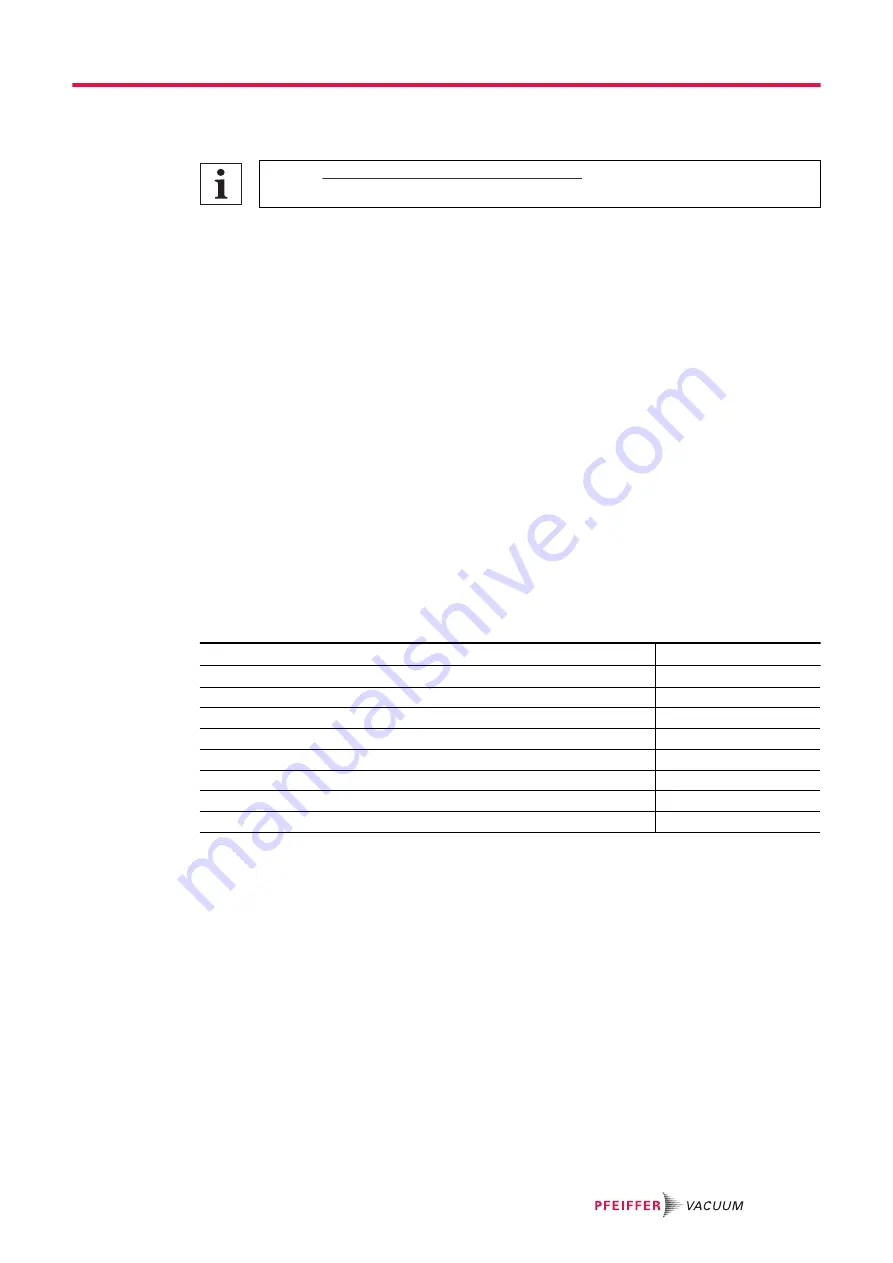
13 Accessories
range of accessories for rotary vane pumps
on our website.
13.1 Accessory information
Operating fluid level switch
Monitors operating fluid level
Operating fluid temperature switch
Monitors operating fluid temperature
Screwing flange
Enables the connection of components with ISO-K
Condensate separator
Protects the pump from liquids from inlet line or backlow from exhaust line
Dust separators
Protects the pump from particles out of processes
Magnetized gas ballast valve
Solenoid valve for remote control of gas ballast
PTC resistor tripping device
Monitors the motor winding temperature
13.2 Ordering accessories
Description
Part number
Operating Fluid Level Switch
PK 100 116
Operating Fluid Temperature Switch
PK 100 125
KAS 100, Condensate Separator
PK Z10 012
SAS 100, DN 100 ISO-K
PK Z60 512
Screw-in flange DN 100 ISO-K
PK 100 061
PTC Resistor Tripping Device 220 – 240 V AC
P 4768 052 FQ
PTC Resistor Tripping Device 24 V AC/DC
P 4768 052 FE
Magnetic Gas Ballast Valve 24 VDC
PK 100 141 -U
Tbl. 15:
Accessories
Accessories
59/70