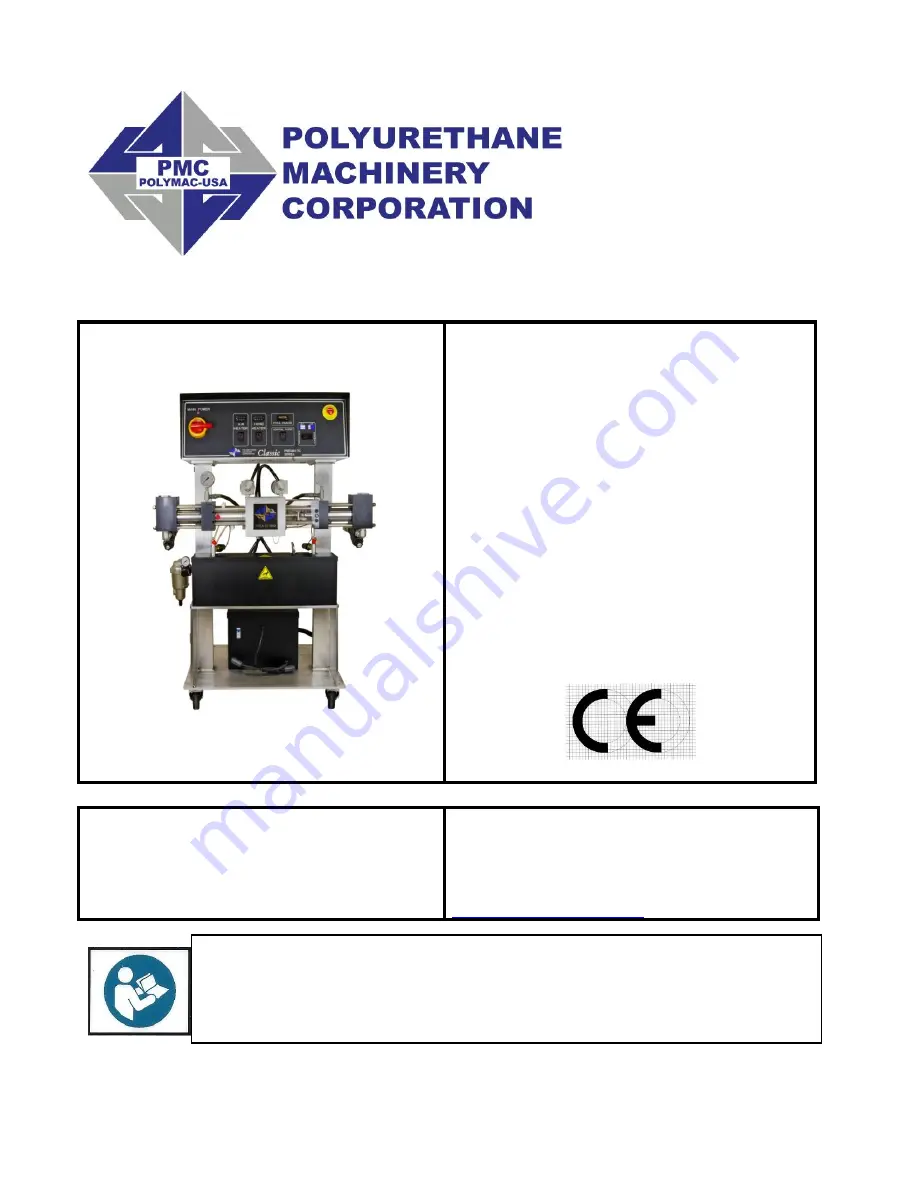
PMCA-20
Proportioner
Manual
Pneumatic, Heated, Plural Component
Proportioner
For spraying Polyurethane Foam and
Coatings
For Professional Use Only
Not approved for use in
Explosive atmosphere locations
Ref. # MN-06001
REVISION 1.0
Polyurethane Machinery Corp.
Headquarters: 1 Komo Drive, Lakewood NJ 08701
Manufacturing: 2 Komo Drive, Lakewood, NJ 08701
Phone: 732-415-4400 Fax: 732-364-4025
Before installing the PMCA-20 Series Proportioner and start-up, carefully read all the
technical and safety documentation included in this manual. Pay special attention to the
information in order to know and understand the operation and the conditions of use of the
PMCA-20 Series Proportioner. All of the information is aimed at improving user safety and
avoiding possible breakdowns from the incorrect use of the PMCA-20 Series Proportioner.
Summary of Contents for MN-06001
Page 11: ...PMCA 20 Manual 11 DESCRIPTION PMCA 20 ...
Page 43: ...PMCA 20 Manual 43 DOUBLE ACTING PROPORTIONING PUMP DIAGRAM FILL STROKE DISCHARGE STROKE ...
Page 44: ...PMCA 20 Manual 44 PART IDENTIFICATION Pump Line Assembly PL 4 PL 5 ...
Page 46: ...PMCA 20 Manual 46 Air Motor Assembly NE 06009 ...
Page 52: ...PMCA 20 Manual 52 Pre Heater Assembly PH 13 ...
Page 55: ...PMCA 20 Manual 55 Air Machine PMCA 20 1600 PMCA 20 2400 ...
Page 56: ...PMCA 20 Manual 56 ...
Page 61: ...PMCA 20 Manual 61 Hoses ...