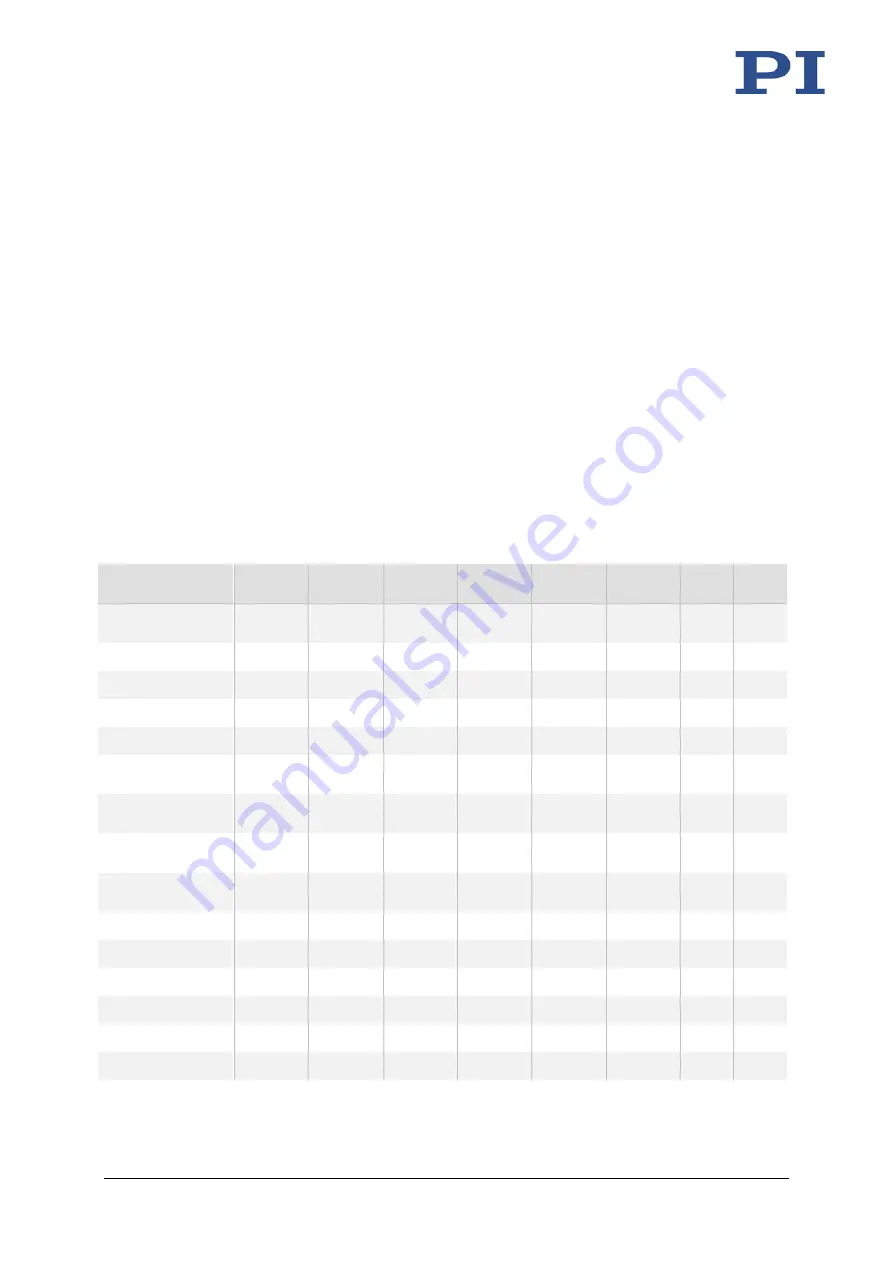
10 Technical Data
H-845 Hexapod System
MS222E
Version: 2.1.1
59
In this Chapter
Specifications .............................................................................................................. 59
Ambient Conditions and Classifications ...................................................................... 63
Dimensions of the hexapod ......................................................................................... 64
Pin Assignment for the hexapod ................................................................................. 66
10.1 Specifications
10.1.1 Data Table Hexapod
Motion and
positioning
H-845.D11
H-845.D31
H-845.D51
H-845.D21
H-845.D41
H-845.D61
Unit
Tole-
rance
Active axes
X, Y, Z,
θ
X
, θ
Y
, θ
Z
X, Y, Z,
θX, θY, θZ
X, Y, Z,
θX, θY, θZ
X, Y, Z,
θX, θY, θZ
X, Y, Z,
θX, θY, θZ
X, Y, Z,
θ
X
, θ
Y
, θ
Z
Travel range* X, Y
±110
±110
±110
±170
±170
±170
mm
Travel range* Z
±50
±50
±50
±105
±105
±105
mm
Travel range* θ
X
, θ
Y
±15
±15
±15
±20
±20
±20
°
Travel range* θ
Z
±30
±30
±30
±30
±30
±30
°
Actuator design
resolution
0.04
0.08
0.1
0.04
0.08
0.1
µm
Min. incremental
motion X, Y
1
2
2.5
1
2
2.5
µm
typ.
Min. incremental
motion Z
0.5
1
1
0.5
1
1
µm
typ.
Minimum incremental
motion
θ
X
,
θ
Y
,
θ
Z
15
30
30
15
30
30
µrad
typ.
Backlash X, Y
5
10
10
5
10
10
µm
typ.
Backlash Z
1
2
2
1
2
2
µm
typ.
Backlash θ
X
, θ
Y
15
30
30
15
30
30
µrad
typ.
Backlash θ
Z
30
60
60
30
60
60
µrad
typ.
Repeatability X, Y
±2
±4
±5
±2
±4
±5
µm
typ.
Repeatability Z
±0.5
±1
±2
±0.5
±1
±2
µm
typ.
10 Technical Data