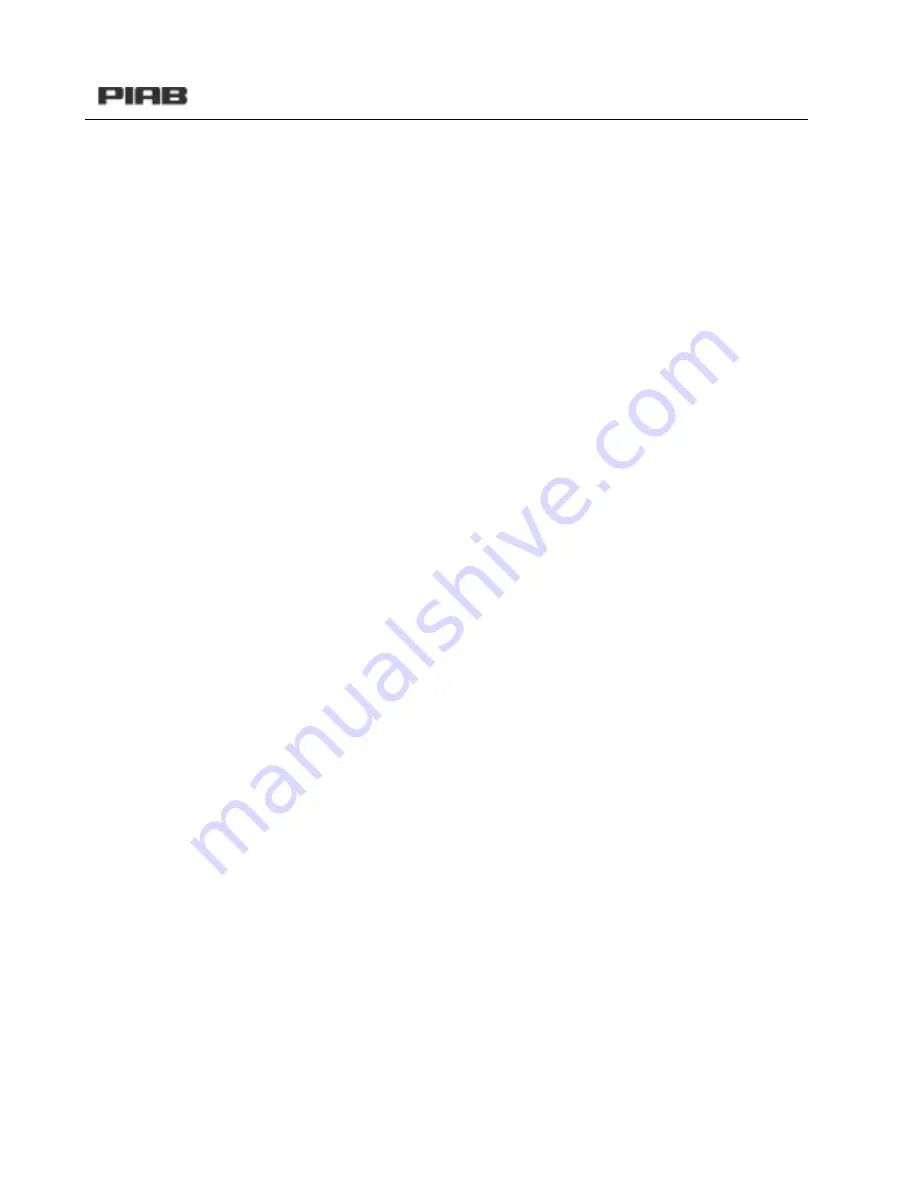
VACUUM CONVEYORS
23
CLEANING AND MAINTAINING THE VACUUM PUMP
PIAB vacuum pumps are easy to clean and maintain. The only wear parts in the pumps are flap valves
and gaskets. A slow, gradual loss in vacuum could be attributed to cracked gaskets or flap valves.
Please refer to pages 26 for a spare parts breakdown. The spare kits include all of the necessary flap
valves, gaskets, and a compressed air filter.
A slow gradual loss in vacuum could also be attributed to product moving through the pump. If any
material has come out of the exhaust, chances are the pump needs to be cleaned out.
Classic and L 100 vacuum pumps
The pump should be opened up and examined. Please refer to page 31 for a diagram and parts break-
down of the Classic 100. First the panel plate should be removed, and then the side plate. The valve
plate and side plate gasket is now visible. Located underneath the valve plate are the flap valves. Are
the gaskets or flap valves cracked? If so, the repair kit 32.01.069 should be purchased. The vacuum
chambers and nozzles should now be visible. Is the material that is being conveyed in the chambers or
nozzles? For optimum performance, there should not be any material in the pump. The pump's perfor-
mance decreases as more material gets lodged in the nozzles. Please be careful when cleaning the
pump. If a nozzle is broken off or rotated, the pump will need to be replaced. To remove material from
the nozzles or chambers, PIAB suggests soaking the pump in water or in water with mild detergent such
as dishwashing detergent. Once the pump has new seals and flap valves and it is clean and put back
together, it should run just like a brand new pump.
L100, L200, L400, L600, L800, L1200, L1600 vacuum pumps
The pump should be opened up and examined. Please refer to page 26-30 for a diagram and parts
breakdown of the vacuum pump. First the left side plate and gasket should be removed. This should ex-
pose the vacuum chambers and nozzles. If the vacuum port is facing down, then the flap valves are lo-
cated at the top of each vacuum chamber. Are the gaskets or flap valves cracked? If so, the appropriate
repair kit should be purchased. Is the material that is being conveyed in the chambers or nozzles? For
optimum performance, there should not be any material in the pump. The pump's performance decreas-
es as more material gets lodged in the nozzles. Please be careful when cleaning the pump. If a nozzle
is broken off or rotated, the pump will need to be replaced. To remove material from the nozzles or
chambers, PIAB suggests soaking the pump in water or in water with mild detergent such as dishwashing
detergent. Once the pump has new seals and flap valves and it is clean and put back together, it should
run just like a brand new pump.
Summary of Contents for C 1200 Series
Page 1: ...VACUUM CONVEYING C Series Conveyor Troubleshooting Guide www piab com ...
Page 7: ...VACUUM CONVEYORS 7 CONNECTION EXAMPLES CONTROL UNIT CU 1A B ART NO 01 04 550 ART NO 01 04 552 ...
Page 8: ...VACUUM CONVEYORS 8 CONTROL UNIT CU 1A B WITH FLUIDISATION ART NO 01 04 550 ART NO 01 04 552 ...
Page 10: ...VACUUM CONVEYORS 10 CONTROL UNIT CU 1A B USDA ART NO 01 04 550 ART NO 01 04 552 ...
Page 11: ...VACUUM CONVEYORS 11 CONTROL UNIT CU 2A B ART NO 01 04 540 ART NO 01 04 548 ...
Page 13: ...VACUUM CONVEYORS 13 CONTROL UNIT CU 2A B WITH FLUIDISATION ART NO 01 04 540 ART NO 01 04 548 ...
Page 14: ...VACUUM CONVEYORS 14 CONNECTION EXAMPLES ...
Page 15: ...VACUUM CONVEYORS 15 VALVE UNIT VCC EP VALVE UNIT VCC EP WITH FLUIDISATION ...
Page 18: ...VACUUM CONVEYORS 18 FILTER REPALCEMENT 1 2 3 4 5 ...
Page 19: ...VACUUM CONVEYORS 19 6 7 8 9 10 11 12 ...
Page 29: ...VACUUM CONVEYORS 29 INSIDE COMPONENTS OF MLL PUMPS ...
Page 31: ...VACUUM CONVEYORS 31 L100 CLASSIC COMPONENTS ...
Page 38: ...VACUUM CONVEYORS 38 CONTROL UNIT CU 1B BOTTOM VALVE NC ART NO 01 04 552 ...
Page 39: ...VACUUM CONVEYORS 39 PNEUMATIC DIAGRAM CONTROL UNIT CU 1A BOTTOM VALVE NO ART NO 01 04 550 ...
Page 40: ...VACUUM CONVEYORS 40 CONTROL UNIT CU 1B BOTTOM VALVE NC ART NO 01 04 552 ...
Page 41: ...VACUUM CONVEYORS 41 CONTROL UNIT CU 2B BOTTOM VALVE NC ART NO 01 04 548 ...
Page 44: ...VACUUM CONVEYORS 44 PNEUMATIC DIAGRAM COMPONENT LAYOUT ...
Page 45: ...VACUUM CONVEYORS 45 TIME SIGNAL DIAGRAM MOUNTING ...
Page 50: ...VACUUM CONVEYORS 50 VALVE CONNECTIONS FOR THE VCC EP ...
Page 53: ...VACUUM CONVEYORS 53 PNEUMATIC INJECTION VALVE ...
Page 57: ...VACUUM CONVEYORS 57 NOTES ...
Page 58: ...VACUUM CONVEYORS 58 NOTES ...
Page 59: ...VACUUM CONVEYORS 59 NOTES ...