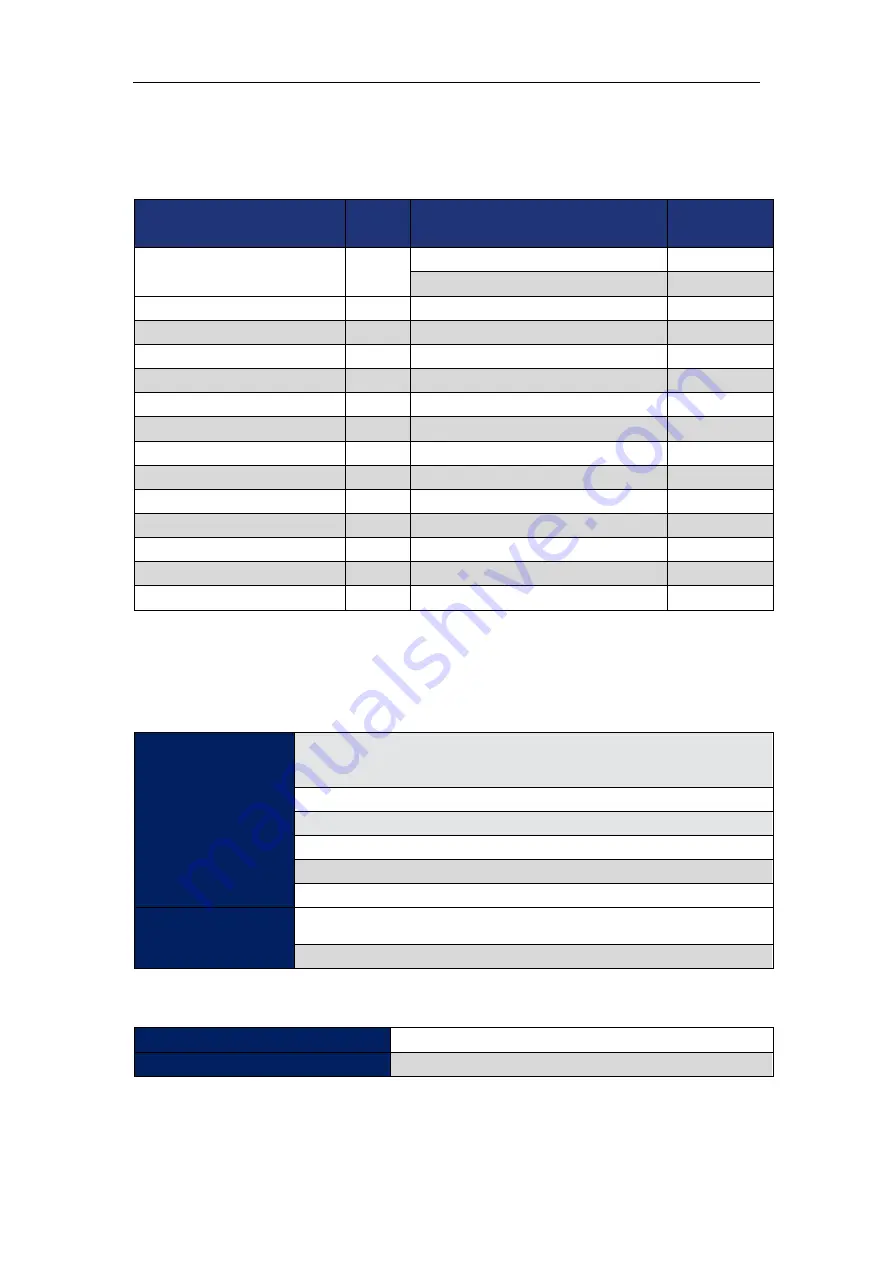
AxN Configurable Motion Control Platform
12
2.1
Specifications
Specifications
Technical specifications
Symbol
AxN 09.20.4
Units
Power Supply Voltage
𝑽
𝑖𝑛
150 ~ 500
Vac 3 phase
0 ~ 800
Vdc
Auxiliary supply voltage
𝑽
𝑎𝑢𝑥
24V ± 15% / 2A
Vdc
Output frequency
𝒇
0 ~ 1200
Hz
Current output, S1
(1)
𝑰
𝑜
9
Arms
Peak current
(1)
𝑰
𝑝
20
Arms
Power Losses total
(2)
𝑷
𝑙
200
W
Maximum output voltage
𝑽
𝑜𝑢𝑡
𝑽
𝑖𝑛
× 0.95
Vac
PWM frequency
(3)
𝒇
𝑝𝑤𝑚
4 / 8 / 16
kHz
Efficiency at nominal power
(1)
--
97.9
%
Input form factor (Full load)
--
0.9
Vac 3 phase
Maximum braking current
--
100% of
𝑰
𝑝
(peak current)
--
Cooling
--
1 fan 40
×
40
× 20
--
Flow rate
--
25.2
m
3
/hour
Dimensions (H
×
W
×
D)
--
201.8
×
96
×
164.6
mm
(1)
𝑽
𝑖𝑛
= 380 Vac,
𝑽
𝑜𝑢𝑡
= 𝑽
𝑖𝑛
× 0.95, 𝐓
𝑎𝑚𝑏
= 40
℃
, Comm.Freq.8kHz
(2) Including input rectifier losses
(3) PWM frequency will automatically decrease at Zero Speed, in order to keep Nominal Current Output
Motor Feedback Options
Main Encoder
(500kHz)
Sincos encoder 5 channels (2 absolute analog tracks/2 incremental
analog tracks/index)
Incremental encoder (1 Vpp or Different Line Driver)
Sensorless algorithm (w/o feedback)
Endat serial encoder 1.0 to 2.2 (default)
Resolver
Hiperface encoder
Secondary Encoder
(500kHz)
Incremental digital encoder without commutation tracks (500kHz)
Endat serial encoder
Programmable Input Signals
2 Differential analog inputs
± 10V (1mV) / R
in
= 10kΩ
8 digital inputs
20 ~ 30V / R
in
= 6.6kΩ to GND
Programmable Output Signals
Summary of Contents for AxN
Page 1: ......