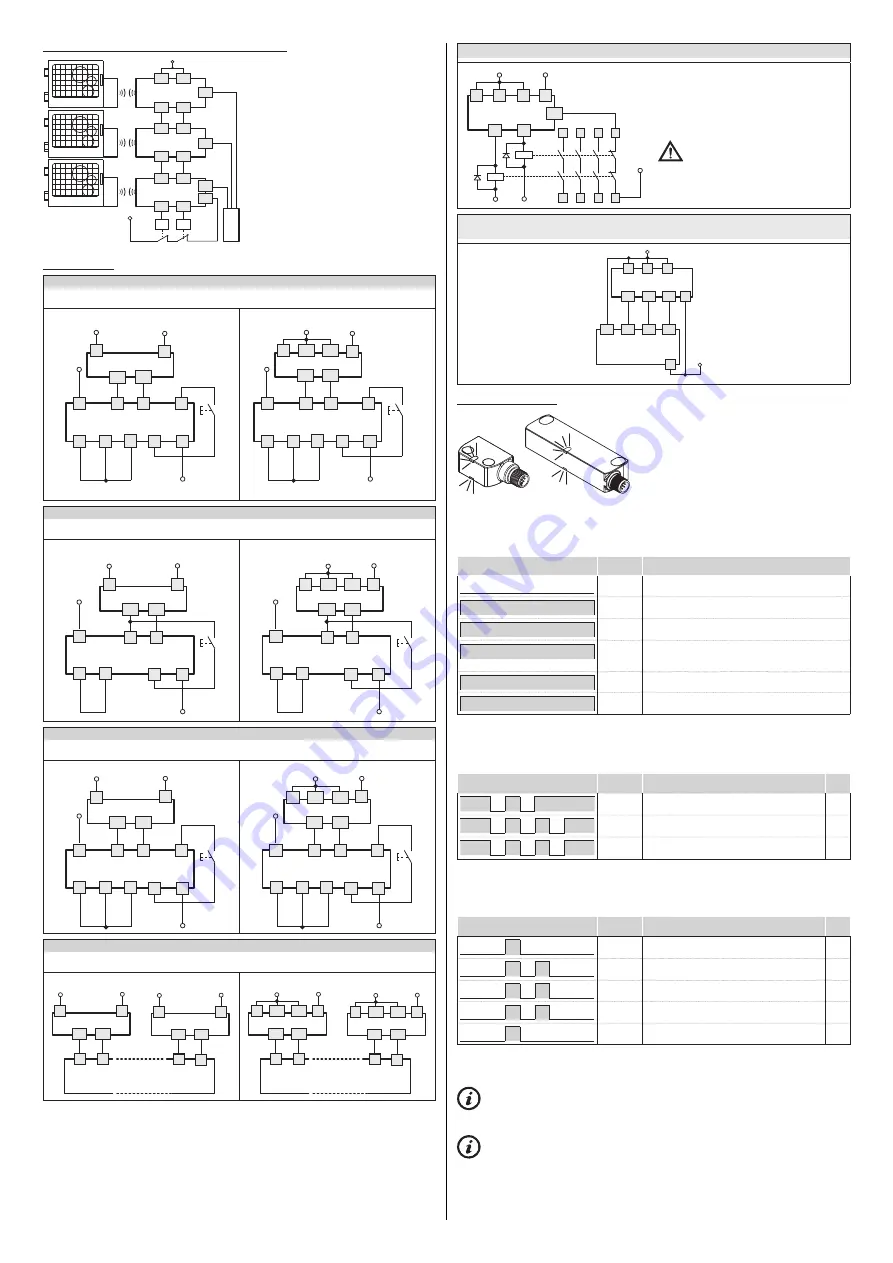
8/20
5.6 EDM connection (External Device Monitoring)
ST ••5•••• / ST ••9••••
ST ••3••••
ST ••3••••
PLC
IS1
K1
K2
O3
SM ••T
SM ••T
SM ••T
O3
O3
EDM
+
+
IS2
OS1
OS2
IS1
IS2
IS1
IS2
OS1
OS2
OS1
OS2
For certain specific applications, as an
alternative to connection to safety mod-
ules, it is possible to use the ST ••5••••
or ST ••9•••• articles with check of the
NC contacts of the forcibly guided re-
lays (K1, K2) connected to the EDM in-
put, installed as the last sensor in the
cascade.
5.7 Interfacing
Connections with CS AR-08•••• safety modules
Input configuration with monitored start
2 channels / Category 4 / up to SIL 3 / PL e
5-pole versions
8-pole versions
S33
S21
S22
S35
S34
A2
S52
S12
A1
-
+
OS2
A1
+
A2
-
ST
CS
OS1
S33
S21
S22
S35
S34
A2
S52
S12
A1
-
+
OS2
OS1
IS2
IS1
A1
+
A2
-
ST
CS
Connections with CS AR-05•••• / CS AR-06•••• safety modules
Input configuration with manual start (CS AR-05••••) or monitored start (CS AR-06••••)
2 channels / Category 4 / up to SIL 3 / PL e
5-pole versions
8-pole versions
S21
S22
S34
A2
A1
-
+
S52
S12
OS2
OS1
A1
+
A2
-
ST
CS
S21
S22
S34
A2
A1
-
+
S52
S12
OS2
OS1
IS2
IS1
A1
+
ST
CS
A2
-
Connections with CS AT-0••••• / CS AT-1••••• safety modules
Input configuration with monitored start
2 channels / Category 4 / up to SIL 3 / PL e
5-pole versions
8-pole versions
S33
S21
S22
S35
S34
A2
A1
-
+
S31
S12
OS2
OS1
A1
+
A2
-
ST
CS
S33
S21
S22
S35
S34
A2
A1
-
+
S31
S12
OS2
OS1
IS2
IS1
A1
+
A2
-
ST
CS
Connections with CS MF••••0, CS MP••••0 safety modules
The connections vary according to the program of the module
Category 4/ up to SIL 3 / PL e
5-pole versions
8-pole versions
Ixx
Ixx
OS2
OS1
A1
+
OS2
OS1
A1
+
Ixx
Ixx
A2
-
A2
-
ST
ST
CS
Ixx
Ixx
OS2
OS1
IS2
IS1
A1
+
OS2
OS1
IS2
IS1
A1
+
Ixx
Ixx
A2
-
A2
-
ST
ST
CS
Connections with external contactors (EDM versions only)
K1
K2
-
-
+
A1
IS1
OS1
OS2
IS2
A2
+
-
ST ••5•••• / ST ••9••••
EDM
Articles ST ••5•••• and ST ••9•••• must
be connected to contactors with forcibly
guided output contacts, as shown in the
adjacent diagram. When connected in
this way, the sensor can be classified
as a control circuit device up to PDF-M
(EN 60947-5-3)
Caution: if all OS safety outputs
are connected directly to a safety contac-
tor, we recommend using fast switching
diodes connected in parallel to the con-
tactor coils.
Connections with Pizzato Elettrica expansion modules (e.g. CS ME-03••••)
(only ST
••5••••,
ST
••9•••• versions)
OS2
+
-
ST
••5•••• / ST ••9••••
EDM
A2
A1
A2
IS2
IS1
OS1
OS2
OS1
EDM
EDM
5.8 Operating states
The sensor has a multicolour signalling LED,
which, through the use of illumination, flash-
ing, and colour sequences, indicates the
various device operating states to the user,
as well as any warnings or errors affecting
internal electronic components.
The LED can be seen on both sides of the
sensor, regardless of device installation di-
rection.
The predefined sensor operating states (OFF, RUN, ERROR, SET) are indicated by
a constantly lit LED.
LED illumination sequence
Sensor
state
Description
OFF
Sensor off.
GN
RUN
Normal operating state with safety outputs on. No
pending error or warning.
YE
RUN
Normal operating state with safety outputs off. No
pending error or warning.
TQ
RUN
Normal operating state with detected actuator and
safety outputs off. No pending error or warning.
NOTE: for versions with multitag programming only.
VT
SET
New actuator acquisition state.
RD
ERROR
Internal device error state.
Table 1: Predefined operating states
If an ERROR event is identified, the LED cycles between continuous light corresponding
to the ERROR state (see Table 1) with one of the illumination sequences listed in Table
2, each of which corresponds to a different message type.
LED illumination sequence
Sensor
state
Description
Prio-
rity
RD
RD
RD
ERROR
Temperature error: the sensor temperature is
outside permitted limits.
9
RD
RD
RD
RD
ERROR
Voltage error: the sensor supply voltage is
outside permitted limits.
8
RD
RD
YE
RD
ERROR
Short circuit between the safety outputs OS1
and OS2.
7
Table 2: ERROR messages
If a WARNING event is identified, the LED cycles between continuous light
corresponding to the current operating state (see Table 1) with the corresponding
illumination sequence listed in Table 3.
LED illumination sequence
Sensor
state
Description
Prio-
rity
RD
WARNING
Temperature warning: the sensor temperatu-
re is close to permitted limits.
6
RD
RD
WARNING
Voltage warning: the supply voltage is close
to permitted limits.
5
YE
YE
WARNING
No signal at the inputs IS1 and IS2.
4
YE
GN
WARNING
Inputs IS1 and IS2 inconsistent.
3
YE
WARNING
The actuator is in the detection limit area.
2
Table 3: WARNING messages
Legend:
GN = green
RD = red
YE = yellow
BU = blue
VT = purple
TQ = turquoise
WARNING events are generally reversible. ERROR events are not reversible:
the device does not recover from the error, but must be switched off, and the cause of
the error resolved prior to switching back on.
If multiple ERROR or WARNING events are present at the same time, the highest
priority error only is indicated. For example, where both a temperature warning and a
voltage warning are present, only the temperature signalling sequence is indicated;
the voltage warning sequence is indicated only once the temperature warning is no
longer active, i.e. the temperature exits the alert threshold.
Pizzato Elettrica
CS ME-03
••••
expansion module