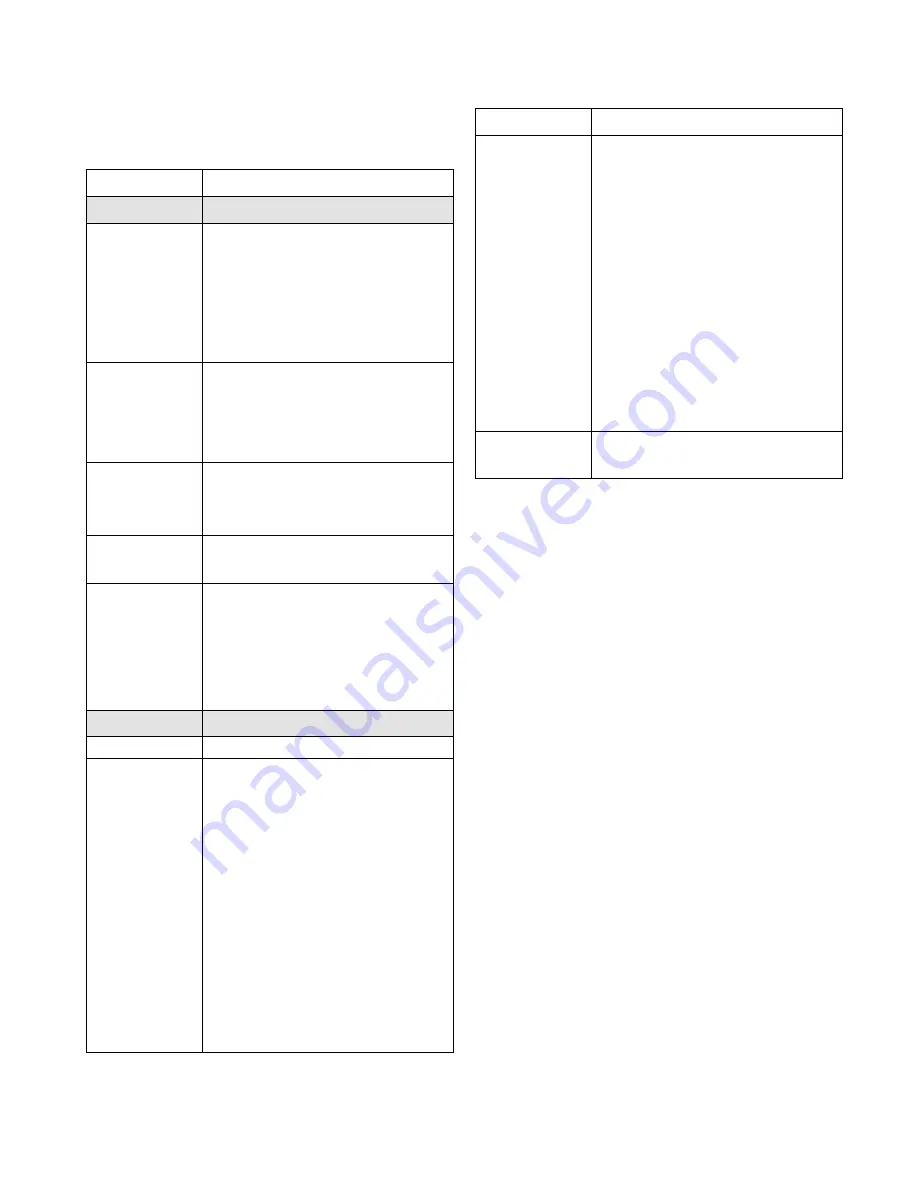
Troubleshooting Manual
31
If
Check
Spreader
Spinner Platter
does not turn
Spinner Platter Tensioning Clamp loose
Shaft Coupling Block loose
Shaft Coupling Block set screw worn
Spinner/Pump Belt loose or damaged
Pulley loose-
Gearbox
Pump
Transaxle
Hopper Opening
Plate does not
move
Plate jammed or dirty
Plate Hardware too tight
Hopper Opening Plate damaged
Hopper Cable loose or damaged
Rod Ends loose or damaged
Product does not
flow from Hopper
Product blocking one or more holes
Agitator damaged or worn
Hopper Opening Plate does not move
Third-hole
Adjustment Plate
does not move
Third-hole Cable or Lever damaged
Product jammed
Spreader Pattern
Uneven
Third-hole improperly adjusted
Spinner Platter damaged or dirty
See “Product does not flow from Hopper”
See “ Spinner Platter does not turn”
Engine RPM incorrect
Sprayer
No Spray output
Tanks empty
Spray system not primed
Suction Valve closed
Clogs -
Nozzle Strainer
Tank Strainer
Nozzle Tip
Pump
Hoses
Spinner/Pump Belt slipping, worn, damaged,
or improperly tensioned
Loose pulley-
Pump
Transaxle
Gearbox
Pump worn, damaged or dirty
Spray mix too thick or viscous
Frozen fluid
If
Check
Spray output low
Unloader Valve diaphragm dirty or damaged
Engine RPM low
Clogs -
Nozzle Strainer
Tank Strainer
Nozzle Tip
Pump
Hoses
Spinner/pump Belt slipping, worn, damaged,
or improperly adjusted
Loose pulley-
Pump
Transaxle
Gearbox
Pump worn, damaged or dirty
Spray mix too thick or viscous
Narrow Spray
Pattern
Spray Nozzles improperly Aligned
See “Spray output low”
If you are experiencing a problem that is not on the list
or are having difficulty, contact PermaGreen Tech
Support at 800-346-2001 or [email protected].