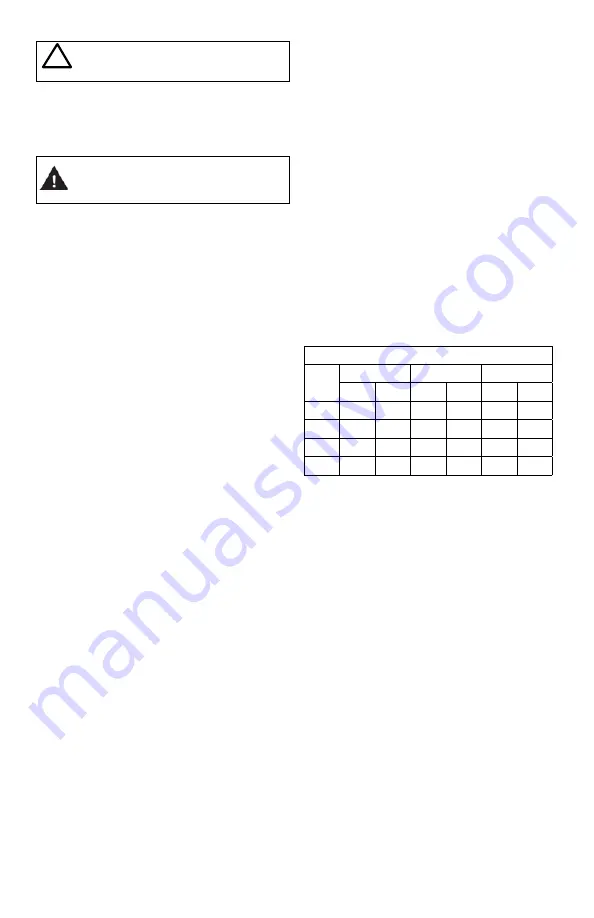
A qualified electrician must perform all the
wiring.
1. GENERAL INFORMATION
1.1. Read this Instruction Manual thoroughly prior to any work.
Work should be undertaken by qualified persons only.
ATTENTION!
Important information for installers of
this equipment!
This equipment is intended for installation by technically
qualified personnel. Failure to install it in compliance with
national and local electrical codes, and with motor suppliers
recommendations, may result in electrical shock or fire hazard,
unsatisfactory performance, and equipment failure. Installation
information is available from pump manufacturers and directly
from motor suppliers. Retain this information sheet with the
equipment for future reference.
WARNING
Serious or fatal electrical shock may result from failure to
connect the motor, control enclosures, metal plumbing, and all
other metal near the motor or cable, to the power supply ground
terminal using wire no smaller than motor cable wires. To reduce
risk of electrical shock, disconnect power before working on or
around the water system.
1. LOCATION
The pump should be installed in a dry, accessible place not
subject to freezing temperatures. If installed in a pump pit or
other location subject to dampness, proper ventilation must be
provided to avoid moisture damage to the electrical equipment.
2. PIPING
Galvanized steel or plastic pipe is recommended. If copper or
other dis-similar metal piping is used, a di-electric union or
bushing is recommended where the piping is connected to the
pump body. The pipe used should be cleaned and free of scale.
Ream ends of pipe to remove burrs. Check threads to see that
they are clean and not damaged. Horizontal runs of suction
pipe must slope upwards from the well to the pump to avoid air
pockets in the line which will make it difficult, if not impossible, to
prime the pump. The recommended slope is one inch in ten feet.
If pump must be offset an appreciable distance from the well,
the size of horizontal pipe should be increased to reduce
friction losses.
If using di-electric bushing, hand start bushing into female end of
pump housing (or other female connection) first. Use a six-sided
socket to tighten the bushing.
The bushing should be fully inserted into the female
connection. After the male end of the bushing is fully installed, hand
start pipe (or other male connection) into the female end of the
bushing. Failure to follow these guidelines may damage the bushing.
Caution should be taken to not cross-thread the bushing.
3. FLUSHING
If the pump discharge line is connected to pressure tank or
house service, disconnect it and flush and clean the system by
* Time delay fuses and circuit breakers (Single Phase).
For distances of 100 feet and over from meter to motor, larger
wire than shown may be required.
5. MOTORS
Motors are equipped with sealed ball bearings and require little
attention.
If motor repeatedly stops, cools off, and starts again, the cause
or trouble must be located and corrected. Do not cover motor
with canvas or other material that may interfere with proper air
circulation and cause over-heating.
6. PRESSURE SWITCH
The pressure switch is set at the factory to start the pump at
30 PSI and stop it at 50 PSI. In the event a change is necessary,
remove the switch cover and adjust either the operating
pressure or differential between start and stop (if available) by
turning screws, marked on switch, in the direction required.
Wiring directions are given on the pressure switch may
damage the bushing. Caution should be taken to not
cross-thread the bushing.
CAUTION
!
temporarily wasting the water outdoors or to drain. The pump
should be operated until the water runs clear, without sand, mud
or rust.
This procedure will eliminate the danger of pumping dirty water
into the pressure tank and home appliances. When water runs
clear, re-connect discharge line to tank and service.
4. WIRING (Use copper conductors only)
Be certain that wire and fuses of correct size are installed. Be
certain the phase, voltage, and cycles of the supply circuit are
the same as that shown on the motor name plate.
It is strongly recommended that a separate electric line, well
protected against fire, be run from electrical service to the pump,
with a fused switch box at the pump.
In the event of fire, this precaution will permit continuous
operation of your pumping system. For added safety, the pump
and motor should be properly grounded to the well casing or to a
separate ground rod driven eight feet into the ground.
NOTE: For proper fuse, circuit breaker and wire sizes in your
area, follow local codes. Otherwise:
Wire Gage and Standard Fuse Sizes
MOTOR
SIZE
WIRE SIZE
*FUSETRON
*CIRCUIT BRKR
115 V
230 V
115 V
230 V
115 V
230 V
1/2 HP
12
12
20 amp 15 amp 20 amp 15 amp
3/4 HP
10
12
25 amp 15 amp 30 amp 15 amp
1 HP
8
12
30 amp 20 amp 35 amp 20 amp
1 1/2 HP
6
10
35 amp 25 amp 40 amp 20 amp