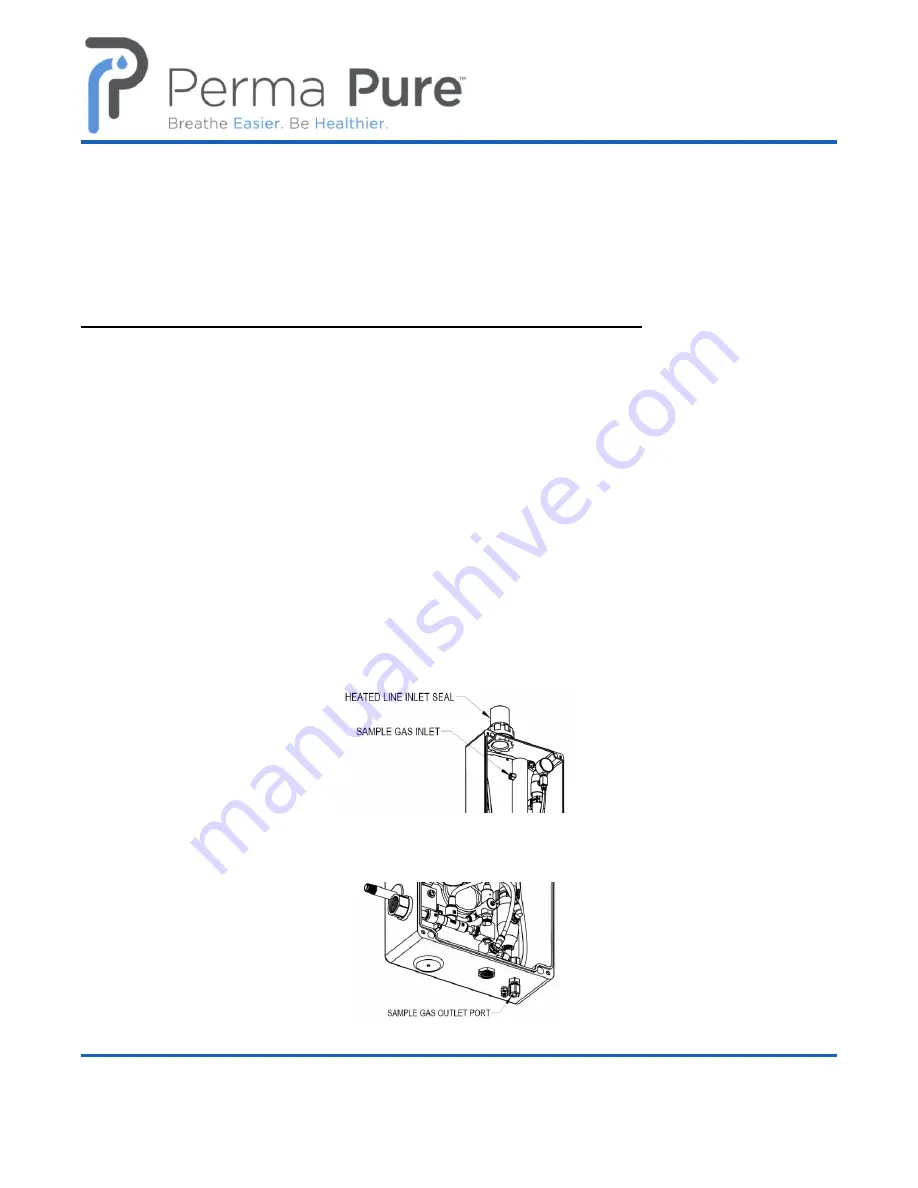
Rev 02, 09/21
Perma Pure LLC
• A Halma Company • [email protected] • www.permapure.com
Telephone: 7
32-244-
0010 • Toll Free: 800
-337-
3762 • Fax:
7
32-244-8140
1
001 New Hampshire Ave.,
L
akewood, NJ 08701 USA
6.3
U
TILITY
C
ONNECTIONS
6.3.1
Electrical Connections
This model has no electrical power requirements.
Grounding lug must be connected to earth ground to prevent electrostatic build up.
6.3.2
Instrument Air Inlet
The instrument air supply must be cleaned of particulates, liquids, and regulated to 60PSI-100PSI at the
required flow rate. Perma Pure recommends both coalescing filtering and particulate filtering of the instrument
air just before entry into the unit. Intrusion of particulates or liquid into the system will compromise
performance.
6.3.3
Heated Sample Gas Inlet and Dry Sample Gas Outlet
Run the heated sample inlet line through the heat shrink entry seal and into enclosure. Connect the sample
tubing to the compression fitting port, as indicated in the image below. Shrink entry seal tubing around the
heated sample line with a heat gun to provide a water-tight seal.
Connect the system to the sample gas analyzers or downstream sample pump via the port labeled
“Sample
Gas
Outlet”.