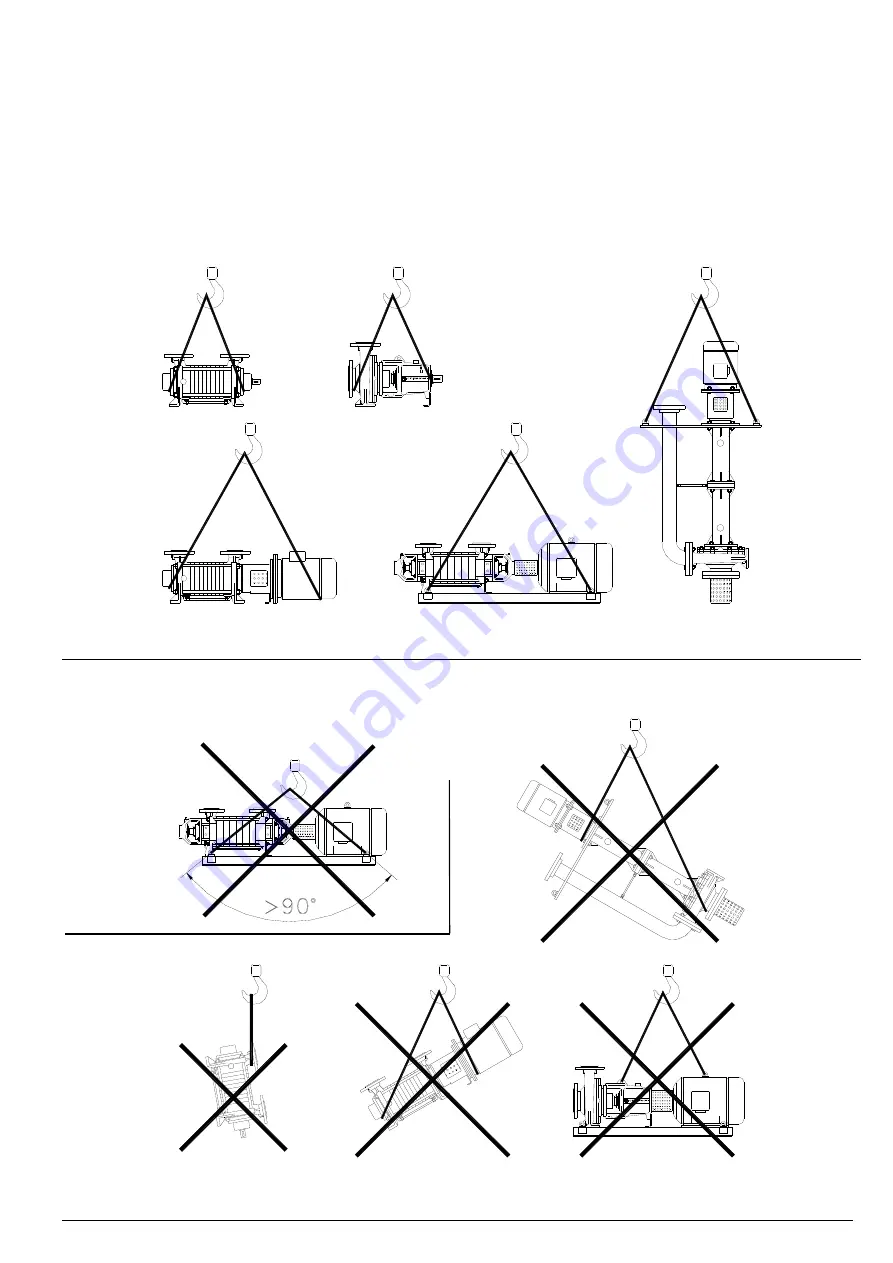
Operating manual for centrifugal pumps AT - TB… - MC… - TC… - TMA
9
Even if the machine is properly stored, as described in the instructions above, in case of long term storage the
following instructions must be taken into account.
After a storage period of 6 months the lubricant should be replaced completely.
In case of a storage period longer than 12 months, the machine shall be carefully checked and inspected
before installation. Following actions should be considered particularly:
- complete replacement of lubricants
- inspection of the bearings, they should be cleaned if necessary
- inspection of O-rings and gaskets (it is recommended to replace them)
- inspection of mechanical seal integrity (replace if necessary).
Fig. 1
Fig. 2
Fig. 3
OK
NO