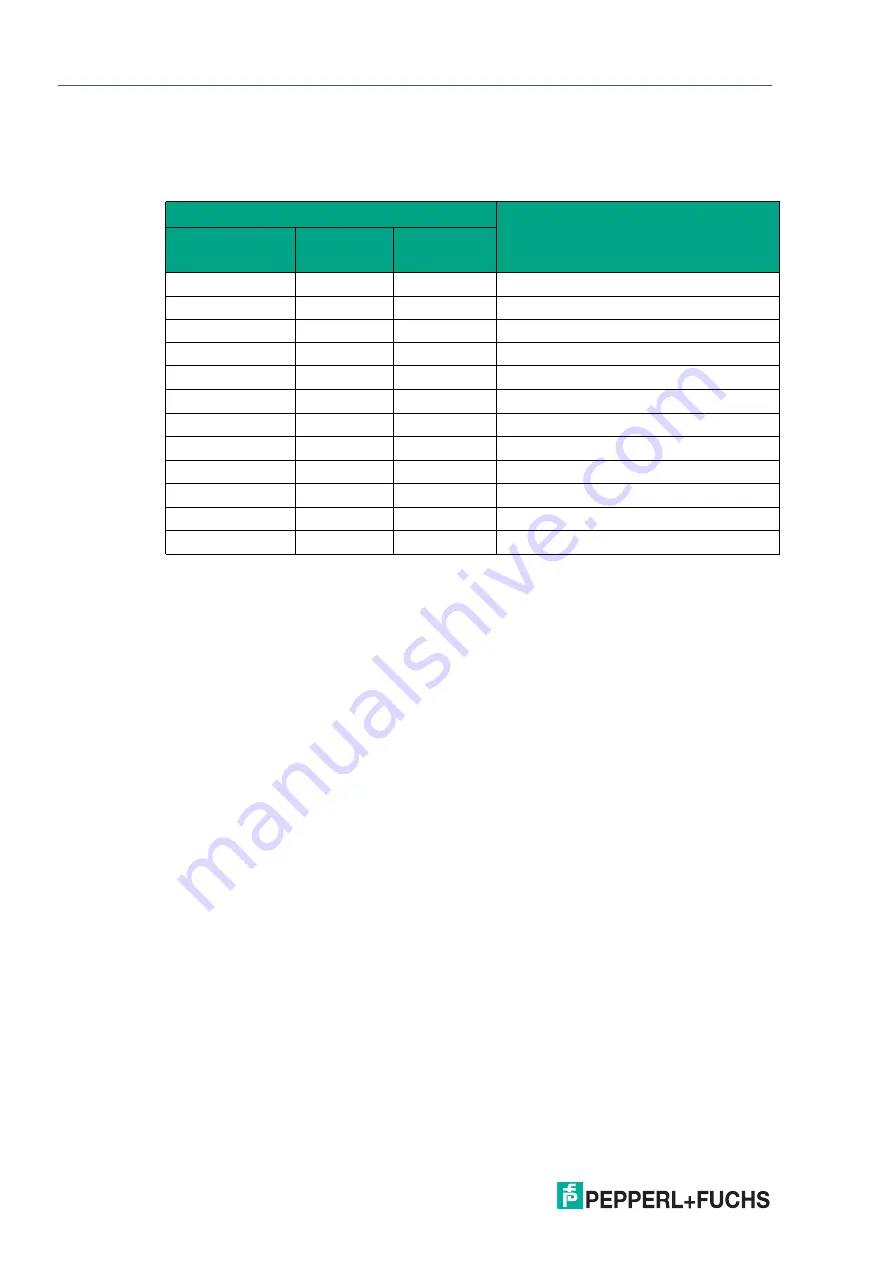
2
0
2
0
-0
9
38
Switching Signal Characteristics
The following table shows the respective switching characteristics for each combination. It is
necessaryto distinguish between the position sector (see previous figure) that is changed to
the next position sector and the status of the switching channel has shortly before the sector
change.
If the position sector is changed from sector 4 (SP1 hysteresis area) to sector 3 (= inner win-
dow area) and the SSC1 switching channel is about to switch to "high," SSC1 will switch its
contents to "low" if sector 4 exceeds sector 3.
You can set the desired measuring range as "high active" or "low active" using the "SSC1 Con-
fig Logic" (0x41 Sub 1) parameter.
These switching characteristics apply to the singlepoint mode if the "SSC 1 Config Mode"
(0x41 Sub 2) parameter is set to "Single point."
The general rule is
If the SPn-Hyst is larger than the "Config Position Overflow" parameter for an increasing mea-
sured value (Position), the switch point is at the position "Config Position Overflow."
MDC1
—
Position
Switching Characteristics of SSC1
Switching Signal 1
From "Position
Sector"
SSC1 Value
To "Position
Sector"
1
high
2
high
–
> high
2
high
3
high
–
> low
2
low
3
low
–
> low
3
low
4
low
–
> low
4
low
1
low
–
> high
4
high
1
high
–
> high
1
high
4
high
–
> high
4
high
3
high
–
> low
4
low
3
low
–
> low
3
low
2
low
–
> low
2
low
1
low
–
> high
2
high
1
high
–
> high
Table 7.2