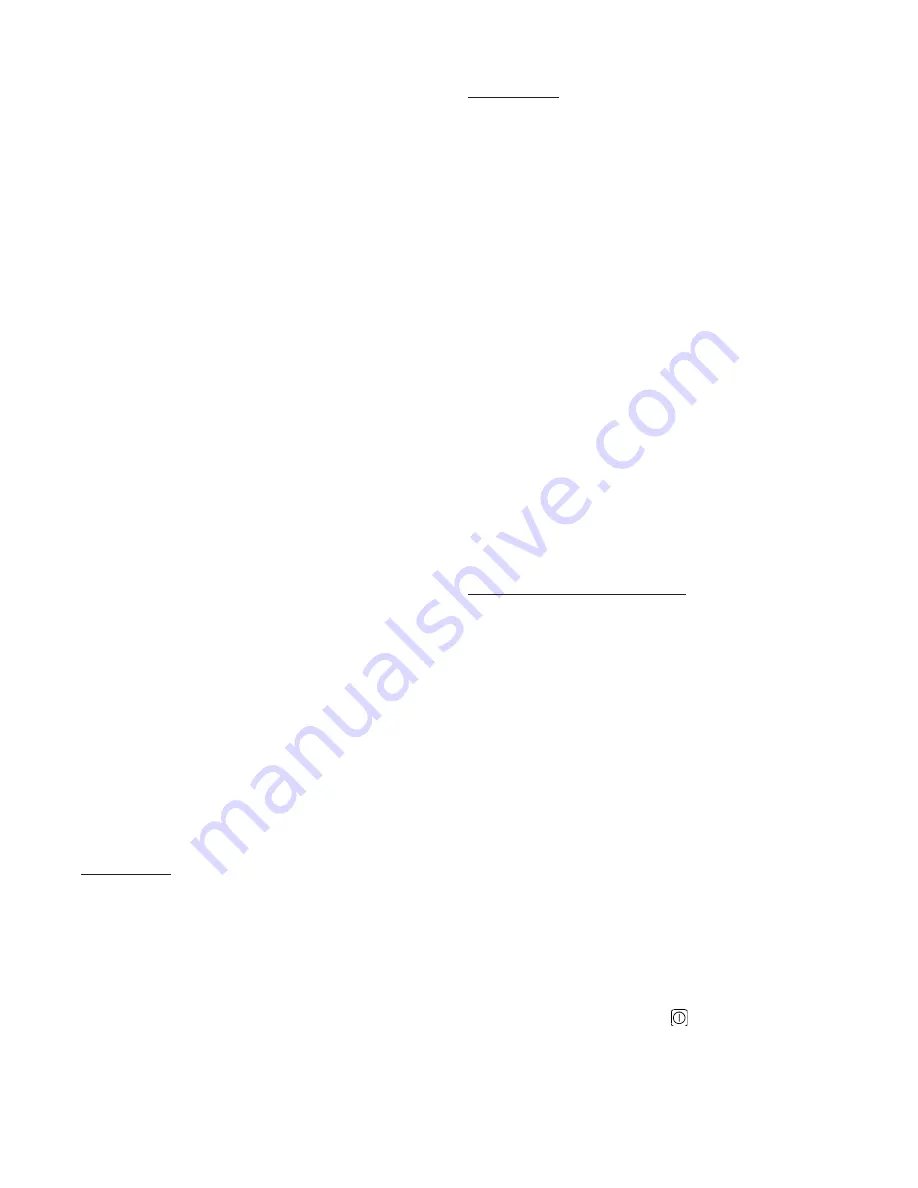
2
Clearances:
Minimum clearance of 6" (15cm) must be maintained
from combustible construction on each side and the
rear of the equipment. This equipment may be in-
stalled on combustible floors.
Maintain a minimum of 24"(61cm) clearance in front
of the fryer to provide for proper operation, mainte-
nance and servicing.
Wiring diagram(s) are located in the back of the ser-
vice manual and inside the fryers.
The control (interlock) voltage for this equipment
must be 120VAC (US & Canada). For other coun-
tries please check the rating plate.
Regular cleaning of this equipment, as well as the
hood, is an important part of proper maintenance.
Refer to Maintenance Requirement Cards for proper
procedure and frequency.
Once the fryers are in place:
Leveling the fryers will help ensure proper opera-
tion. To level the fryers loosen the two set screws on
the caster stem. Rotate the collar of the caster to raise
or lower the height of the unit. Tighten set screws to
lock the adjustment. Casters should be adjusted so
that the fryers are level and at the correct height un-
der the hood system.
Clean the fry tanks using the Boil Out procedure on
Maintenance Card 14A.
A wiring diagram is located in the back of this manual
and inside the fryers.
EQUIPMENT SET UP AND SHUT DOWN
PROCEDURES
NOTE:
Should you experience a power failure, your
fryers will shut off automatically. Once the power
has been restored, press the
key to turn the fryer
back ON. If the machine is being filtered, close the
RED return valve so that the filter does not run if the
machine is left unattended. Do not attempt to restart
the fryers until the power is restored.
INSTALLATION INSTRUCTIONS
CAUTION:
This equipment is manufactured for the use on a
particular voltage and phase which is specified on
the rating plate located on the inside of the door.
When your fryers arrive, look them over carefully
noting any damage on the freight bill. If concealed
damage is found after you have accepted the equip-
ment, report it to the carrier immediately as all claims
must be filled within 15 days of the receipt of the
shipment. Also, be sure to keep all packing materi-
als as these will be necessary to make any claim.
Follow these installation instructions carefully. A
proper installation is important for the operation of
the fryers.
All installations must conform to all local and state
codes and well as the United States National Elec-
trical Code (ANSI/N.F.P.A. No. 70-1987). In
Canada, installations must be made in accordance to
Canadian Electrical Code Part I, CSA-C22.1.
Do not block the area around the casters and under
the fryers. Contact the Autorized Pitco Frialator rep-
resentative for any service related problems. Rou-
tine maintenance may be performed by qualified
personnel.
The duct system, the hood system and the fryers must
be cleaned on a regular basis and must be kept clear
of any grease build up. See the appropriate Mainte-
nance Requirements Cards.
Ventilation:
A proper ventilation system is also an important part
of the installation. For information on the construc-
tion and installation of ventilating hoods, please see
“Standard for the Installation of Equipment for the
Removal of Smoke and Grease Laden Vapors from
Commercial Cooking Equipment”, N.F.P.A. No. 96-
1987. Copies can be obtained by writing to the Na-
tional Fire Protection Association, Battery March
Park, Quincy, MA 02269
Summary of Contents for ME14S-C/MFD
Page 16: ......
Page 17: ...PARTS SECTION...
Page 19: ......
Page 21: ......
Page 23: ......
Page 25: ......
Page 27: ......
Page 29: ......
Page 31: ......
Page 33: ......
Page 34: ...ME14 SCHEMATIC 700246H...
Page 35: ...ME14 DOMESTIC FULL SPLIT VAT CONTROL SCHEMATIC 700246H...
Page 36: ...ME14 DOMESTIC FULL SPLIT VAT HI POWER SCHEMATIC 700246H...
Page 37: ......