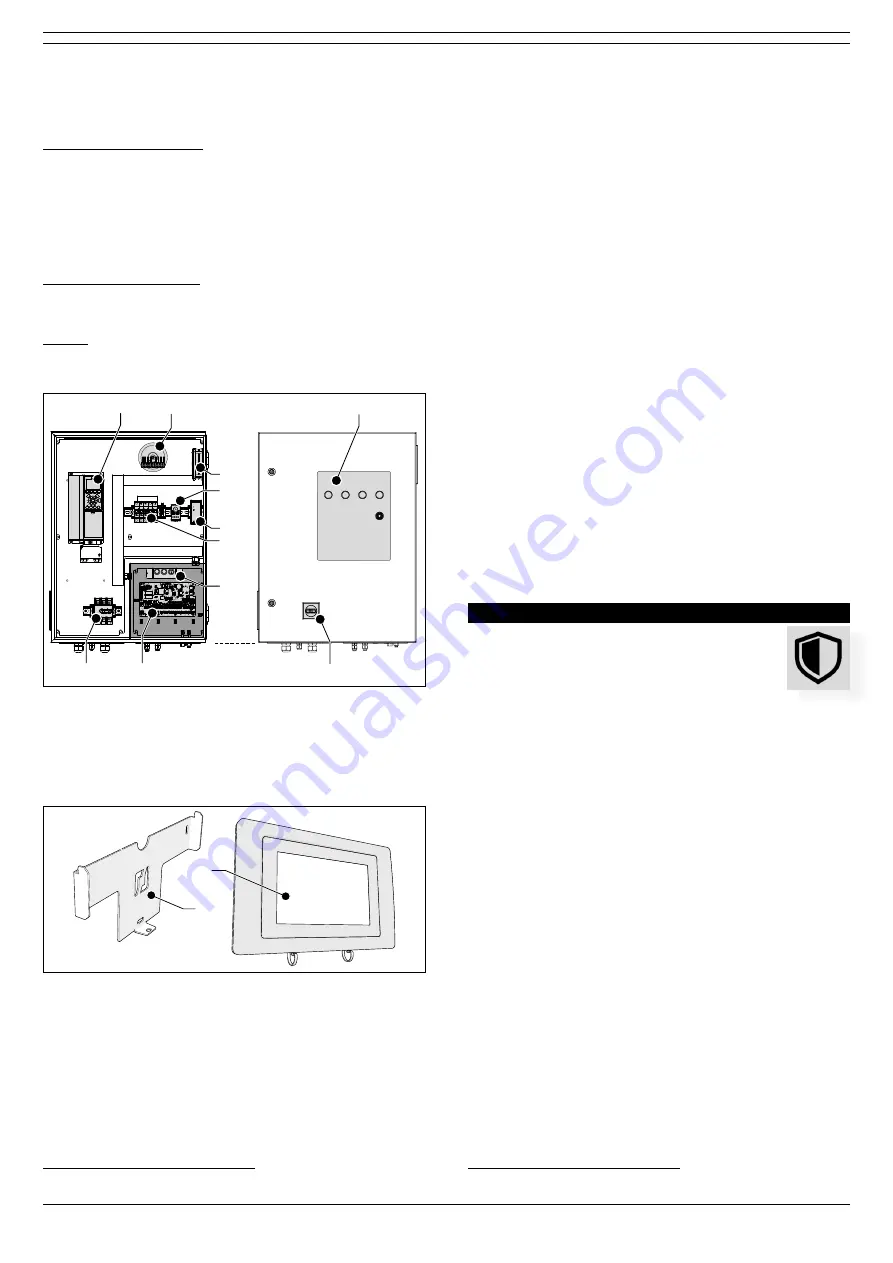
0000300349/230420/0 MDB-Diluter PRO
4
2.1.2 Control equipment
Panel
High voltage compartment
A VFD (frequency inverter)
B Transformer
C Cooling fan
D Thermostat
E Switch mode power supply
F Circuit protectors
3
G Main switch (interior parts)
Low voltage compartment
H PC board
I Manual controls
Outside
J Status panel
K Main switch (exterior parts)
Fig. 2.1
A
B
G
I
F
D
C
H
J
K
E
Main components Panel
HMI
A Touch screen
B Mounting bracket
Fig. 2.2
A
B
Main components HMI
Connection cables
- Panel
HMI cable
- motor cable
- PTC cable
- control cable (connected to the compressed air switch)
3. CE (400V): circuit breakers | UL (480/600V): fuses
2.2
Operation
2.2.1 MDB-Diluter
The air -that contains welding fume- is extracted through the
air inlet module on top of the unit. The larger particles and any
sparks are separated by a labyrinth-shaped
4
spark arrester.
Subsequently the air is cleaned by the eight filter cartridges.
The air then passes the extraction fan and a duct silencer. The
clean air is blown back into the workshop by the outlet unit
with adjustable nozzles.
The filter cartridges are cleaned individually from the inside
out by compressed air pulses. This filter cleaning system is
called the RamAir™ pulse amplifier. The dust and dirt particles
are collected in the dustbin.
The fan speed is pressure controlled.
Apart from air cleaning, the system optimises the present
natural ventilation (draught) and/or forced ventilation (roof/
wall fans) system and equally distributes the present welding
fume to reduce the background concentration of welding fume
in the workshop.
2.2.2 ControlPro
ControlPro is an intelligent platform that controls the filter
system as well as the connected extraction fan. It contains an
extensive feature package to monitor and arrange the
RamAir™ pulse amplifier (filter cleaning system), the required
airflow and the corresponding fan speed. By means of the
user-friendly HMI you can program all desired parameters. The
HMI gives a clear insight into the system status and
performance at all times.
ControlPro allows for remote access via a network connection.
3
SAFETY INSTRUCTIONS
General
The manufacturer does not accept any liability for
damage to the product or personal injury caused by
ignoring of the safety instructions in this manual, or
by negligence during installation, use, maintenance, and repair
of the product mentioned on the cover of this document and
any corresponding accessories. Specific working conditions or
used accessories may require additional safety instructions.
Immediately contact your supplier if you detect a potential
danger when using the product.
The user of the product is always fully responsible for
observing the local safety instructions and regulations.
Obey all applicable safety instructions and regulations.
User manual
- Everyone working on or with the product, must be familiar
with the contents of this manual and must strictly obey the
instructions therein. The management should instruct the
personnel in accordance with the manual and obey all
instructions and directions given.
- Do not change the order of the steps to perform.
- Always keep the manual with the product.
Pictograms and instructions on the product (if
present)
- The pictograms, warning and instructions attached to the
product are part of the safety features. They must not be
covered or removed and must be present and legible during
the entire life of the product.
- Immediately replace or repair damaged or illegible
pictograms, warnings and instructions.
4.
Refer to Fig. VI on page 28 for the airflow through the air inlet module