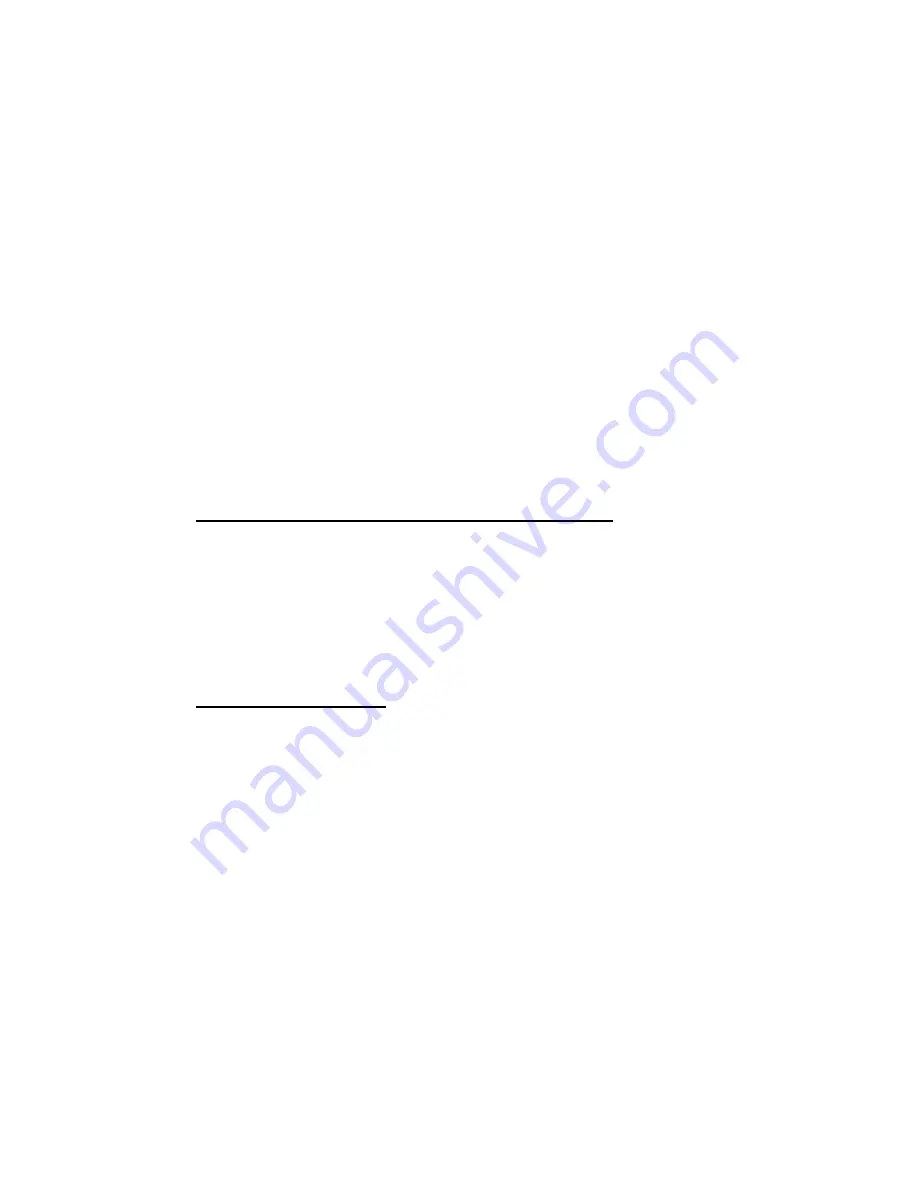
bottom side of the base plate on the OC2-500 control to facilitate heat transfer.
When mounting in the enclosure, select an area that will minimize the possibility
of metal parts falling between the PC board and OC2-500 base plate, or on the PC
board and thereby causing shorts. Since the enclosure wall or sub-panel is actually
used by the OC2-500 as a heat sink, it is necessary that the panel be of sufficient
size to furnish adequate cooling. If a single OC2-500 is placed in an unventilated
enclosure with no other heat-generating equipment, a 20”x20” enclosure of
minimum clearance depth is of adequate size. The top edge of the OC2-500 base
plate must be located at least 4” below the top surface of the enclosure. If these
conditions are met, no fans need to be used.
If other equipment which generates significant heat is installed in the cabinet with
the OC2-500, however, increase enclosure size or add a circulating fan to
distribute heat within the enclosure. In all cases, though, it can be determined if a
larger enclosure and/or fan will be needed by measuring the power cube base
plate temperature. The power cube base plate temperature under all conditions
cannot exceed 100
°
C
.
4.2
MOUNTING OF ENCLOSED OC2E-500 CONTROL
The enclosed OC2E-500 control must be mounted in an environment that does not
exceed 40
°
C. Since this control uses the back of the box for cooling, the control
must be mounted in a location to permit airflow over the back of the enclosure. It
is mandatory that the OC2E-500 enclosure back be spaced at least one-half inch
from any air restricting or thermally non-conductive walls. Spacers are provided
with the control to permit proper mounting. Refer to Figure 3.
4.3
WIRING PROCEDURE
Use drawing A1501-100-ES ( Figure 4) on open chassis controls and A1436-000-
WD (figure 3) on enclosed controls for proper external wiring connections. The
rated RMS current for 5 horsepower control is given in these wiring diagrams. All
wires which carry armature current are sized the same as those carrying AC line
current. (This is necessary to account for the form factor of the current being
supplied to the armature of the motor.) All other wire connections may be # 18
AWG.
On enclosed controls the AC input connections are made to 3TB. On open chassis
controls the input connections are made directly to the double fuse holder. For
open chassis controls, wire connections to terminal strip 1TB on the printed
circuit board are not to be lugged.
4