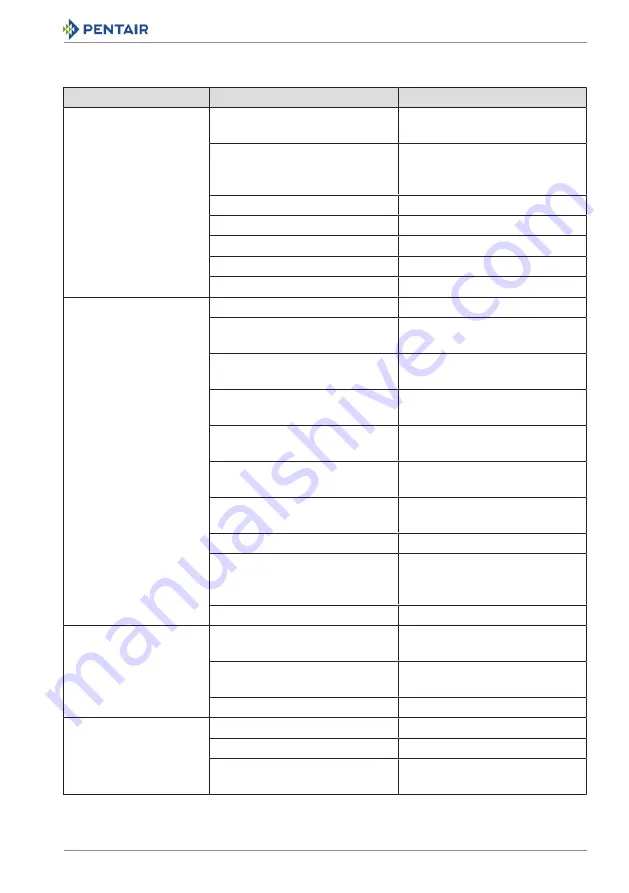
Installer manual Fleck 4600 MECH - Troubleshooting
Ref. MKT-IM-027 / C - 12.11.2019
73 / 92
10
Troubleshooting
Problem
Cause
Solution
Softener fails to
regenerate automatically
Interrupted power or switched off
power source.
Restore the controller and
connect to constant power source.
Disconnected/faulty meter cable.
Check connections in the power
head and on the meter cover.
Change the cable.
Defective power cord.
Replace cord.
Defective motor.
Change motor.
Defective controller.
Change controller.
Blocked meter.
Clean or change meter.
Bad programming.
Program correctly.
Softener delivers hard
water
By-pass valve is open.
Close by-pass valve.
No salt in the brine tank.
Add salt in the brine tank and
keep salt level above water level.
Plugged injector and/or filter.
Clean or replace injector and/or
filter.
Insufficient water flowing into
brine tank.
Check brine tank filling time and
clean flow regulator.
Hot water tank hardness.
Repeated flushing of the hot water
tank.
Leak at the distributor hose.
Ensure the distributor tube has no
cracks. Check the o-ring.
Internal valve leak.
Change seals & spacers and/or
piston assembly.
Blocked meter.
Clean or change meter.
Disconnected/faulty meter cable.
Check connections in the power
head and on the meter cover.
Change the cable.
Bad programming.
Program correctly.
Excessive salt
consumption
Improper brine refill setting.
Check use of salt and setting of
brine refill.
Too much water in the brine tank. See problem below: Too much
water in the brine tank.
Bad programming.
Program correctly.
Water pressure drop
Iron deposit in the valve inlet.
Clean the inlet.
Iron deposit in the valve.
Clean the valve and resin.
Valve inlet obstructed by foreign
elements.
Remove piston and clean the
valve.