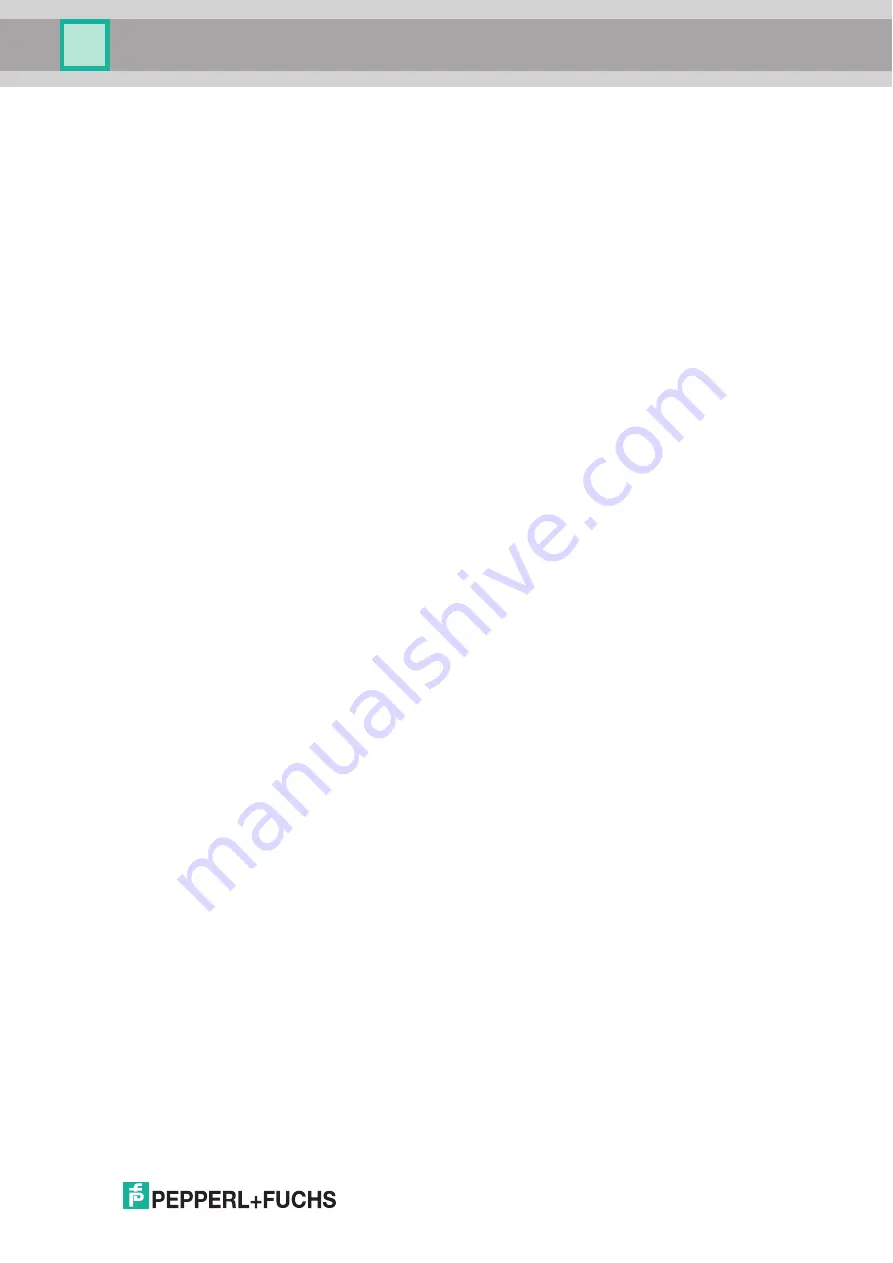
Functional Safety KFD2-UT2-(Ex)*(-1)
List of Abbreviations
20
19
-1
0
25
7
List of Abbreviations
ESD
E
mergency
S
hut
d
own
FIT
F
ailure
I
n
T
ime in 10
-9
1/h
FMEDA
F
ailure
M
ode,
E
ffects, and
D
iagnostics
A
nalysis
s
Probability of safe failure
dd
Probability of dangerous detected failure
du
Probability of dangerous undetected failure
no effect
Probability of failures of components in the safety loop that have
no effect on the safety function. The no effect failure is not used
for calculation of SFF.
not part
Probability of failure of components that are not in the safety loop
total (safety function)
Probability of failure of components that are in the safety loop
HFT
H
ardware
F
ault
T
olerance
MTBF
M
ean
T
ime
B
etween
F
ailures
MTTR
M
ean
T
ime
T
o
R
estoration
PCS
P
rocess
C
ontrol
S
ystem
PFD
avg
Average
P
robability of dangerous
F
ailure on
D
emand
PFH
Average frequency of dangerous failure per hour
PLC
P
rogrammable
L
ogic
C
ontroller
PTC
P
roof
T
est
C
overage
SC
S
ystematic
C
apability
SFF
S
afe
F
ailure
F
raction
SIF
S
afety
I
nstrumented
F
unction
SIL
S
afety
I
ntegrity
L
evel
SIS
S
afety
I
nstrumented
S
ystem
T
1
Proof Test Interval
T
service
Time from start of operation to putting the device out of service