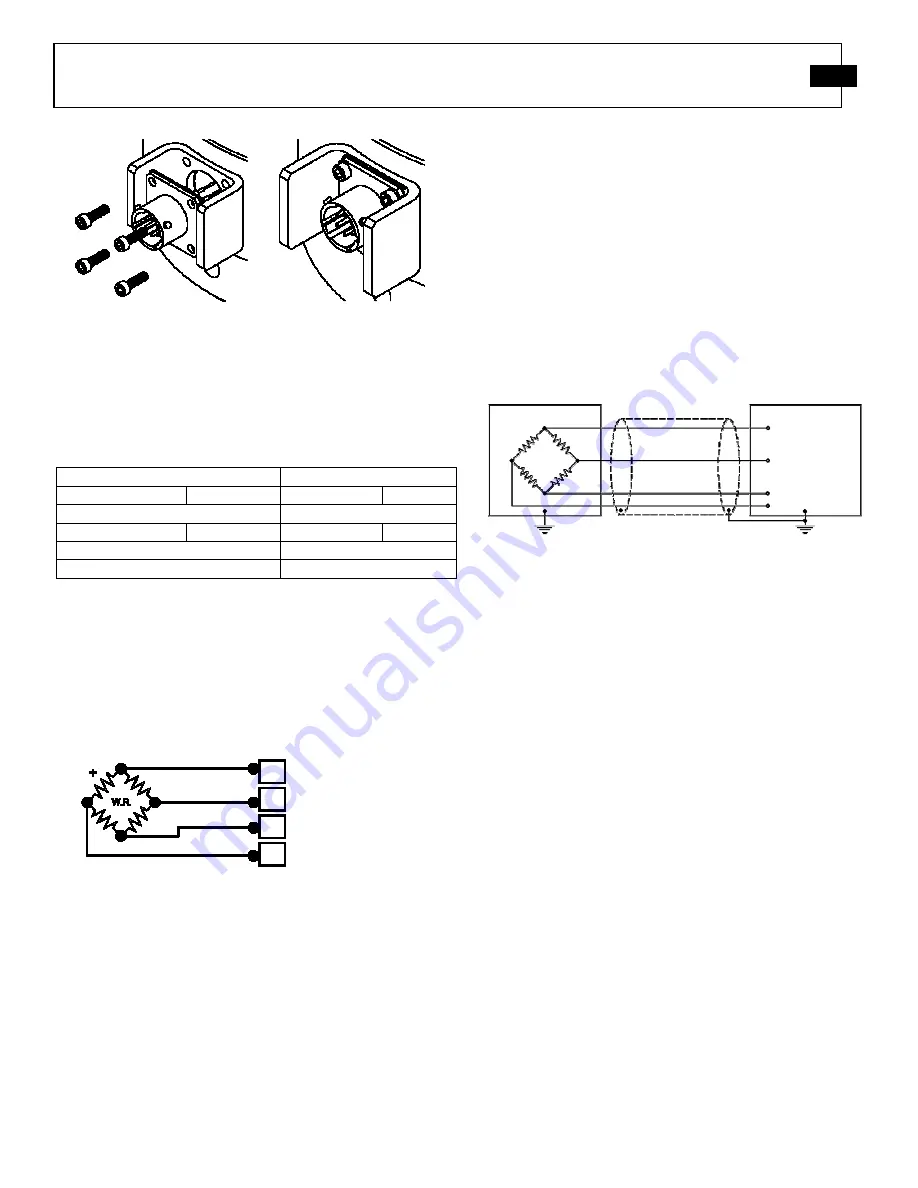
PCB Load & Torque, Inc.
Toll-Free in USA 866-684-7107
716-684-0001
www.pcbloadtorque.com
GENERAL PURPOSE LOW PROFILE LOAD CELL OPERATION MANUAL
5
5.0 ELECTRICAL INSTALLATION
5.1 Electrical Drawing / Western Regional Std.
All load cells are wired following the Western Region
Standard. All models utilize strain gages configured into a
Wheatstone Bridge Circuit to produce the primary sensing
element. The four-arm Wheatstone bridge configuration is
shown below in Figure 11.
The gages are bonded to the load cell's structure.
Typically, a regulated DC or AC excitation is applied
between A and D of the bridge. When a force is applied to
the load cell, the Wheatstone bridge becomes unbalanced,
causing an output voltage between B and C, which is
proportional to the applied load. This configuration allows
for temperature and pressure compensation, as well as
cancellation of signals caused by forces not directly
applied to the axis of the applied load. Output is typically
expressed in units of mV/V of excitation.
5.2 Cable & Grounding Considerations
Proper grounding and shielding is required to prevent
electrical noise in strain gage load cell measuring systems.
The cable must be shielded twisted pairs with a drain wire.
Cable shields must be grounded only at one end, for example,
on the instrument or control system ground. The load cell
case is grounded by mechanical attachment to the structure to
which it is mounted.
The instrument or control system is grounded through its
power cord. Ground loops and measuring system wiring may
result in unstable or noisy signals.
A simple test with a voltmeter connected between the power
cord ground and the structure on which the load cell is
mounted can confirm that the structure has been properly
grounded. If the power cord ground and structure ground are
not at the same potential, it may be necessary to provide a
secure structure ground, perhaps by driving a copper rod and
attaching a ground strap.
6.0 CALIBRATION
Every general purpose low profile load cell purchased from
PCB Load & Torque, Inc. has been fully calibrated in tension
and compression per ISO/IEC 17025 procedures, and meets all
published specifications. Each load cell will come with a
calibration certificate designated with matching model and
serial numbers. PCB Load & Torque also offers calibration
services on an on-going basis.
6.1 Calibration Certificate Description
Calibration reports supplied with PCB Load & Torque general
purpose low profile load cells contain valuable information to
assist the customer in use of the equipment. A separate
calibration report is provided for tension and compression
calibrations
on
each
bridge.
Calibration
procedures,
equipment, and reports comply with ISO/IEC 17025.
Load Cell Receptacle “A”:
PT02E-10-6P
Mating Connector:
PT06A-10-6S
PCB Item No:
181-012A
Load Cell Receptacle “B”:
PC04E-10-6P
Mating Connector:
PC06A-10-6S
PCB Item No:
182-025A
Load Cell Receptacle “C”:
PT02E-12-8P
Load Cell Receptacle “D”:
PC01E-12-8P
Table 6
– Electrical Connection Options
Figure 12
- Grounding
Test Rig Ground
Power Supply
Instrument Ground
Cable Shielding
Load Cell
C
A
D
B
- Signal White
- Excitation Black
+ Excitation Red
+ Signal Green
Figure 11 - Western Regional Strain Gage Committee Wiring Code
Figure 9 - Attach the Connector
Protector (54823-02) using #4-40 x
3/8” Socket Head Cap Screws
Figure 10 - Fully Assembled