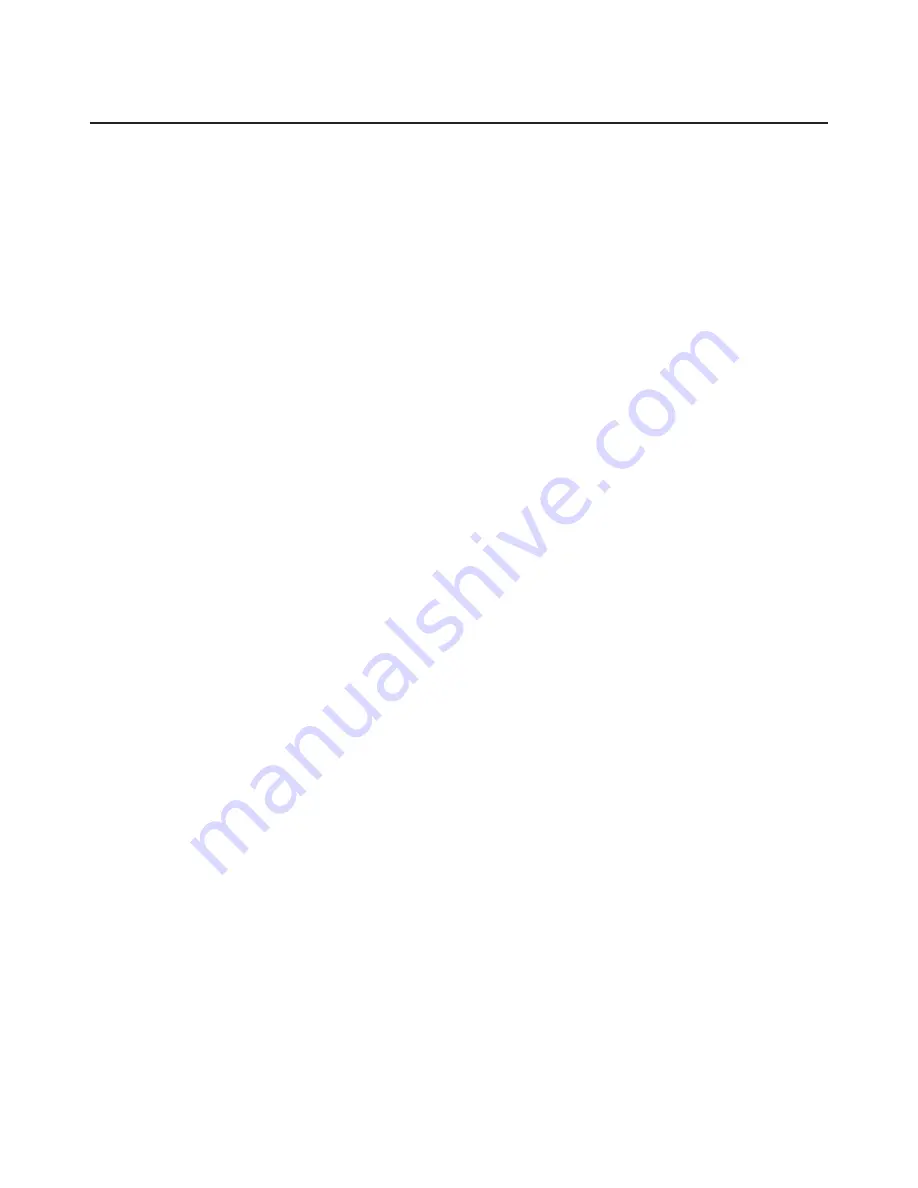
HYDRAULIC POWER (Cont.)
B. Description (cont.)
A pressure switch is installed on a cross fitting connected to the pump mount assembly. During landing
gear retraction the pressure switch is the primary means to shut down the pump. This switch opens
the electrical circuit to the pump solenoid when the gear fully retracts and the pressure in the system
increases to 1800 ± 100 psi. As long as the gear selector handle is in the up position the switch will
continue to hold the circuit open until system pressure drops to 200 to 400 psi. At that time, the pump
will again operate to build up pressure to prevent the gear from free falling. The pressure switch has no
effect on the system when the gear selector is in the down position.
Both the Prestolite and Oildyne hydraulic pumps are gear type units driven by a 14-volt reversible
motor. designed to operate in a pressure range of 2000 to 2500 psi. To prevent excessive buildup of
pressure in the hydraulic system due to expansion, a thermal relief valve is incorporated in both the
Prestolite and Oildyne pumps. The Prestolite pump’s relief valve will open at 2250 ± 250 psi allowing
fluid to flow into the reservoir. The Oildyne pump’s relief valve will open at 3000 ± 500 psi Other
valves in both pumps channel fluid to the proper outlet during retraction or extension of gear. A shuttle
valve located in the base of the both pumps allows fluid displaced by the cylinder pistons to return to
the reservoir without back-pressure. (Refer to Figure 1 and Chart 1 for specific pressures.)
Also in the system is a by-pass or free-fall valve that allows the gear to drop should a malfunction in
the pump system occur. To prevent the gear from extending too fast, there is a special restrictor nipple
on the main gear retraction line. This valve is manually controlled by a lever or push-pull type cable
located between the two pilot seats on the elevator trim quadrant.'
– NOTE–
Beginning with airplane s/n’s 3213003 and up, Piper Aircraft
no longer installs the automatic gear extender system. Piper
kit, P/N 765 199, provides information concerning the removal
of the backup landing gear extension system
Models that have not had the automatic backup gear extender removed, have a lever that can manually
extend the gear, or allow the gear to extend automatically by the use of a backup extension device that
operates by a pressure sensing mechanism that lowers the landing gear regardless of the gear selector
handle position. Its operation depends on airspeed and engine power (propeller slipstream). Gear
extension occurs even if the selector is in the up position, at airspeeds below approximately 103 KIAS
with engine power off. The device also prevents the gear from retracting at airspeeds below approxi-
mately 81 KIAS at sea level with full power, though the selector switch may be in the up position. This
speed increases with reduced power and/or increased altitude. The sensing device operation is con-
trolled by a differential air pressure across a flexible diaphragm which is mechanically linked to the
hydraulic valve and an electrical switch which actuates the pump motor. A high pressure and static air
source for actuating the diaphragm is provided in a mast mounted on the left side of the fuselage above
the wing. Manual override of the device is provided by an emergency gear lever located between the
front seats to the right of the flap handle.
PIPER AIRCRAFT
PA-32R-301/301T
MAINTENANCE MANUAL
29-00-00
Page 29-4
Reissued: July 1, 1993
2E24
Summary of Contents for PA-32R-301T SARATOGA S
Page 26: ...CHAPTER 4 AIRWORTHINESS LIMITATIONS 1C1 ...
Page 29: ...CHAPTER 5 TIME LIMITS MAINTENANCE CHECKS 1C4 ...
Page 53: ...CHAPTER 6 DIMENSIONS AND AREAS 1D6 ...
Page 64: ...CHAPTER 7 LIFTING AND SHORING 1D21 ...
Page 68: ...CHAPTER 8 LEVELING AND WEIGHING 1E1 ...
Page 72: ...CHAPTER 9 TOWING AND TAXIING 1E5 ...
Page 76: ...CHAPTER 10 PARKING AND MOORING 1E9 ...
Page 80: ...CHAPTER 11 REQUIRED PLACARDS 1E13 ...
Page 92: ...CHAPTER 12 SERVICING 1F1 ...
Page 126: ...CHAPTER 20 STANDARD PRACTICES AIRFRAME 1G17 ...
Page 127: ...THIS PAGE INTENTIONALLY LEFT BLANK ...
Page 139: ...CHAPTER 21 ENVIRONMENTAL SYSTEMS 1H5 ...
Page 188: ...CHAPTER 22 AUTOFLIGHT 1J7 ...
Page 193: ...CHAPTER 23 COMMUNICATIONS 1J12 ...
Page 203: ...CHAPTER 24 ELECTRICAL POWER 1J22 ...
Page 263: ...CHAPTER 25 EQUIPMENT FURNISHINGS 2A13 ...
Page 269: ...CHAPTER 27 FLIGHT CONTROLS 2A20 ...
Page 332: ...CHAPTER 28 FUEL 2D11 ...
Page 363: ...CHAPTER 29 HYDRAULIC POWER 2E18 ...
Page 404: ...CHAPTER 30 ICE AND RAIN PROTECTION 2G16 ...
Page 470: ...CHAPTER 32 LANDING GEAR 3A13 ...
Page 550: ...CHAPTER 33 LIGHTS 3D24 ...
Page 562: ...CHAPTER 34 NAVIGATION AND PITOT STATIC 3E12 ...
Page 582: ...CHAPTER 35 OXYGEN 3F8 ...
Page 604: ...CHAPTER 37 VACUUM 3G6 ...
Page 616: ...CHAPTER 39 3G18 ELECTRIC ELECTRONIC PANELS MULTIPURPOSE PARTS ...
Page 620: ...CHAPTER 51 STRUCTURES 3G22 ...
Page 636: ...CHAPTER 52 DOORS 3H14 ...
Page 650: ...CHAPTER 55 STABILIZERS 3I4 ...
Page 662: ...CHAPTER 56 WINDOWS 3I16 ...
Page 670: ...CHAPTER 57 WINGS 3I24 ...
Page 688: ...CHAPTER 61 PROPELLER 3J18 ...
Page 704: ...CHAPTER 70 STANDARD PRACTICES ENGINES 3K10 ...
Page 708: ...CHAPTER 71 POWER PLANT 3K14 ...
Page 737: ...CHAPTER 73 ENGINE FUEL SYSTEM 4A13 ...
Page 749: ...CHAPTER 74 IGNITION 4B1 ...
Page 783: ...CHAPTER 77 ENGINE INDICATING 4C11 ...
Page 793: ...CHAPTER 78 EXHAUST 4C21 ...
Page 801: ...CHAPTER 79 OIL 4D5 ...
Page 805: ...CHAPTER 80 STARTING 4D9 ...
Page 819: ...CHAPTER 81 TURBINES 4D23 ...
Page 833: ...CHAPTER 91 CHARTS WIRING DIAGRAMS 4E13 ...