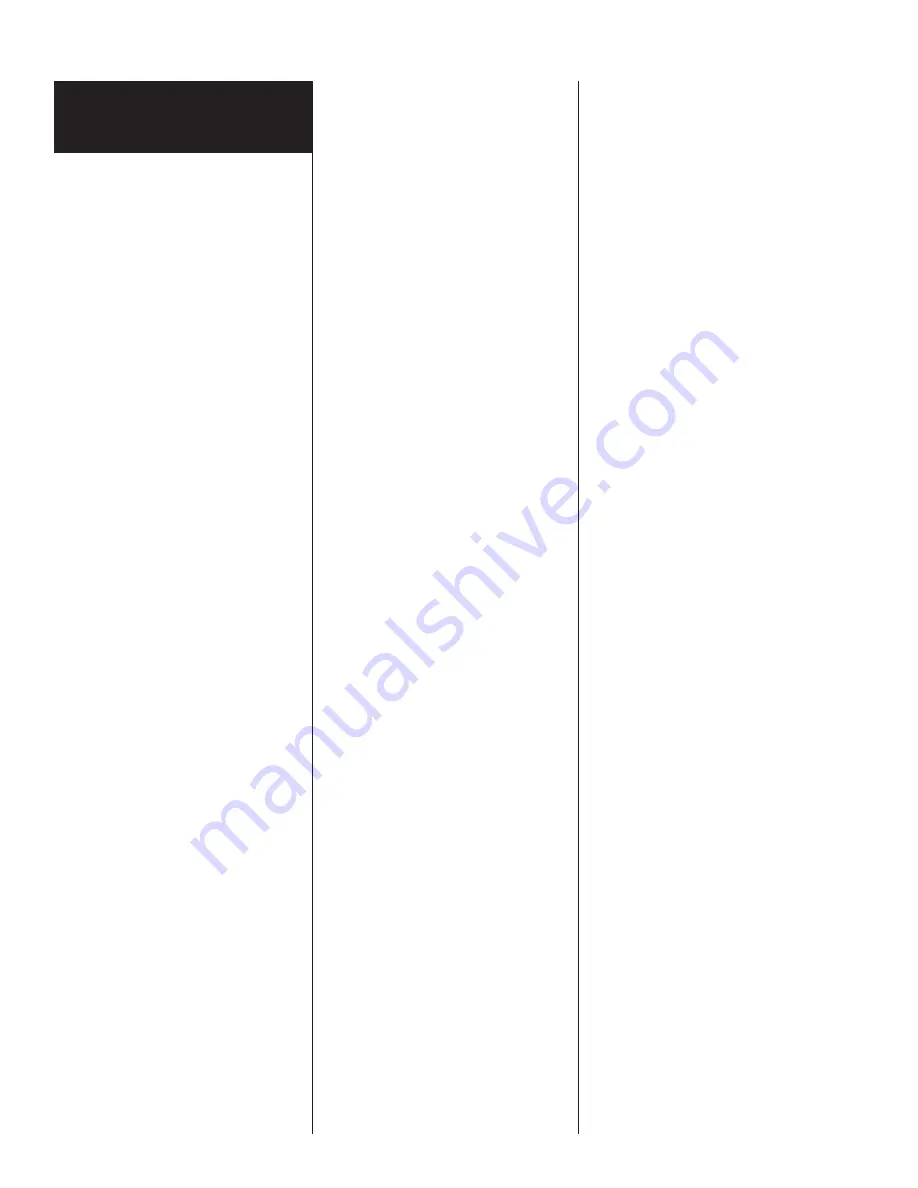
6
Pump
Maintenance
1. If only the stator is damaged, it
may not be necessary to
com plete ly dismantle pump as
stator and housing can be lifted
from pump without dis turb ing
seals or bearings.
2. Drain all oil from upper housing.
Remove drain plug in bottom
of bearing housing, and
re move con nec tion box to
allow air to enter.
3. When connection box is lifted
off, con nec tion wires to motor
will be exposed. These wires
are tagged with a metal
marker giving wire num
ber.
Disconnect wires and remove
connection box.
4.
After chamber is drained,
remove hold-down bolts on
motor housing and lift off. Use
care in lifting as the seal failure
connecting wire must be
disconnected before hous ing is
completely re
moved. See
sectional drawing.
5.
The stator is held in the
housing with a bolted-in
retaining ring and pre
vent
ed
from rotating bolt.
6. Remove the retaining ring and
socket head cap screw.
7. After ring is removed, turn
hous ing upright and bump on
hard
wood block. This should
jar the stator loose and allow it
to drop out.
8. Thoroughly clean housing
before replacing new stator.
Replace sta
tor and make all
wire con nec tions to con nec tion
box before re
plac
ing housing
on pump. See motor lead
connection drawing. This is
important as leads must
be tucked behind the windings
by using hands up through
rotor core.
IMPORTANT: Use only butt
con nec tions on the wires.
Do not tape leads as oil will
de te ri o rate the tape and cause
dam age to stator and bearings.
9. Check top bearing. If the bearing
is clean and does not turn
rough, bearings can be reused.
If bear ings are damaged with
dirt or heat, they must
be replaced. See ad
di
tion
al
instructions on re plac ing seals
and bearings.
10.Replace stator housing onto
seal chamber and bolt in place.
Be sure seal failure wires are
con
nect
ed before housing is
assembled.
Be sure O-ring seal has been
re placed. If O-ring is nicked or
cut, replace with new ring.
This ap plies to all O-rings used
in as sem bly.
11.After all leads are reconnected
in the con nec tion box, make a
high voltage ground test on
each wire. The only wire that
should show ground is the
green power lead and the
ground head in the aux
il
ia
ry
control cable.
12.For safety, complete pump
should be air checked under
water for leaks.
Install air valve in plug opening
of motor housing and charge
housing with about 10 psi
of air. Be sure air is dry. Do
not use air line where water
may be trapped in the line.
Submerge com plete unit un der
water and check for leaks.
If seals were okay, refill seal
cham
ber with oil. Lay pump
on side for this oil filling with
oil fill hole upright. Do not
completely fill; leave oil about
1" below plug hole. Use only
Hydromatic sub mers ible oil or
high grade trans form er oil in
this chamber. Re
place plug;
use Permatex on threads.
13.Refill motor chamber with
oil through con nec tion box
opening. Use high grade,
non-syn thet ic
trans form er
oil or Hydromatic spe
cial
submers
ible oil. Fill hous
ing
until oil covers top of the
wind ings. Leave air space in
top for expansion.
NOTE: Oil must cover top
of stator.
Replacing Seals and Bearings:
1.
Drain all oil from motor
chamber and seal chamber
as described.
2. Remove motor housing as
de scribed in re plac ing stator.
3.
Remove bolts that hold
bearing housing to volute. Lift
bearing housing and rotating
unit off and set assembly on its
side. Remove socket head
screw and washer at the
impeller end of the shaft.
Hold
ing the shaft stationary,
re move the impeller from the
shaft by tap ping the end of the
impeller blades.
4. To remove seal plate, take out
the sock
et head screws and
using screws in back-off
holes, pry plate loose. This
will also force seal off if not
already removed.
5. Remove snap ring. Pull seal
if it is free. If not free, it
can be forced off when shaft
is removed.
5A.The flame ring must be
removed. It is recommended
Hydromatic Kit #51700-900-7
Summary of Contents for Hydromatic H3HX Series
Page 9: ...9 H3HX...
Page 11: ......