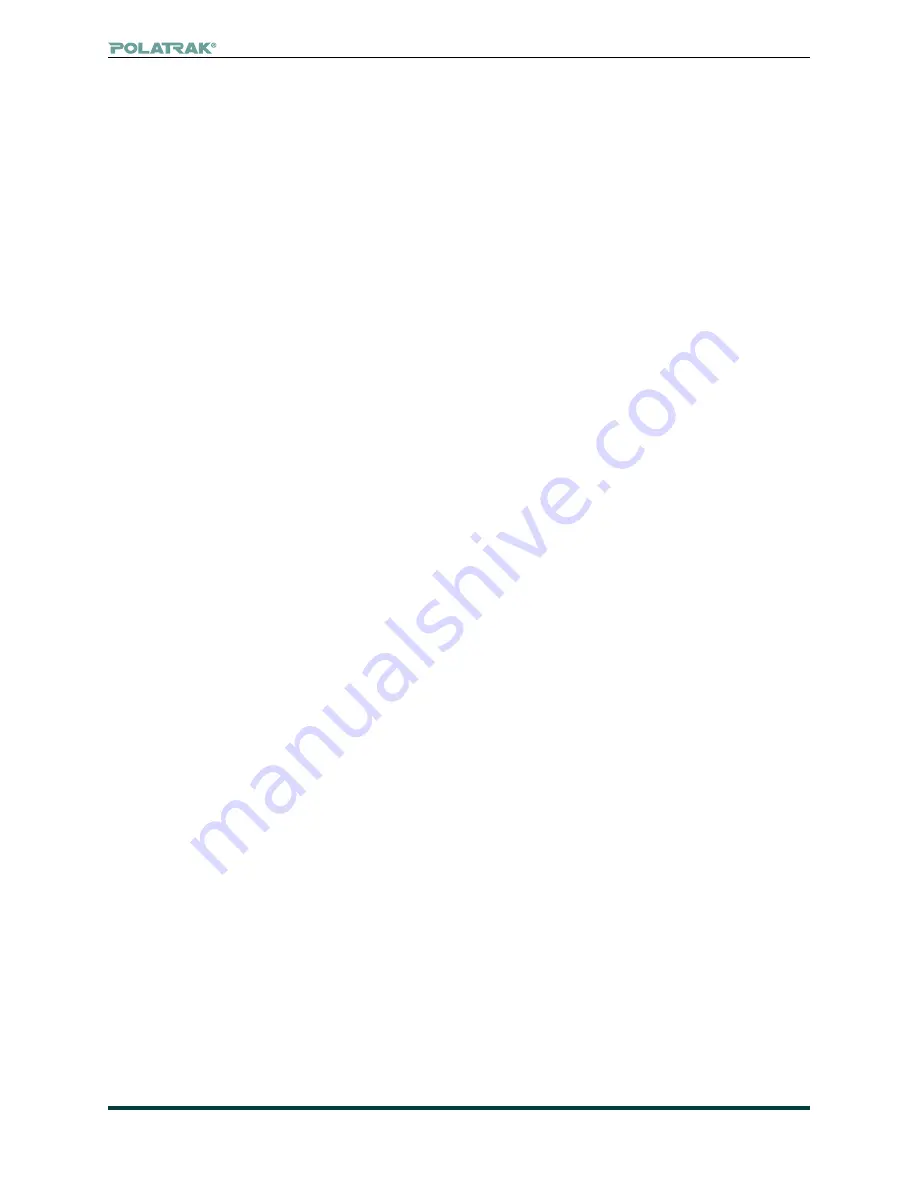
www.polatrak.com
|
13813 FM 529 Rd, Houston, TX 77041 USA
|
Telephone: +1 (713) 983 7117
|
Email: [email protected]
©
2015 Deepwater Corrosion Services Inc. Specifications subject to change without notice
Deep C Meter 300 AD™
operation manual
9
SMB-001 Deep C Meter 300 AD Manual
7.4. Online subsea check
7.4.1
While free-flying, the top and middle display lines are reading the potential of the stainless
contact tip. This number will vary depending on ROV speed, time of immersion and whether a
protected structure has been recently stabbed. Normally, the reading will be in the (-) 0.200V to (-)
0.400V range. However, both meters should be within 0.010V of each other. This number should
not be more negative than (-) 8.800V.
NOTE: If instrument fails calibration check, go to troubleshooting section 13 in this manual.
8. Operation
8.1
Mounting on ROV
8.1.1
Create the power lead from the 4 pin open-ended cable whip and splice on the required
connector to interface with the ROV MUX bottle. See section 6.0 for the correct pin outs.
8.1.2
Verify the whip has power and perform a loop-back test before attaching the unit directly to
ensure the data stream is not corrupted. See Table 6 if communication cannot be established.
8.1.3
Find a good location on the vehicle to mount the Deep C Meter 300 AD™ and attach the
articulated mount. Typically, the display unit should be in view at the same time as the probe unit
to maximize efficiency. Alternatively, a second camera can be dedicated to the display unit. The
LED readout must be visible by the camera; also, having a light source directed at the lens for
optimal visibility is recommended.
8.1.4
If using zoom cameras, position the camera approximately 12” away from the edge of the lens.
8.1.5
If using fixed-zoom cameras, physically position the camera approximately 0.5” to 3” away
from the edge of the lens.
8.1.6
Ensure that all fasteners are tightly secured and in good condition. Verify that all lock nuts
and washers are in place on the readout unit mount.
8.1.7
Connect and route the power lead.
8.1.8
Insert the probe unit into the T-handle and position in a manipulator or tool basket that is
manipulator accessible.
8.1.9
If the EFG probe has been purchased, the unit can be piggy-backed onto the ROV-II probe
using the supplied brackets.
8.1.10
Tying a safety lanyard to the T-handle is recommended.
8.1.11
Ensure that lock rings for the flying lead(s) connectors are properly mounted and secured.
8.1.12
Ensure that all fasteners are tight and the lock nuts are in place on the T-handle.
8.1.13
Route the flying lead(s) in such a way that they will not be stressed, entangled or pinched
during manipulator operation.
8.1.14
Using the provided connector sealant, apply a small amount to the shoulder of each flying
lead(s) connector, ensuring that no sealant is applied to the copper pin. Connect the flying lead to
the probe lead and tighten the connector lock ring. Please refer to the MSDS in the appendix be-
fore handling sealant. All appropriate Personal Protective Equipment (PPE) shall be worn including
safety glasses and gloves as a minimum precaution.
8.1.15
Mount a zinc ROV calibration coupon on the ROV’s front porch or manipulator in an area
the contact tip can easily reach during subsea calibrations.
8.1.16
Ensure the calibration coupon is electrically isolated from the ROV (Over 1MΩ).
8.1.17
Remove the lens cover from the instrument.
8.1.18
Perform a bucket calibration (see section 7.2).