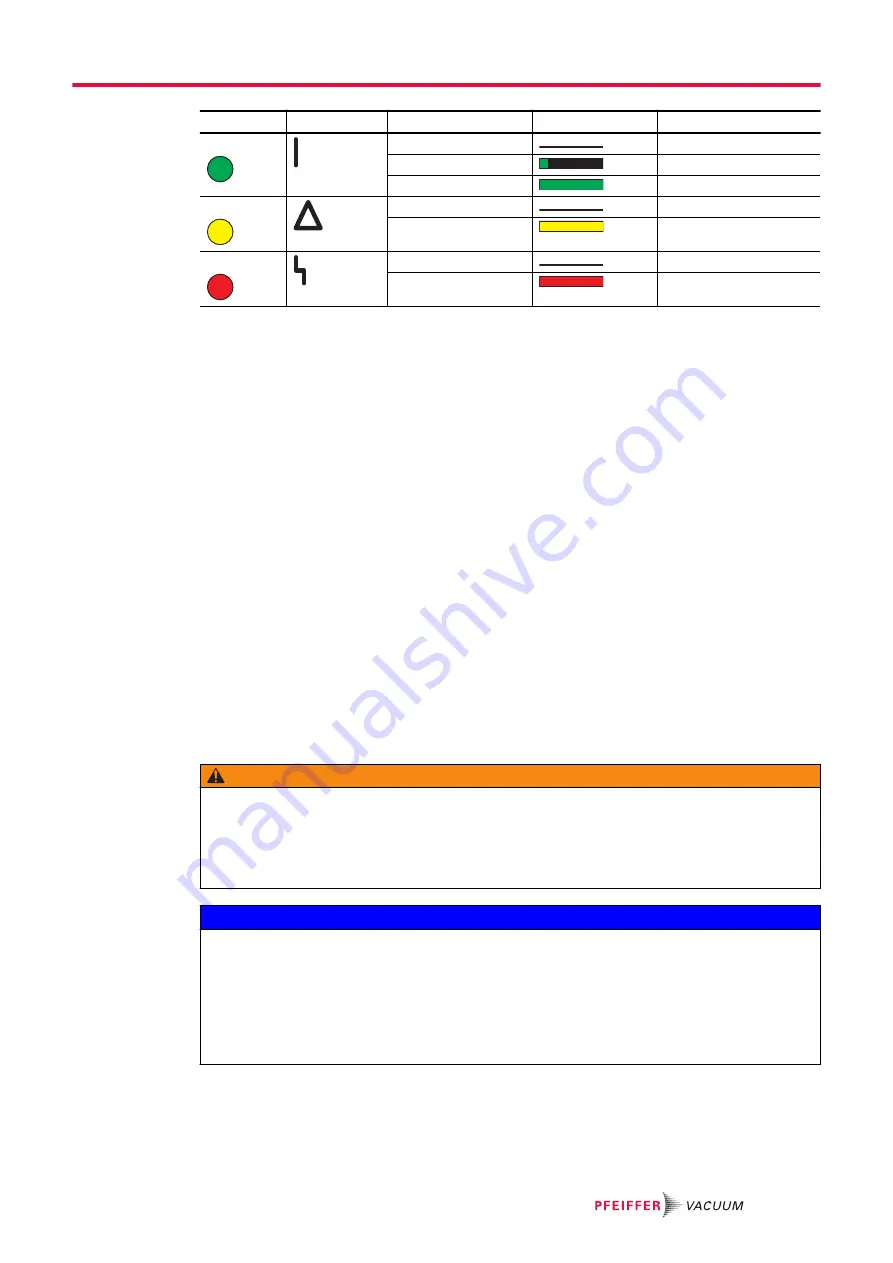
LED
Symbol
LED status
Display
Meaning
Green
Off
without current
On, flashing
"Pump OFF"
On, constant
"Pump ON"
Yellow
Off
no warning
On, constant
Warning
Red
Off
No errors
On, constant
Error
Tbl. 17:
Meaning of the LEDs
8.5.2 Temperature monitoring
Depending on the sensor type, temperature thresholds for warning and malfunction messages are stor-
ed immutably in the parameter set of the electronic drive unit. If a measured value exceeds the thresh-
old, the vacuum pump is switched to a safe state.
With an oil temperature (T > 85 °C), only a "
Warning
" is issued.
With impermissibly high temperature (T > 95 °C), the vacuum pump is switched off with an "
Error
". Af-
ter cooling down, the vacuum pump does
not
start automatically.
Acknowledge error - Query status
► Set parameter
[P:010]
to "0/1".
8.5.3 Check the lubricant level
Check the lubricant level
1. Regularly check the lubricant level while the vacuum pump is running and at operating tempera-
ture.
2. Make sure that the level is in the area at the center of the sight glass.
3. Check operating fluid fill level daily during continuous operation, and every time vacuum pump is
switched on.
8.6 Switching off and venting
WARNING
Risk of crushing on rotating parts when reaching into the open flange
The pistons continue to run in the vacuum after switching off the motor, and can trap fingers and
hands within their reach.
► Wait until the vacuum pump comes to a complete standstill.
► Secure the vacuum pump against re-start.
NOTICE
Risk of damage from gas backflow into the roots pump
Due to the backflow of process gas, the electronic equipment is susceptible to irreversible damage
caused by regenerative energy produced with rotation of the piston.
► Equip the vacuum pump with a facility that prevents the backflow of gases.
► Use, e.g. a shut-off facility on the fore-vacuum side and block the line directly after switching off
the vacuum pump.
► As an alternative, use a backing pump with integrated vacuum safety valve.
The "Pumping station" parameter
[P:010]
comprises operation of the vacuum pump with control of all
connected interfaces and configurations.
Operation
45/68