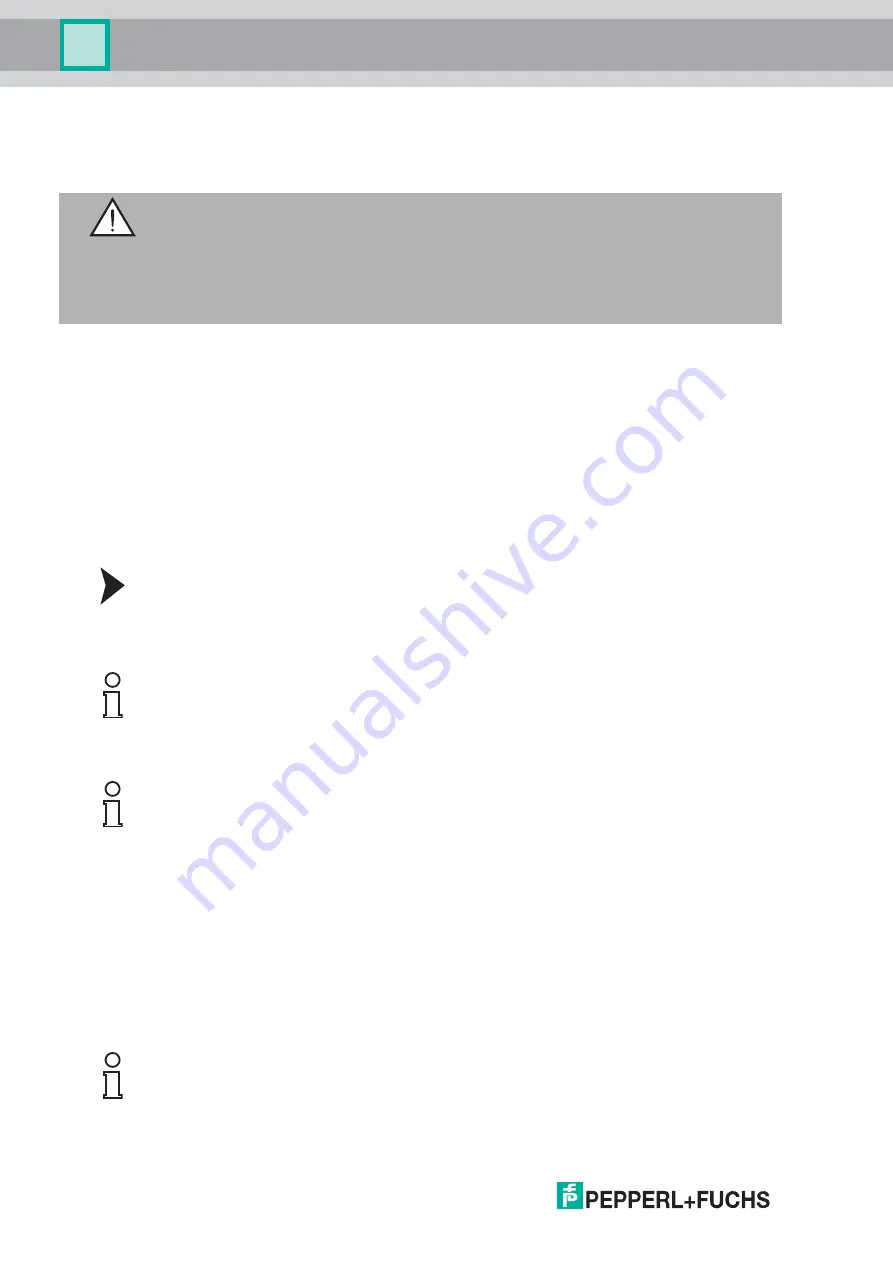
2
019-
02
16
Commissioning
4
Commissioning
4.1
Introduction
Components
To commission the module, you will require the following components:
WCS-ECG110 interface module
Cordset from the interface module to the reader
Connector for the EtherCAT
®
connection to the interface module
Ethernet cable
10 VDC...33 VDC power supply
ESI file (the ESI file can be obtained free of charge from our website www.pepperl-
Connecting the interface module
To ensure that the assembly functions correctly, you must carry out the following steps during
commissioning:
1. Assign an EtherCAT
®
address.
2. Assign an EtherCAT
®
device name.
3. Connect the module to the EtherCAT
®
network at the interface with the label "In" (cable
from master) or "Out" (further cable to the next slave).
4. Connect the process device (reader) to the interface module. For information on
commissioning the reader, please refer to the instruction manual for the reader.
5. Ground the DIN mounting rail onto which the assembly is snapped.
6. Connect the direct current to the terminals provided.
7. Use any programming tool for configuration. The ESI file can be downloaded from our
website: www.pepperl-fuchs.com. Simply enter the product name or item number in the
Product/Keyword field and click the "Search" icon.
Warning!
Danger to life due to defective work
Errors during installation and commissioning can cause life-threatening injuries and significant
property damage.
Installation and commissioning must only be carried out by trained personnel in
accordance with the safety regulations.
Note!
On delivery, the module does not yet have an IP address. In normal operation, the IP address
is usually assigned to the module by the EtherCAT
®
IO controller (PLC).
Note!
On delivery, the module does not yet have a device name. The device name is assigned to the
module via the project planning software.
Note!
A more detailed description of the individual steps is provided on the following pages.