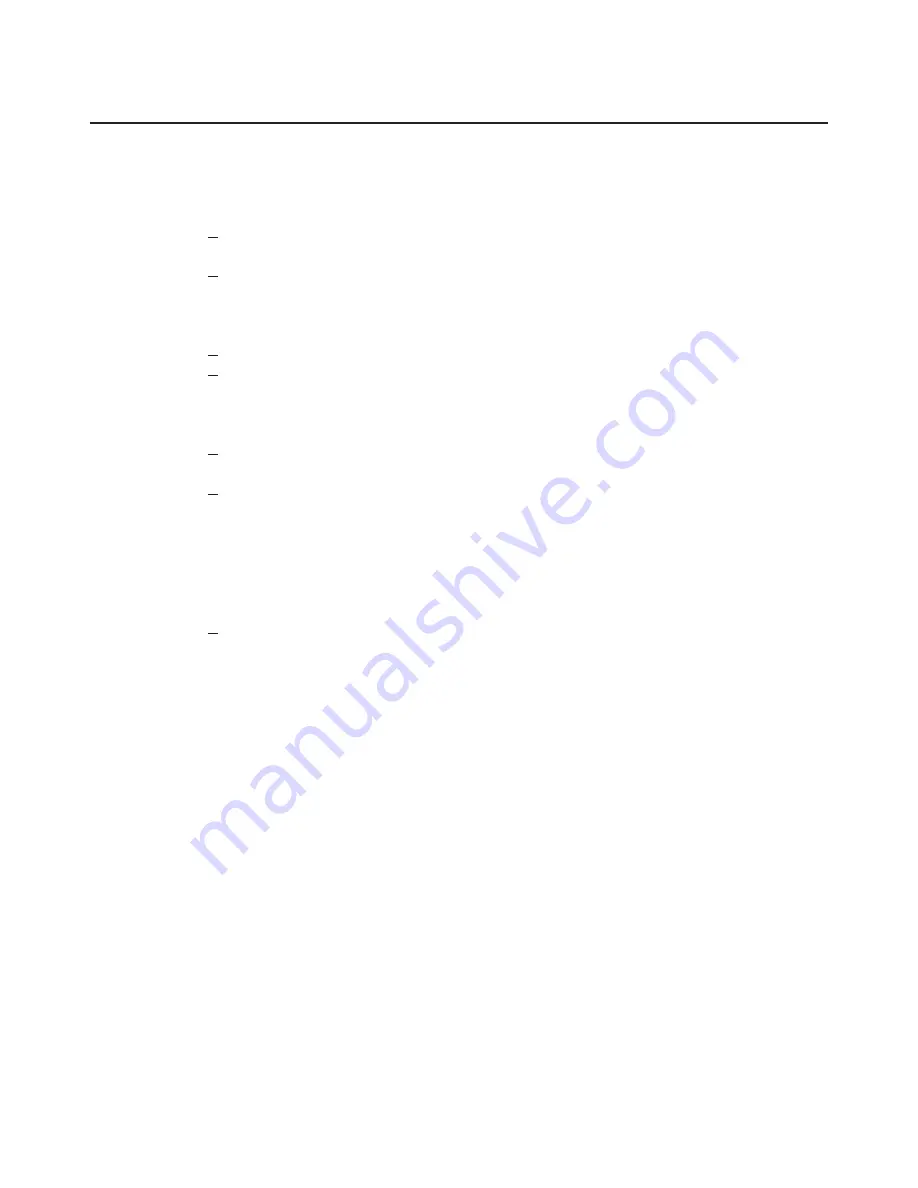
AIRFOILS (Cont.)
I-Pneumatic Boots (cont.)
(2) Boot Repair (cont.)
2 Buff area around damage with buffing stick, Part No. 74-451-75, so that surface is
thoroughly roughened.
3 Apply patch to deicer with stretch in widthwise direction of inflatable tubes, sticking
edge of patch in place, working remainder down with slight pulling action so injury is
closed. Do not trap air between patch and deicer surface.
(c) Loose Surface Ply in Dead Area (Non-Inflatable Area)
1 Peel and trim loose surface ply to where adhesion of surface ply to deicer is good.
2 Scrub (roughen) area in which surface ply is removed with steel wool. Scrubbing motion
must be parallel to cut edge of surface ply to prevent loosening it. Scrub with steel wool
and Toluol directly over all edges, but parallel to edges or surface ply to taper them down
to tan rubber ply.
3 Cut a piece of surface ply material, Part No. 74-451-23, to cover damaged area and
extend at least one inch beyond in all directions.
4 Mask off damaged boot area 1-1/2 inch larger in length and width than size of surface
ply patch. Apply one coat of cement, Part No. 74-451-20, to damaged area and one coat
of patch. Allow cement to set until tacky. Roll surface ply to deicer with 2 inch rubber
roller, Part No. 74-451-74. Roll edges with stitcher-roller, Part No. 74-451-73. Apply just
enough tension on surface ply when rolling to prevent wrinkling and be careful to pre-
vent trapping air. If air blisters appear after surface ply is applied, remove them with a
hypodermic needle.
5 Clean excess cement from deicer with solvent.
(d) Loose Surface Ply in Tube Area . Loose surface ply in tube area is usually an indication of
deicer starting to flex fail. This type of failure is more easily detected in form of a blister
under surface ply when deicer is pressurized. If this type of damage (or void) is detected
while still a small blister (about 1/4 or 3/8 inch diameter) and patched immediately, service
life of deicer will be appreciably extended. Apply repair patch as outlined in Paragraph I, (2),
(e) Damage to Fabric Back Ply of Deicer During Removal
If cement has pulled loose from wing skin and adhered to back surface of deicer, remove it
with steel wool and MEK. In those spots where coating has pulled off fabric, leaving bare
fabric exposed, apply at least two addi- tional coats of cement, 1300L. Allow each coat to
dry thoroughly.
(3) Vulcanized Repairs
Due to variety of boot damage possible, it is recommended that B. F. Goodrich Company be
contacted so they can determine extent of damage and whether it is repairable by vulcanized
method or not. Overall condition of deicer boot must be given careful consideration before
deciding on any repairs. Damages can vary from minor punctures which may be easily repaired,
to extensive ripping of tube or stretch areas which may make repairs exceedingly difficult or
impossible. Determination where this division between repairable and unrepairable damage exists
will depend upon careful judgment of the inspector. For this reason, Piper recommends contacting
B. F. Goodrich Company at Akron, Ohio.
PIPER AIRCRAFT
PA-32R-301/301T
MAINTENANCE MANUAL
30-10-00
Page 30-13
Reissued: July 1, 1993
2H7
Summary of Contents for PA-32R-301T SARATOGA S
Page 26: ...CHAPTER 4 AIRWORTHINESS LIMITATIONS 1C1 ...
Page 29: ...CHAPTER 5 TIME LIMITS MAINTENANCE CHECKS 1C4 ...
Page 53: ...CHAPTER 6 DIMENSIONS AND AREAS 1D6 ...
Page 64: ...CHAPTER 7 LIFTING AND SHORING 1D21 ...
Page 68: ...CHAPTER 8 LEVELING AND WEIGHING 1E1 ...
Page 72: ...CHAPTER 9 TOWING AND TAXIING 1E5 ...
Page 76: ...CHAPTER 10 PARKING AND MOORING 1E9 ...
Page 80: ...CHAPTER 11 REQUIRED PLACARDS 1E13 ...
Page 92: ...CHAPTER 12 SERVICING 1F1 ...
Page 126: ...CHAPTER 20 STANDARD PRACTICES AIRFRAME 1G17 ...
Page 127: ...THIS PAGE INTENTIONALLY LEFT BLANK ...
Page 139: ...CHAPTER 21 ENVIRONMENTAL SYSTEMS 1H5 ...
Page 188: ...CHAPTER 22 AUTOFLIGHT 1J7 ...
Page 193: ...CHAPTER 23 COMMUNICATIONS 1J12 ...
Page 203: ...CHAPTER 24 ELECTRICAL POWER 1J22 ...
Page 263: ...CHAPTER 25 EQUIPMENT FURNISHINGS 2A13 ...
Page 269: ...CHAPTER 27 FLIGHT CONTROLS 2A20 ...
Page 332: ...CHAPTER 28 FUEL 2D11 ...
Page 363: ...CHAPTER 29 HYDRAULIC POWER 2E18 ...
Page 404: ...CHAPTER 30 ICE AND RAIN PROTECTION 2G16 ...
Page 470: ...CHAPTER 32 LANDING GEAR 3A13 ...
Page 550: ...CHAPTER 33 LIGHTS 3D24 ...
Page 562: ...CHAPTER 34 NAVIGATION AND PITOT STATIC 3E12 ...
Page 582: ...CHAPTER 35 OXYGEN 3F8 ...
Page 604: ...CHAPTER 37 VACUUM 3G6 ...
Page 616: ...CHAPTER 39 3G18 ELECTRIC ELECTRONIC PANELS MULTIPURPOSE PARTS ...
Page 620: ...CHAPTER 51 STRUCTURES 3G22 ...
Page 636: ...CHAPTER 52 DOORS 3H14 ...
Page 650: ...CHAPTER 55 STABILIZERS 3I4 ...
Page 662: ...CHAPTER 56 WINDOWS 3I16 ...
Page 670: ...CHAPTER 57 WINGS 3I24 ...
Page 688: ...CHAPTER 61 PROPELLER 3J18 ...
Page 704: ...CHAPTER 70 STANDARD PRACTICES ENGINES 3K10 ...
Page 708: ...CHAPTER 71 POWER PLANT 3K14 ...
Page 737: ...CHAPTER 73 ENGINE FUEL SYSTEM 4A13 ...
Page 749: ...CHAPTER 74 IGNITION 4B1 ...
Page 783: ...CHAPTER 77 ENGINE INDICATING 4C11 ...
Page 793: ...CHAPTER 78 EXHAUST 4C21 ...
Page 801: ...CHAPTER 79 OIL 4D5 ...
Page 805: ...CHAPTER 80 STARTING 4D9 ...
Page 819: ...CHAPTER 81 TURBINES 4D23 ...
Page 833: ...CHAPTER 91 CHARTS WIRING DIAGRAMS 4E13 ...