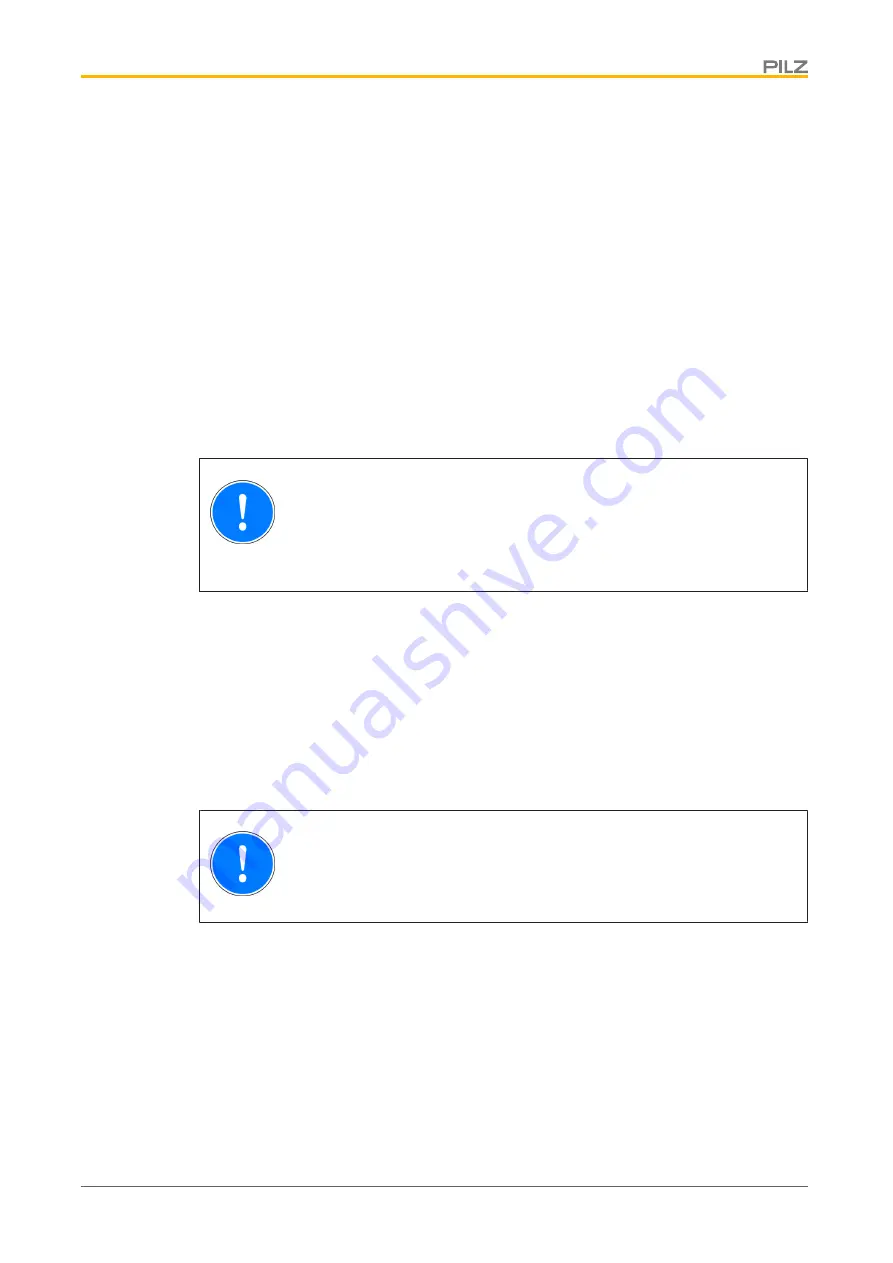
PNOZ po3.1p
Operating Manual PNOZ po3.1p
20676-EN-07
8
Function Description
The safety contacts are controlled by the base unit. The base unit controls the status of the
input circuits and the feedback loop. The supply voltage is fed via the PNOZpower bus.
When supply voltage is applied the "POWER" LED will light. The unit is ready for operation
when the feedback loop and the start circuit are closed at the base unit.
}
Functional procedure after closing the input circuit of the base unit:
– Close the safety contacts 13-14, 23-24, 33-34, 43-44, 53-54, 63-64, 73-74 and
83-84.
– The LEDs "CH. 1" and "CH. 2" are lit.
}
Functional procedure after opening the input circuit of the base unit:
– Safety contacts 13-14, 23-24, 33-34, 43-44, 53-54, 63-64, 73-74 and 83-84 are
opened redundantly.
– The LEDs "CH. 1" and "CH. 2" go out.
NOTICE
When controlling an expansion module via the den PNOZpower bus the
switch-on delay/delay-on de-energisation of the controlling device (e.g base
unit, control module, ...) and the expansion module are added together.
Installation
}
The unit should be installed in a control cabinet with a protection type of at least IP54.
}
Use the notches on the rear of the unit to attach it to a DIN rail.
}
Fit the unit to a horizontal DIN rail. If other mounting positions are used, the switching
capability values stated in the technical details cannot be maintained.
}
There are 2 sockets on the rear of the PNOZ po3.1p.
The base unit/control module and the expansion modules are connected using the
jumpers supplied.
NOTICE
Always connect a terminator to the first and last device.
}
Only use terminators, jumpers and terminals of the modular safety system PNOZpower.
}
Layout:
– The base module and the expansion modules can be installed in any position on
the PNOZpower modular safety system.
}
Maximum hardware:
– 1 base unit/control module
– 4 expansion modules
– 1 power supply unit