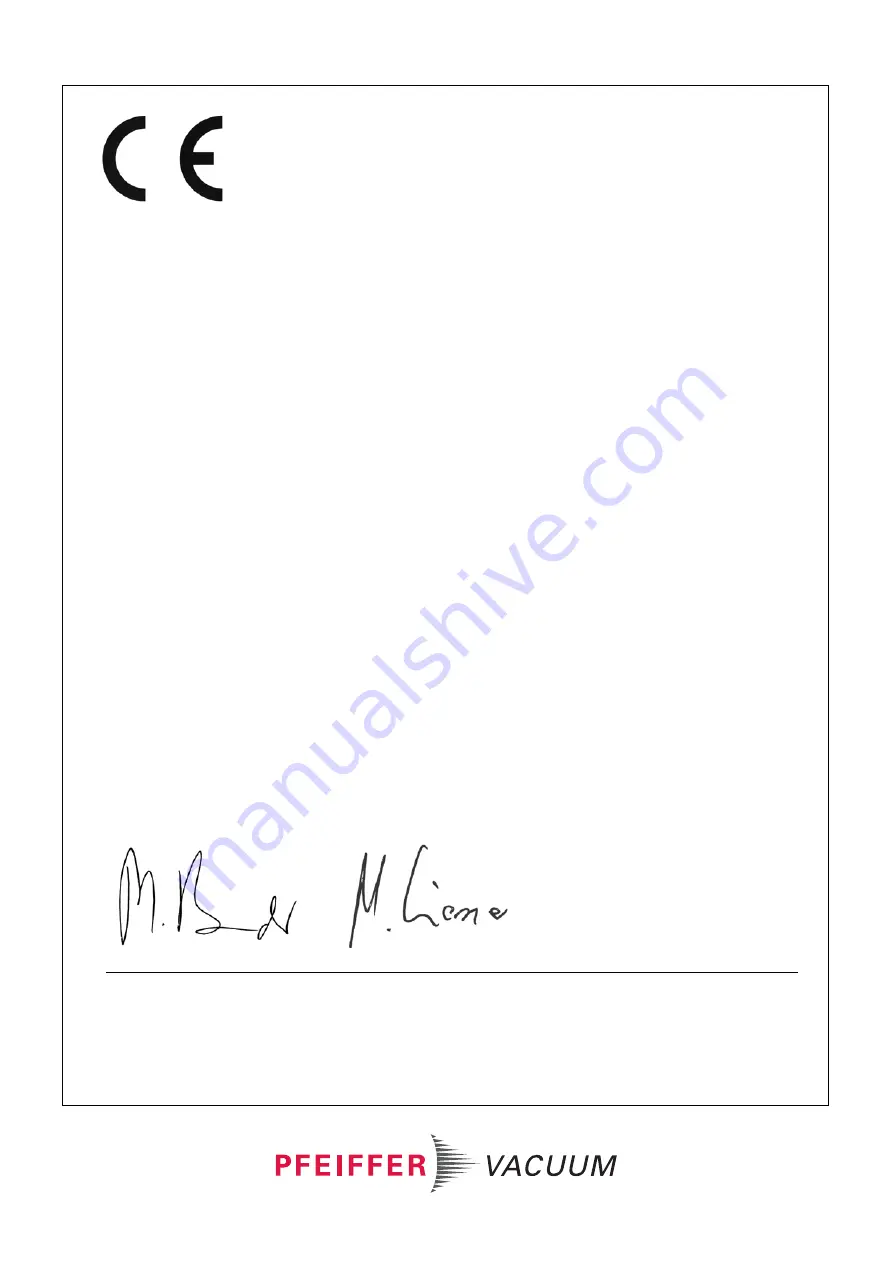
Declaration of conformity
according to the EC directive:
●
Machinery 2006/42/EC (Annex II, no. 1 A)
We hereby declare that the product cited below satisfies all relevant provisions of EC
directive "Machinery"
2006/42/EC
.
In addition, the product cited below satisfies all relevant provisions of EC directive "Elec-
tromagnetic Compatibility"
2004/108/EC
.
The agent responsible for compiling the technical documentation is Mr. Sebastian Ober-
beck, Pfeiffer Vacuum GmbH, Berliner Straße 43, 35614 Aßlar.
DuoLine
®
/DuoLine™
UNO/DUO 2.5, UNO 5, DUO 2.5 C
Guidelines, harmonised standards and national standards and specifications which
have been applied:
DIN EN ISO 12100 : 2011-03
DIN EN 61010 : 2002
DIN EN 61000-6-3 : 2007
DIN EN 1012-2 : 1996
DIN EN 61000-6-1 : 2007
DIN EN 61000-6-4 : 2007
DIN EN ISO 13857 : 2008
DIN EN 61000-6-2 : 2006
Signatures:
Pfeiffer Vacuum GmbH
Berliner Straße 43
35614 Asslar
Germany
(M.Bender)
Managing Director
(Dr. M. Wiemer)
Managing Director
CE/2011