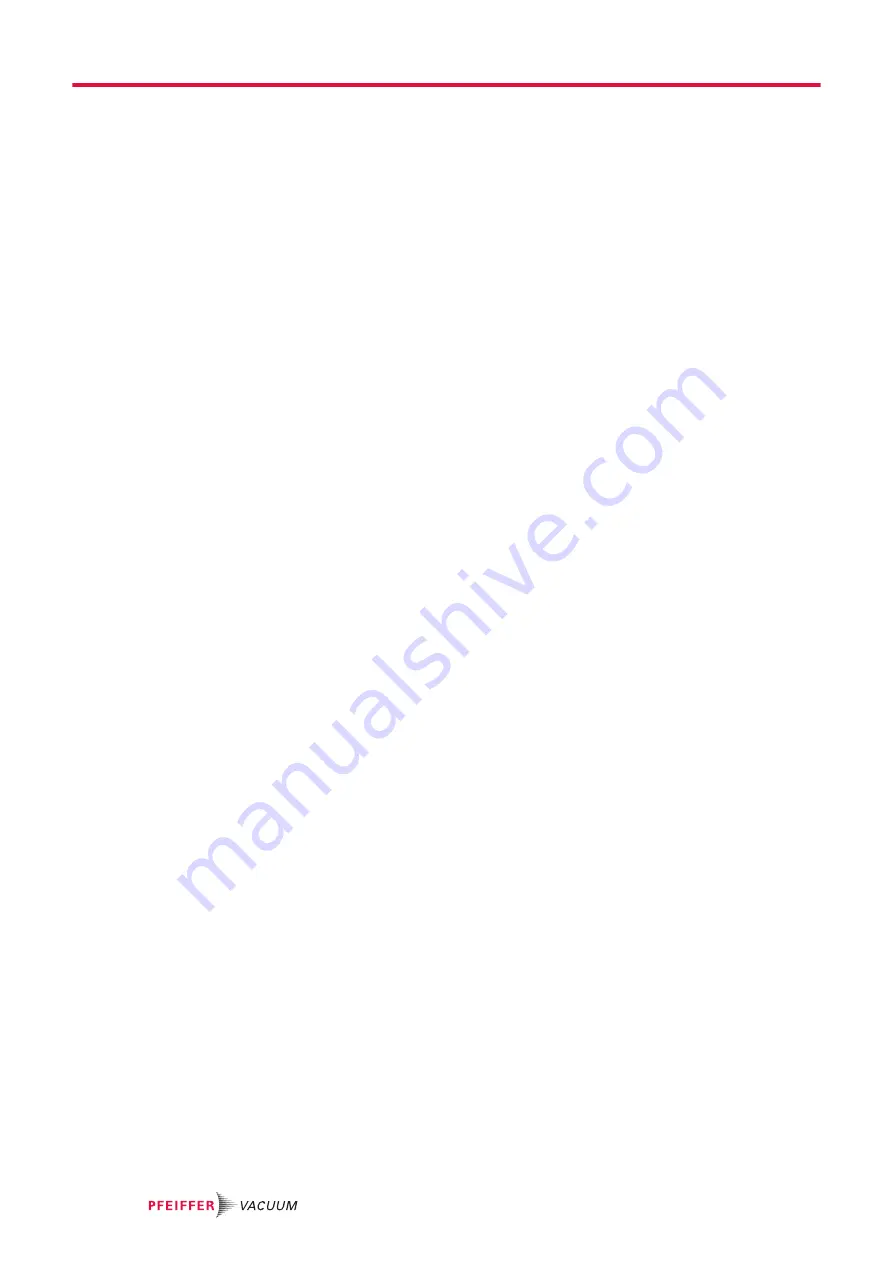
List of figures
Fig. 1:
Position of the stickers on the product
Fig. 2:
HiPace 450 design
Fig. 3:
Example: Secure against displacement and tipping caused by external vi-
brations
Fig. 4:
Recommended alignment of the fore-vacuum connection when using oil-
sealed backing pumps
Fig. 5:
Flange connection ISO-K to ISO-F, bracket screws
Fig. 6:
Flange connection ISO-K to ISO-F, hexagon head screw and tapped hole
Fig. 7:
Flange connection ISO-K to ISO-F, stud screw and tapped hole
Fig. 8:
Flange connection ISO-K to ISO-F, stud screw and through hole
Fig. 9:
Flange connection ISO-F, hexagon head screw and tapped hole
Fig. 10:
Flange connection ISO-F, stud screw and tapped hole
Fig. 11:
Flange connection ISO-F, stud screw and through hole
Fig. 12:
Flange connection CF-F, hexagon head screw and through hole
Fig. 13:
Flange connection CF-F, stud screw and tapped hole
Fig. 14:
Flange connection CF-F, stud screw and through hole
Fig. 15:
Example of fore-vacuum connection on HiPace 450
Fig. 16:
Connecting the cooling water supply
Fig. 17:
Example: Connecting the grounding cable
Fig. 18:
Connecting the electronic drive unit to a power supply pack
Fig. 19:
Removing the operating fluid reservoir
Fig. 20:
Assembling the operating fluid reservoir
Fig. 21:
Removal of electronic drive unit TC 400
Fig. 22:
Installation of electronic drive unit TC 400
Fig. 23:
Spare parts HiPace 450
Fig. 24:
Gas throughput characteristic depending on the rotation speed
Fig. 25:
Dimensions HiPace 450 | TC 400 | DN 160 ISO-K
Fig. 26:
Dimensions HiPace 450 | TC 400 | DN 160 ISO-F
Fig. 27:
Dimensions HiPace 450 | TC 400 | DN 160 CF-F
List of figures
6/64