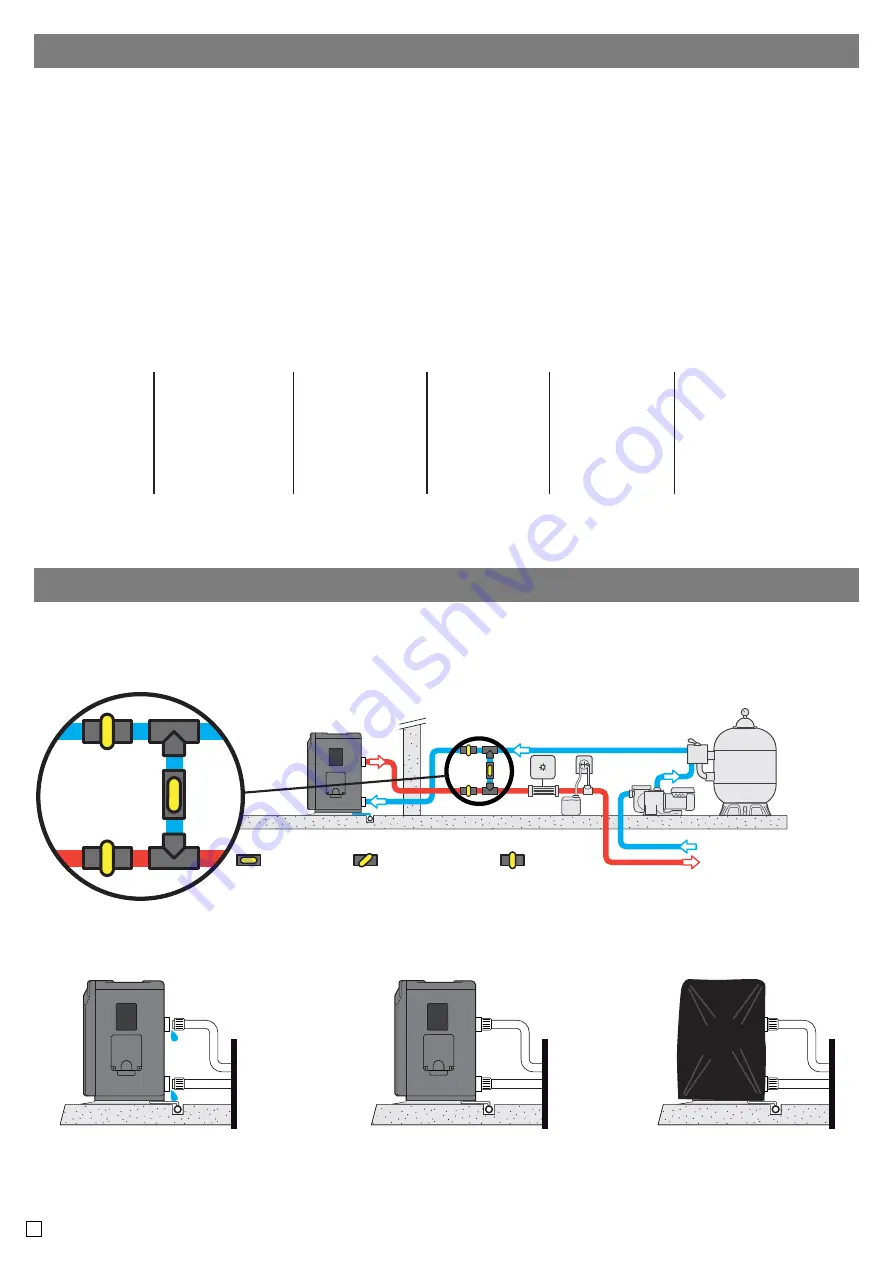
pH +/-
+60°C = 38.3 bar
+55°C = 34.2 bar
+50°C = 30.4 bar
+45°C = 26.9 bar
+40°C = 23.8 bar
+35°C = 20.9 bar
+32°C = 19.3 bar
+30°C = 18.3 bar
+28°C = 17.3 bar
+26°C = 16.3 bar
+24°C = 15.4 bar
+22°C = 14.5 bar
-16°C = 3.7 bar
-18°C = 3.3 bar
-20°C = 3.0 bar
-4°C = 6.1 bar
-6°C = 5.7 bar
-8°C = 5.2 bar
-10°C = 4.8 bar
-12°C = 4.4 bar
-14°C = 4.0 bar
+20°C = 13.7 bar
+18°C = 12.9 bar
+16°C = 12.2 bar
+14°C = 11.4 bar
+12°C = 10.7 bar
+10°C = 10.0 bar
+8°C = 9.4 bar
+6°C = 8.8 bar
+4°C = 8.2 bar
+2°C = 7.6 bar
0°C = 7.1 bar
-2°C = 6.6 bar
14
MAINTENANCE
WINTERING
–Prior to undertaking any maintenance operation on the HP, it is imperative to disconnect the power supply from the HP: there is a risk of electrocution that can
cause damages, severe injuries, and even death. Maintenance operations are to be conducted by a qualified technician.
Cleaning (must be conducted by a qualified technician at least once yearly):
–The cleaning of the inlet of the evaporators and of the outlet of the fan are necessary to maintain a sufficient yield.
–The HP outer casing must be cleaned with a damp soft cloth (microfibre for example). The use of detergent and other household products might damage the
surface of the casing and change its properties.
–The evaporator, at the rear of the HP, can be cleaned carefully using a soft brush vacuum cleaner, just a soft brush, or a stream of soft water; never use a
high-pressure hose.
Yearly maintenance, safety checks (must be conducted by a qualified technician at least once yearly):
Prior to any maintenance operation, it is imperative to power down the device and to wait a few minutes before installing pressure control devices, as the high
pressure and temperature in some parts of the cooling circuit could cause severe burns.
–Check that the electric cables are properly connected.
–Check that the earth terminals are properly connected to the earth.
–Check the state of the pressure gauge, and that the pressure is aligned with the temperature (table below), and for the presence of coolant.
1 - Turn off the power supply to the HP
2 - Fully open the bypass valve and close the HP inlet and outlet valves.
Open valve
3 - Unscrew the junctions to evacuate all the
water contained in the HP.
4 - Reconnect and slightly tighten the junctions
by hand to prevent the introduction of foreign
objects into the HP
5 - Place the provided wintering blanket
over the HP
Half-open valve
Closed valve