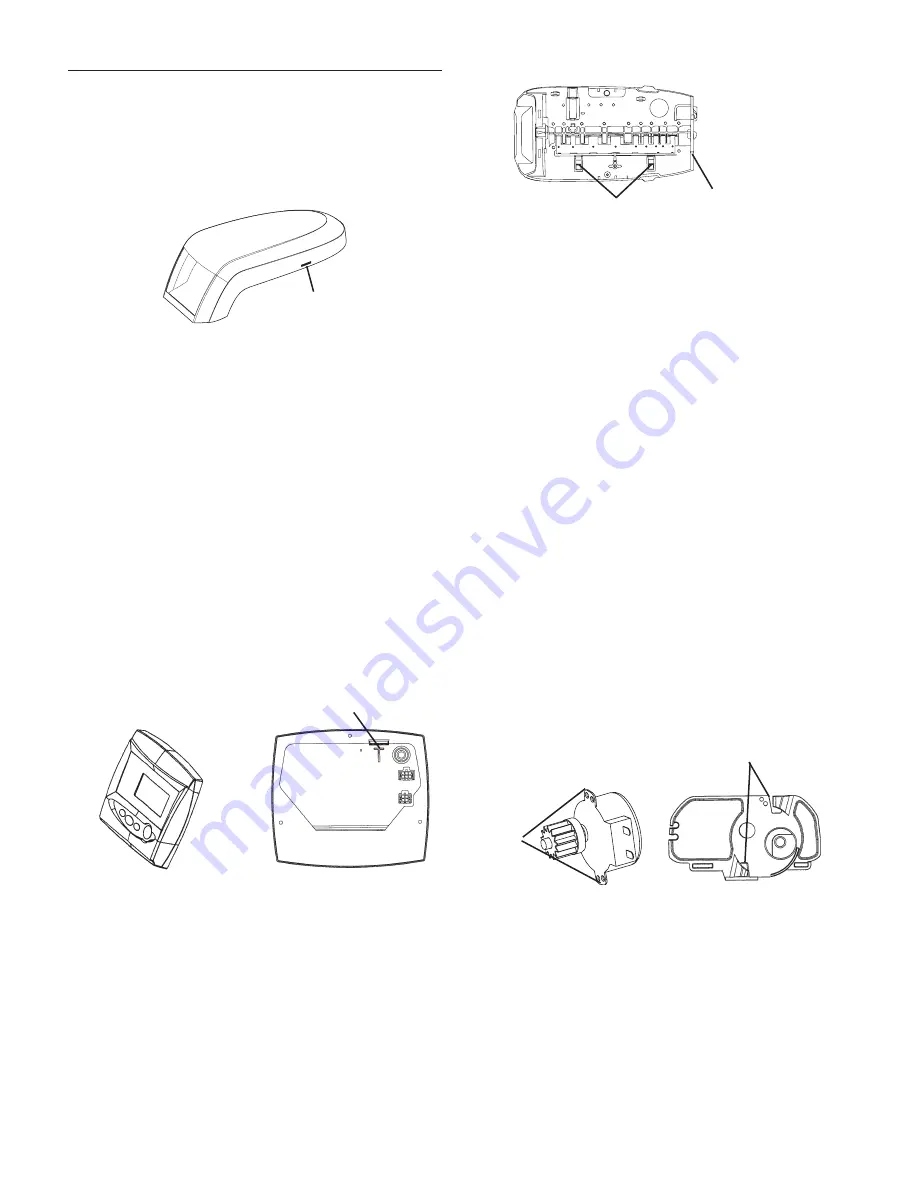
SERVICE AND MAINTENANCE
Cover
The cover provides protection for the controller, wiring, and
other components. This cover will be removed for most service
and maintenance.
When installed, the cover provides NEMA 3 water protection.
This protects from falling water up to 30 degrees from vertical.
To remove cover:
Slots
1. Grasp side edges toward rear of the valve.
2. Pull outwards until the slots in the cover clears the
projections on the top plate.
3. Lift up on the rear and pull forward to clear the
control module.
To install cover:
1. Position cover to be low in front and under the bottom edge
of the control module.
2. The cover will hook on the bottom of the controller and
drop down over the camshaft.
3. To finish, grasp the side edges and pull outward to clear
the projections on the top plate.
4. Drop down until the cover snaps in place.
Electronic Control Module
The purpose of the electronic control module is to control the
regeneration cycle. The control module has several variations.
When replacing the controller, use the same model or some
functions may not work. This is an electronic controller that is
programmable and uses input/output signals.
To remove control module:
Trip Lever
1. Disconnect power to the unit.
2. Remove valve cover.
3. Press trip lever to release module from top plate.
4. Pivot the top forward and up.
5. Remove any wire connections. Wire connectors have a
locking tab that must be squeezed before removing.
NOTE:
There is no need to label the wires. The keyed
connectors will only plug back into one site.
To install control module:
Wire Clips
Slots for Motor and
Turbine Harness
1. Be sure the power is disconnected.
2. Check model.
3. Check routing of wires and plug them into the controller.
Connectors will snap in place. Be sure that wires are
properly managed through the clips on top plate. This will
prevent the wires from being caught in the camshaft.
4. Place bottom of module in position. The bottom will fit into
a clip.
5. Pivot the top into position and snap in place. The controller
should be secure.
If you are ready to program the controller, then power can be
applied by plugging in transformer.
Drive Motor
The drive motor is open loop and receives commands from the
control module. The motor has a pinion gear that meshes with
the camshaft gear to drive (rotate) the camshaft.
During operation, rotation forces the motor into its mounting
position and screws or bolts are not needed.
NOTE:
Some units will have a shipping peg in the top motor
mount. The peg can be removed and discarded. This
peg is not required for motor operation.
To remove motor:
1. Disconnect power to the unit.
2. Remove cover.
3. Pull off wiring connector.
4. Grasp the motor body and rotate counterclockwise.
5. Pull motor out.
To install motor:
Mounting
Tabs
Slots
1. Insert gear through hole on top plate and mesh with
camshaft. Cam may need to be rotated slightly.
2. With motor ears flat to the rear of the top plate, rotate
clockwise until mounting tabs are engaged in slots.
3. Reconnect wires.
NOTE:
It is not necessary to pre-position the camshaft or
the motor. When the controller is powered up the
camshaft will be rotated to the "home" position.
24
•
AUTOTROL
®
740/760 Control 255 & Performa Series Valves (268, 268FA) Service Manual