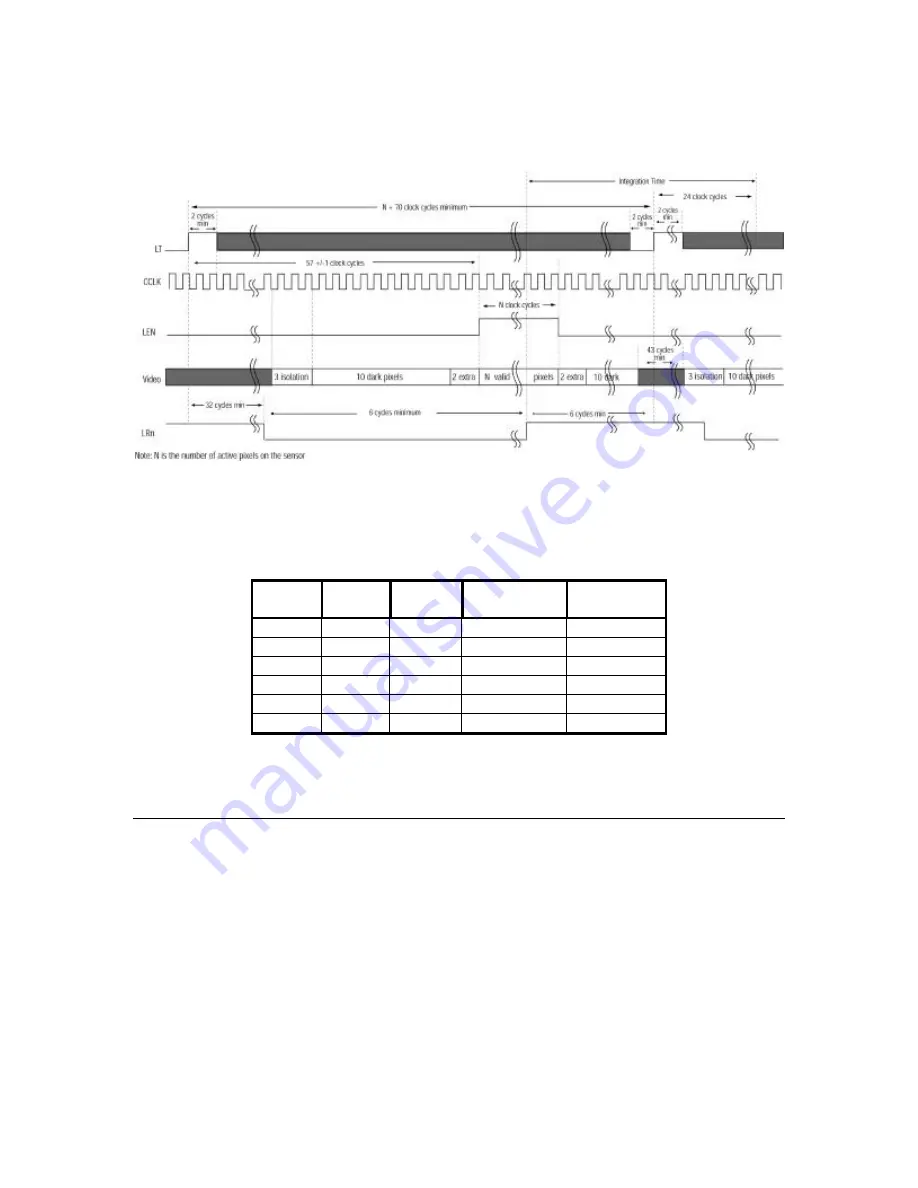
7
PerkinElmer
Optoelectronics
Figure 4 Slave Mode Timing (Camera Link
Model)
4.1.4 Line Period Limits
Table 1 Line Period Limit Definition (Camera Link Model)
Model
# Pixels
Clock
Max Line Scan
Rate
Min. Line
Scan Period
LD3521
512
20 MHz
34,364 L/sec
29.1
µ
sec
LD3522
1024
20 MHz
18,281 L/sec
54.7
µ
sec
LD3523
2048
20 MHz
9,442 L/sec
105.9
µ
sec
LD3541
512
40 MHz
68,728 L/sec
14.6
µ
sec
LD3542
1024
40 MHz
36,563 L/sec
27.4
µ
sec
LD3543
2048
40 MHz
18,885 L/Sec
53.0
µ
sec
4.2 Camera Exposure Modes (LVDS Model)
The following exposure modes are provided:
•
Master Mode
•
Slave Mode
The camera mode is automatically detected on the LVDS model.
Note:
The camera defaults to master mode on power up. If an external LT signal
is detected the camera will go into slave mode. If an unintentional LT signal
is supplied, the camera must be powered down and restarted to restore the
camera to master mode.
Summary of Contents for RETICON LD3500 Series
Page 5: ...v PerkinElmer Optoelectronics ...
Page 6: ......
Page 8: ...PerkinElmer Optoelectronics 2 Figure 1 LD3500 Series Camera Block Diagram ...
Page 34: ...PerkinElmer Optoelectronics 28 APPENDIX B Front Plate Detailed Mechanical Drawing ...
Page 36: ...PerkinElmer Optoelectronics 30 W Warranty ii Working Distance Estimating 17 ...