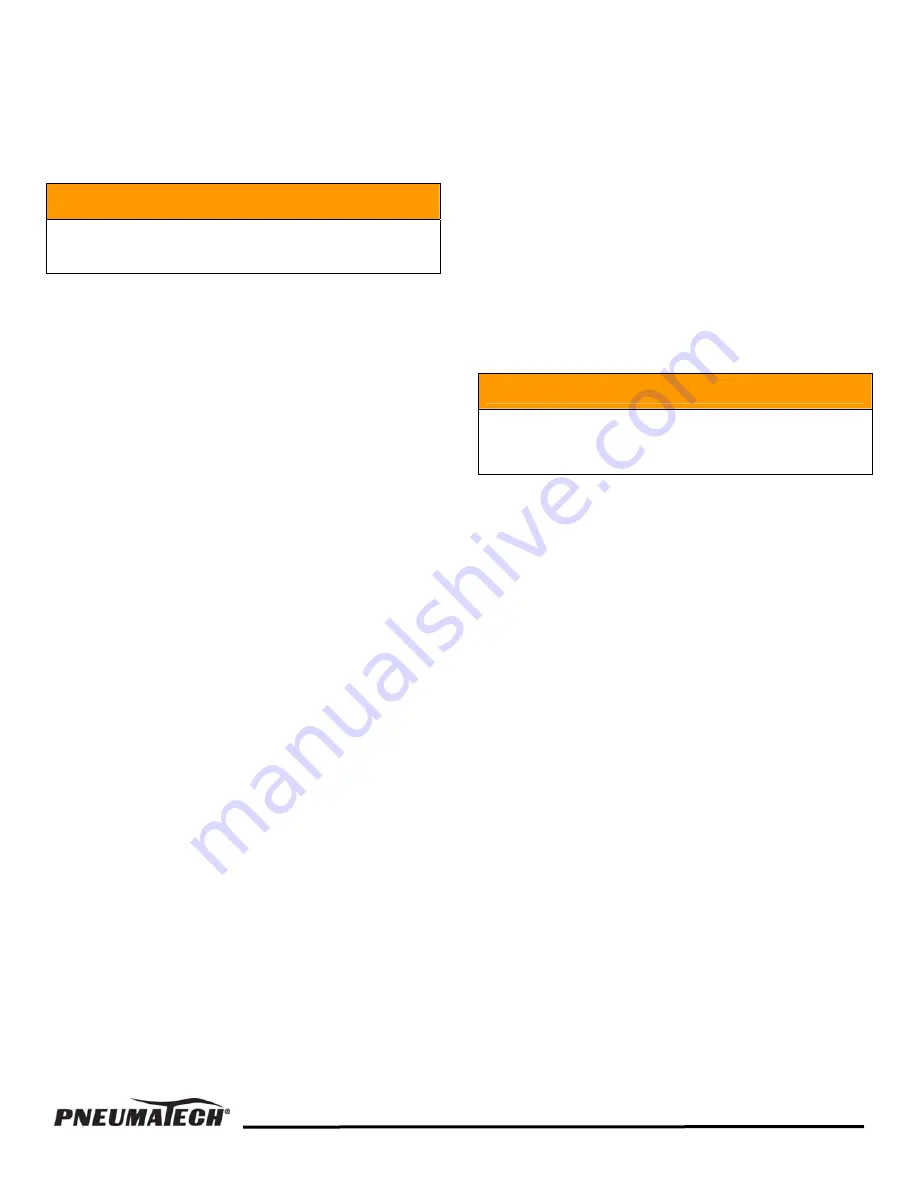
3
GENERAL INFORMATION
The Pneumatech Air Drying System is designed to cool
and remove moisture from compressed air. When
properly installed, the unit requires little maintenance or
adjustment.
WARNING
Do NOT install, operate, maintain, adjust or service
this unit without thoroughly reading this manual.
This manual contains important safety information. Read
THOROUGHLY and follow the Safety Instructions
provided in this manual and posted on the unit. Keep this
manual near the unit and in a safe place. Replace this
manual if it becomes torn or dirty and cannot be properly
used.
Please read the Installation Instructions and Start-up and
Operation sections of this manual before attempting to
operate the unit.
Please read the Maintenance and Troubleshooting
sections of this manual before beginning any
maintenance or service work on this unit.
INSPECTION
Inspect equipment. Any concealed shipping damage
must be reported to the carrier immediately. Damage
claims should be filed by the consignee with the
carrier.
SAFETY INSTRUCTIONS
When using air compressors and compressed air
accessories, basic safety rules and precautions must
always be followed, including the following:
1.
READ ALL INSTRUCTIONS FULLY.
2.
WIRING & BREAKERS
Wiring, breakers and other electrical equipment must
conform to local and national electrical codes. Do
not operate this unit with damaged wiring or after the
unit or air handling parts have been dropped or
damaged in any manner. Notify authorized service
facility for examination, repair or other adjustments.
3.
USE SUITABLE PARTS & ACCESSORIES
Do not use air pressurized accessories or parts in
the air system not suitable for the maximum air
pressure.
4.
RELEASE AIR PRESSURE SLOWLY
Fast moving air will stir up dust and debris, which
may be harmful. Release air pressure slowly when
depressurizing your system to avoid bodily injury.
5.
SECURE DRAIN LINES
Fasten drain lines to floor or drain. Pressurized air
may periodically pass through drain lines, which will
cause an unsecured line to whip and may cause
bodily injury.
WARNING
Air from compressor and from Pneumatech Air
Drying System, as equipped, is not safe for human
respiration (breathing).
To provide safe, breathable air, compressor must be
capable of producing at least Grade D breathing air as
described in Compressed Gas Association Commodity
Specification G7.1-1966. Special filtering, purifying and
associated alarm equipment must be used to convert
compressed air to “Breathing Air.” Other special
precautions must also be taken.
Refer to OSHA 29 CFR 1910.134.
DISCLAIMER OF WARRANTY
If this unit is used to produce breathing air, the special
equipment and precautions expressed in OSHA 29 CFR
1910.134 for specifications of the necessary equipment
and special precautions to make Breathing Air MUST BE
used or any warranties are VOID and manufacturer
disclaims any liability whatsoever for loss, personal
injury or damage.
Summary of Contents for AD Series
Page 15: ...14 FIGURE 6 FLOW DIAGRAM AD 750 to 1000 ...
Page 16: ...15 FIGURE 7 FLOW DIAGRAM AD 1200 to 2000 ...
Page 17: ...FIGURE 8 FLOW DIAGRAM AD 2500 to 4000 16 ...
Page 22: ...21 ...
Page 23: ...22 ...