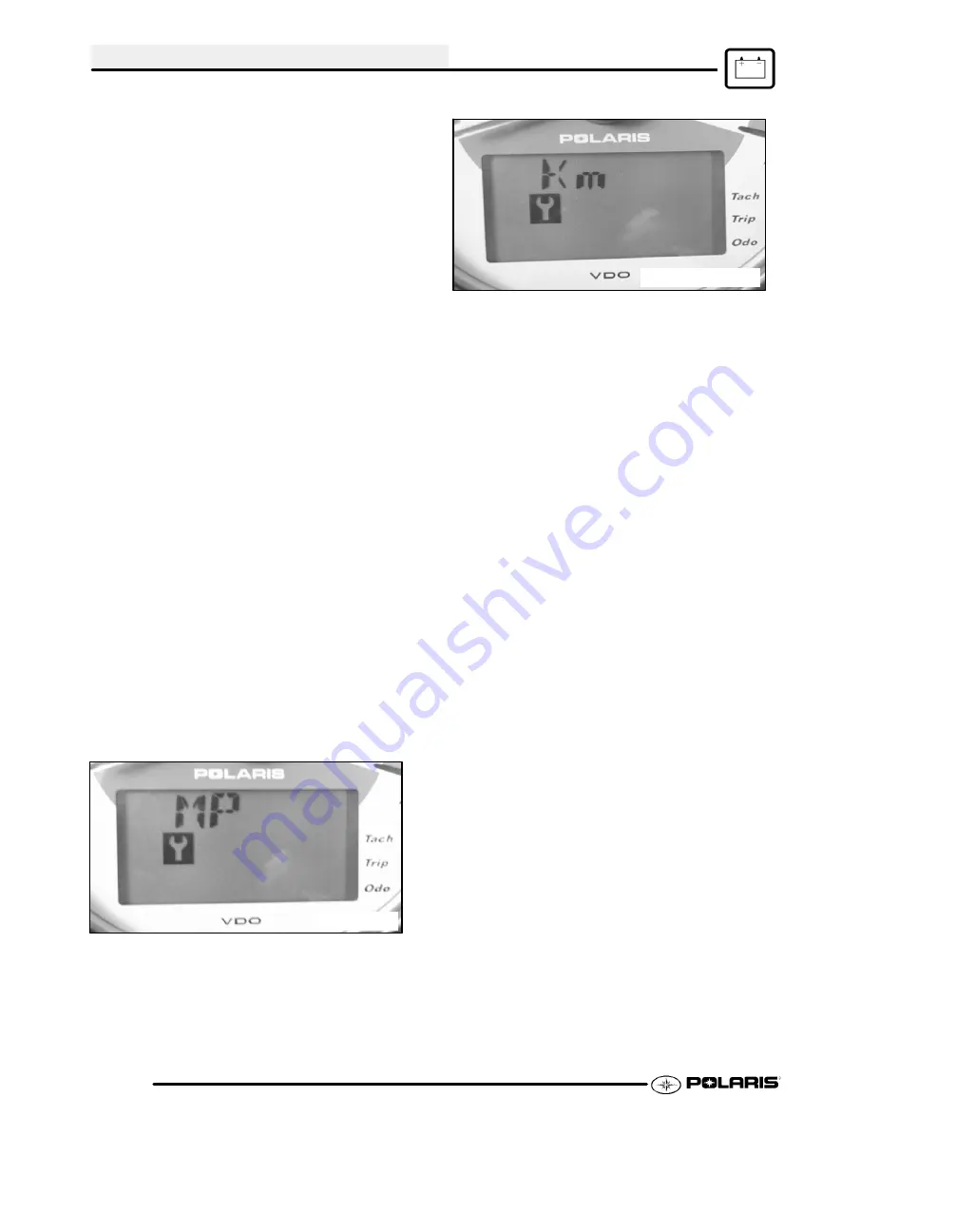
ELECTRICAL
10.8
3. When the desired time increment is displayed,
release the button and wait for the wrench to stop
flashing. When the wrench stops blinking, your
service hours are set.
NOTE:
If you scroll past the intended number, hold
the button down until the count turns over to
0
. You
can then reset the number.
Turn Service Interval OFF:
1. If the service interval is enabled (functioning) on
your ATV and you wish to turn it off, toggle to the
service interval mode.
2. Press and hold the mode button for approximately
7 seconds until the word
OFF
appears in the Rider
Information Center. The service interval is now off.
3. To enable (turn on) the service interval mode,
repeat the steps above in “Setting Service Interval
After Countdown”.
Change Service Interval Time:
If you would like to change the service interval time,
(for example change the interval from 50 hrs. to 55
hrs.). Follow the steps below:
1. While in the service interval mode, press and hold
the mode button for approximately 7 seconds until the
word
OFF
appears in the Rider Information Center.
2. Wait 5 seconds and then press the mode button in
until the wrench icon flashes. Press the mode button
again to set the desired service increment. Release
the button and wait for the wrench icon to stop
flashing. The new service interval is now set.
Screen 6: Miles/Kilometers
toggle, The display in
the trip meter and odometer can be changed to
display either kilometers or miles. The current display
mode will be shown as “KM” or “MP”. To change, hold
in the mode button until the letters flash, then press
and release the button once. When the display stops
flashing, the mode has been set.
MP = Miles
Km = Kilometers
*NOTE:
As long as you are in the diagnostic mode,
the wrench icon will remain lit.
*NOTE:
To leave the diagnostic mode, turn the key
switch off and on.
Summary of Contents for 2005 SPORTSMAN 400
Page 60: ...MAINTENANCE 2 40 MAINTENANCE SCHEDULE Service Date Hours Miles Service Performed Serviced By...
Page 80: ...ENGINE 3 20 CYLINDER HEAD EXPLODED VIEW EH50PL A EH50PL...
Page 188: ...CLUTCHING 6 36 NOTES...
Page 260: ...BRAKES 9 24 NOTES...
Page 303: ...ELECTRICAL WIRING DIAGRAM 2005 SPORTSMAN MODELS...
Page 304: ...ELECTRICAL WIRING DIAGRAM 2005 SPORTSMAN MODELS...
Page 312: ...31 25 3ULQWHG LQ 86...