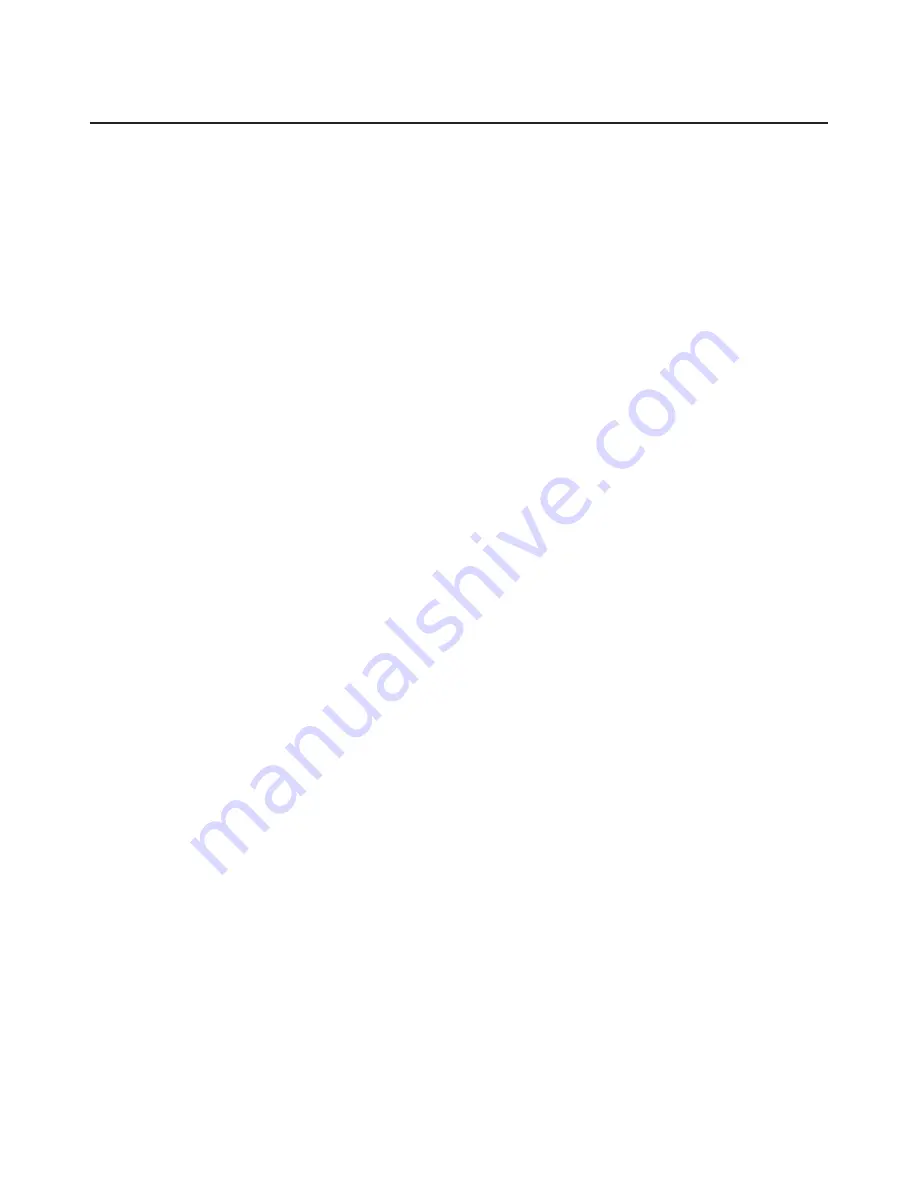
WHEELS AND BRAKES (Cont.)
5. Riveted type lining may be removed from backing plates by drilling out old rivets using a 5/32 drill.
Install a new set of linings using proper rivets and a rivet set that will properly stake the lining and
form a correct flair of the rivet. Snap-on type lining used on optional heavy duty assemblies may be
removed by prying loose with a screwdriver or a thin flat wedge. Install snap-on type by positioning
onto pins and applying pressure to snap into position.
– NOTE –
To inspect heavy duty brake lines (press-on metallic type)
check expansion groove. If groove is not showing replace lining.
– NOTE –
Replacement of brake linings (organic) on standard Cleveland
30-65 brakes should be conditioned by performing a minimum
of six light pedal effort braking applications from 25 to 40 mph
allowing discs to partially cool between stops.
Replacement brake linings (metallic) used on optional heavy
duty brakes (Cleveland 30-83) should be conditioned by performing
two (2) consecutive full stop braking applications from 30 to 35
kts. Do not allow brake discs to cool substantially between
stops. This will wear off any high spots and at same time
generate sufficient heat to glaze surface of metallic linings.
Once linings are glazed, they will provide many hours of
maintenance free service.
ASSEMBLY AND INSTALLATION OF WHEEL BRAKE ASSEMBLY
1. Lubricate piston O-ring(s) with fluid MIL-H-5606A and install on piston(s). Slide piston(s) in cylinder
housing until flush with surface of housing.
2. Slide lining pressure plate onto anchor bolts of housing.
3. Slide cylinder housing assembly on torque plate of gear.
4. Position lining back plate between wheel and brake disc. Install bolts and torque to 40 inch -pounds to
secure assembly.
5. Connect brake line to brake cylinder housing.
6. Bleed brake system as described in Bleeding Brakes.
BRAKE MASTER CYLINDER (HAND PARKING BRAKE)
REMOVAL OF BRAKE MASTER CYLINDER (HAND BRAKE)
1. To remove brake master cylinder, first disconnect inlet supply line from fitting at top of cylinder and
allow fluid to drain from reservoir and line into a suitable container.
2. Disconnect pressure line from fitting on cylinder and allow fluid to drain from cylinder line.
3. Disconnect end of cylinder rod from brake handle by removing cotter pin that safeties connecting
clevis pin. Remove clevis pin and spacer washers.
PIPER AIRCRAFT
PA-32R-301/301T
MAINTENANCE MANUAL
32-40-00
Page 32-60
Reissued: July 1, 1993
3D5
Summary of Contents for PA-32R-301T SARATOGA S
Page 26: ...CHAPTER 4 AIRWORTHINESS LIMITATIONS 1C1 ...
Page 29: ...CHAPTER 5 TIME LIMITS MAINTENANCE CHECKS 1C4 ...
Page 53: ...CHAPTER 6 DIMENSIONS AND AREAS 1D6 ...
Page 64: ...CHAPTER 7 LIFTING AND SHORING 1D21 ...
Page 68: ...CHAPTER 8 LEVELING AND WEIGHING 1E1 ...
Page 72: ...CHAPTER 9 TOWING AND TAXIING 1E5 ...
Page 76: ...CHAPTER 10 PARKING AND MOORING 1E9 ...
Page 80: ...CHAPTER 11 REQUIRED PLACARDS 1E13 ...
Page 92: ...CHAPTER 12 SERVICING 1F1 ...
Page 126: ...CHAPTER 20 STANDARD PRACTICES AIRFRAME 1G17 ...
Page 127: ...THIS PAGE INTENTIONALLY LEFT BLANK ...
Page 139: ...CHAPTER 21 ENVIRONMENTAL SYSTEMS 1H5 ...
Page 188: ...CHAPTER 22 AUTOFLIGHT 1J7 ...
Page 193: ...CHAPTER 23 COMMUNICATIONS 1J12 ...
Page 203: ...CHAPTER 24 ELECTRICAL POWER 1J22 ...
Page 263: ...CHAPTER 25 EQUIPMENT FURNISHINGS 2A13 ...
Page 269: ...CHAPTER 27 FLIGHT CONTROLS 2A20 ...
Page 332: ...CHAPTER 28 FUEL 2D11 ...
Page 363: ...CHAPTER 29 HYDRAULIC POWER 2E18 ...
Page 404: ...CHAPTER 30 ICE AND RAIN PROTECTION 2G16 ...
Page 470: ...CHAPTER 32 LANDING GEAR 3A13 ...
Page 550: ...CHAPTER 33 LIGHTS 3D24 ...
Page 562: ...CHAPTER 34 NAVIGATION AND PITOT STATIC 3E12 ...
Page 582: ...CHAPTER 35 OXYGEN 3F8 ...
Page 604: ...CHAPTER 37 VACUUM 3G6 ...
Page 616: ...CHAPTER 39 3G18 ELECTRIC ELECTRONIC PANELS MULTIPURPOSE PARTS ...
Page 620: ...CHAPTER 51 STRUCTURES 3G22 ...
Page 636: ...CHAPTER 52 DOORS 3H14 ...
Page 650: ...CHAPTER 55 STABILIZERS 3I4 ...
Page 662: ...CHAPTER 56 WINDOWS 3I16 ...
Page 670: ...CHAPTER 57 WINGS 3I24 ...
Page 688: ...CHAPTER 61 PROPELLER 3J18 ...
Page 704: ...CHAPTER 70 STANDARD PRACTICES ENGINES 3K10 ...
Page 708: ...CHAPTER 71 POWER PLANT 3K14 ...
Page 737: ...CHAPTER 73 ENGINE FUEL SYSTEM 4A13 ...
Page 749: ...CHAPTER 74 IGNITION 4B1 ...
Page 783: ...CHAPTER 77 ENGINE INDICATING 4C11 ...
Page 793: ...CHAPTER 78 EXHAUST 4C21 ...
Page 801: ...CHAPTER 79 OIL 4D5 ...
Page 805: ...CHAPTER 80 STARTING 4D9 ...
Page 819: ...CHAPTER 81 TURBINES 4D23 ...
Page 833: ...CHAPTER 91 CHARTS WIRING DIAGRAMS 4E13 ...