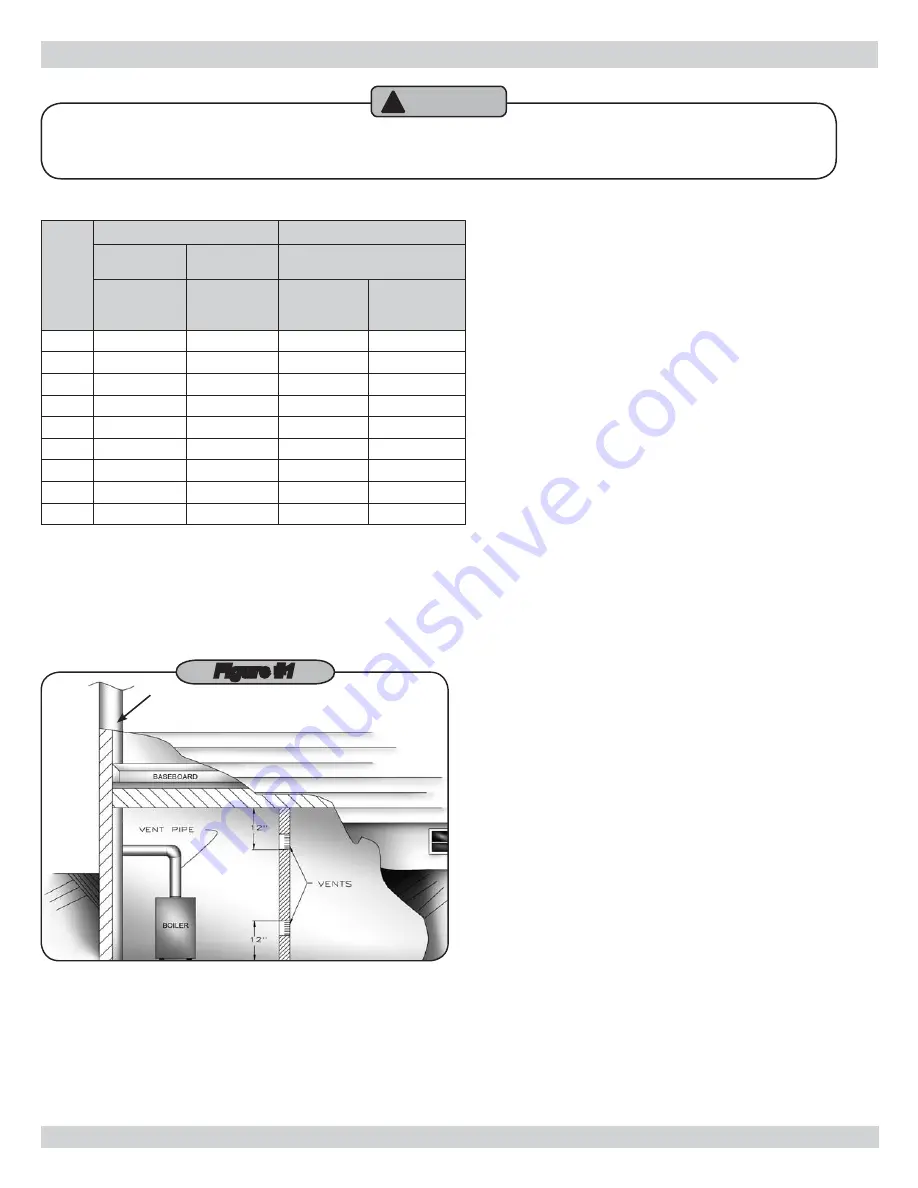
6
VENTILATION & COMBUSTION AIR
COMBUSTION AIR REQUIREMENTS
(Minimum Square Inches Requirement)
Model
No.
Unconfined Area*
Confined Area**
Inside
Combustion Air
Outside
Combustion Air
Outside Combustion Air
1 Sq. In./1000
Btu/Hr.
(Fig. #3)
1 Sq. In./5000
Btu/Hr.
(Fig. #4)
Vertical Ducts
1 Sq. In./4000
BTU/Hr.
Horizontal Ducts
1 Sq. In./2000
BTU/Hr.
15B045
100
10
13
25
15B070
100
15
19
38
15B096
100
20
25
50
15B120
125
25
32
63
15B145
150
30
38
75
15B175
175
35
44
88
15B195
200
40
50
100
15B245
250
50
63
125
15B295
300
60
75
150
* A space whose volume is not less than 50 cubic feet per 1000 BTU per hour of all
appliances installed in that space (cubic feet of space = height x width x length)
** A space whose volume is less than 50 cubic feet per 1000 BTU per hour of all
appliances installed in that space (cubic feet of space = height x width x length)
Air openings to combustion area must not be obstructed. By following the instructions below,
adequate combustion air can be maintained.
WARNING
!
Ventilation of the boiler room must be adequate to provide
1.
sufficient air to properly support combustion per the latest
revision of the National Fuel Gas Code, ANSI Z223.1.
Figure #1
CHIMNEY OR
TYPE B VENT PIPE
When a boiler is located in an unconfined space in a
2.
building or conventional construction frame, masonry or
metal building, infiltration normally is adequate to provide
air for combustion and ventilation. However, if the equip
-
ment is located in a building of tight construction (See the
National Fuel Gas Code, ANSI Z223.1 latest revision), the
boiler area should be considered as a confined space.
In this case air for combustion and ventilation shall be
provided according to Step 5. If there is any doubt, install
air supply provisions in accordance with the latest revision
of the National Fuel Gas Code.
When a boiler is installed in an unconfined space in a
3.
building of tight construction, air for combustion and ven
-
tilation must be obtained from outdoors or from spaces
freely communicating with the outdoors. A permanent
opening or openings having a total free area of not less
than 1 square inch per 5000 Btu per hour of total input
rating of all appliances shall be provided. Ducts may be
used to convey makeup air from the outdoors and shall
have the same cross-sectional area of the openings to
which they are connected.
When air for combustion and ventilation is from inside
4.
buildings, the confined space shall be provided with two
permanent openings, one starting 12 inches from the
top and one 12 inches from the bottom of the enclosed
space. Each opening shall have a minimum free area
of 1 square inch per 1000 Btu per hour of the total input
rating of all appliances in the enclosed space, but must
not be less than 100 square inches. These openings must
freely communicate directly with other spaces of sufficient
volume so that the combined volume of all spaces meets
the criteria for an unconfined space. (Figure #1)
When the boiler is installed in a confined space and all air
5.
is provided from the outdoors the confined space shall be
provided with one or two permanent openings according
to methods A or B. When ducts are used, they shall be
of the same cross sectional area as the free area of the
area of the openings to which they connect. The minimum
dimension of rectangular air ducts shall be not less than 3
x 3 inches or 9 square inches.
When installing two openings, one must commence with-
A.
in 12 inches from the top and the other within 12 inches
from the bottom of the enclosure. The openings shall
communicate directly, or by ducts, with the outdoors or
spaces (crawl or attic) that freely communicate with the
outdoors. One of the following methods must be used to
provide adequate air for ventilation and combustion.
Summary of Contents for 15B SERIES
Page 2: ......
Page 15: ...15 Wiring Diagram 24V Standing Pilot...
Page 16: ...16 Wiring Diagram 24V Intermittent Ignition...
Page 17: ...17 Wiring Diagram 24V Standing Pilot WITH LWCO...
Page 18: ...18 Wiring Diagram 24V INTERM IGNITION WITH LWCO...
Page 31: ...31...
Page 32: ...85 Middle Rd Dunkirk NY 14048...