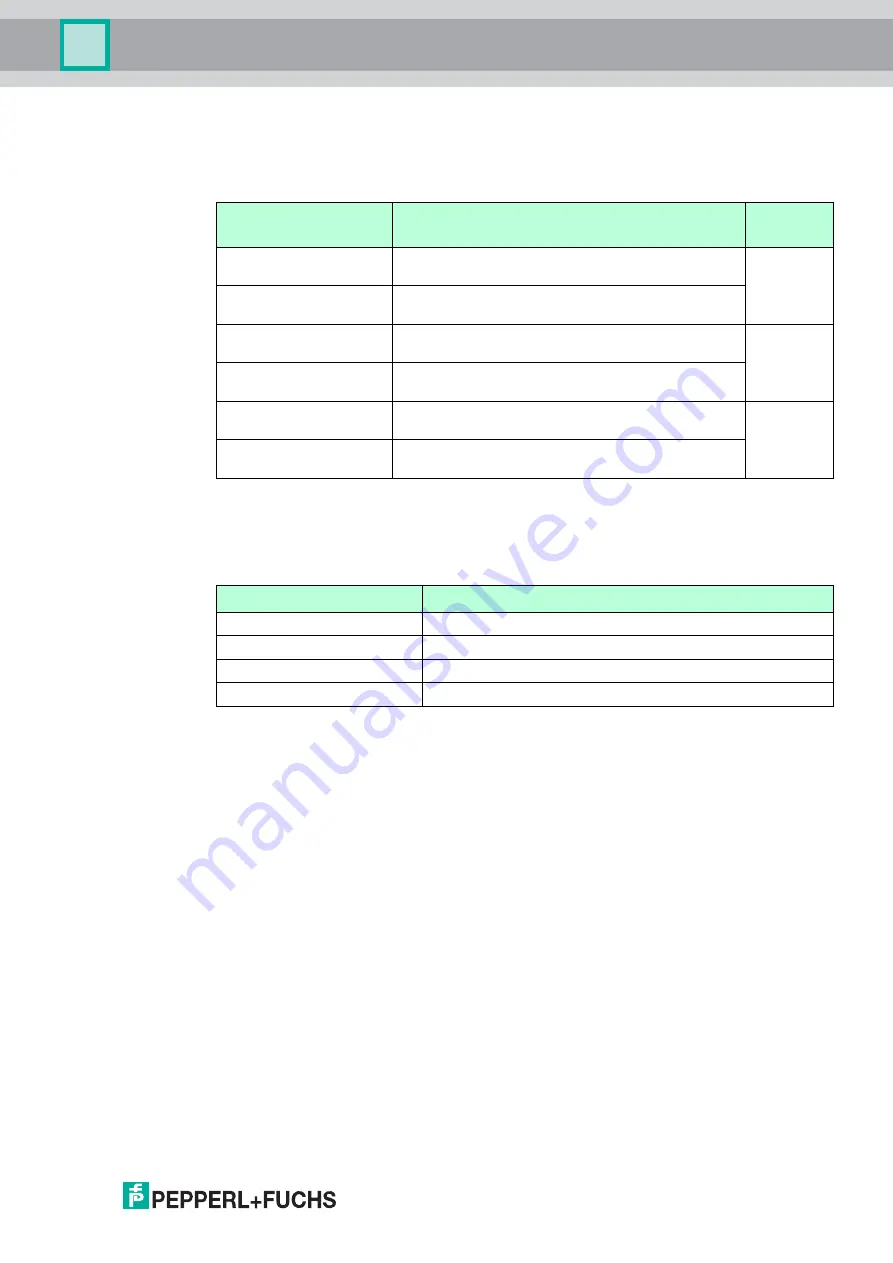
Parameterization and Operation
2
017-
06
39
4.5.8
Lead Breakage and Lead Short Circuit Monitoring
You can independently enable or disable lead short circuit and lead breakage monitoring of the
valve and position feedback sensors. Use the Lead Fault Monitoring parameter to achieve this.
The Lead Fault parameter contains the fault status of the valve and sensor connection.
Structure and content is identical to the Lead Fault Monitoring parameter.
The Sensor Fault State parameter defines the process value handling of position feedback
sensors in case of a lead fault.
4.5.9
Valve and Drive Information
You can enter information of the valve drive or transducer block in the following parameters.
The first 3 parameters are part of all FOUNDATION Fieldbus blocks. Their use depends on the
control system.
■
Strategy: Identify grouped blocks by entering a number. This number is not controlled or
used by the block.
■
Alert Key: Identification number for the plant unit which is used by the master computer to
sort, e. g., alarm or operation messages. Values from 0 ... 65535 are valid.
■
Tag Desc.: Description of the task of the TB.
■
Act. Man.: Mechanical drive manufacturer
■
Act. Model: Mechanical drive model
■
Act. Ser. Num.: Mechanical drive serial number
■
Valve Man.: Valve manufacturer
■
Valve ID: Valve model
■
Valve Type: undefined, linear, turning, other
■
Valve Ser. Num.: Valve serial number
Option
Description
Hardware
Channels
Short Circuit Sensor-A
Enable/disable lead short circuit detection for final
position feedback sensor A connection
TB1: 2
TB2: 5
TB3: 8
TB4: 11
Lead Breakage Sensor-A Enable/disable lead breakage detection for final
position feedback sensor A connection
Short Circuit Sensor-B
Enable/disable lead short circuit detection for final
position feedback sensor B connection
TB1: 3
TB2: 6
TB3: 9
TB4: 12
Lead Breakage Sensor-B Enable/disable lead breakage detection for final
position feedback sensor B connection
Short Circuit Valve
Enable/disable lead short circuit detection for valve
connection
TB1: 1
TB2: 4
TB3: 7
TB4: 10
Lead Breakage Valve
Enable/disable lead breakage detection for valve
connection
Option
Description
Set Fault State to Sensor A
Enable/disable fault handling of position feedback sensor A
Sensor A Fault State
Fault value of position feedback sensor A
Set Fault State to Sensor B
Enable/disable fault handling of position feedback sensor B
Sensor B Fault State
Fault value of position feedback sensor B