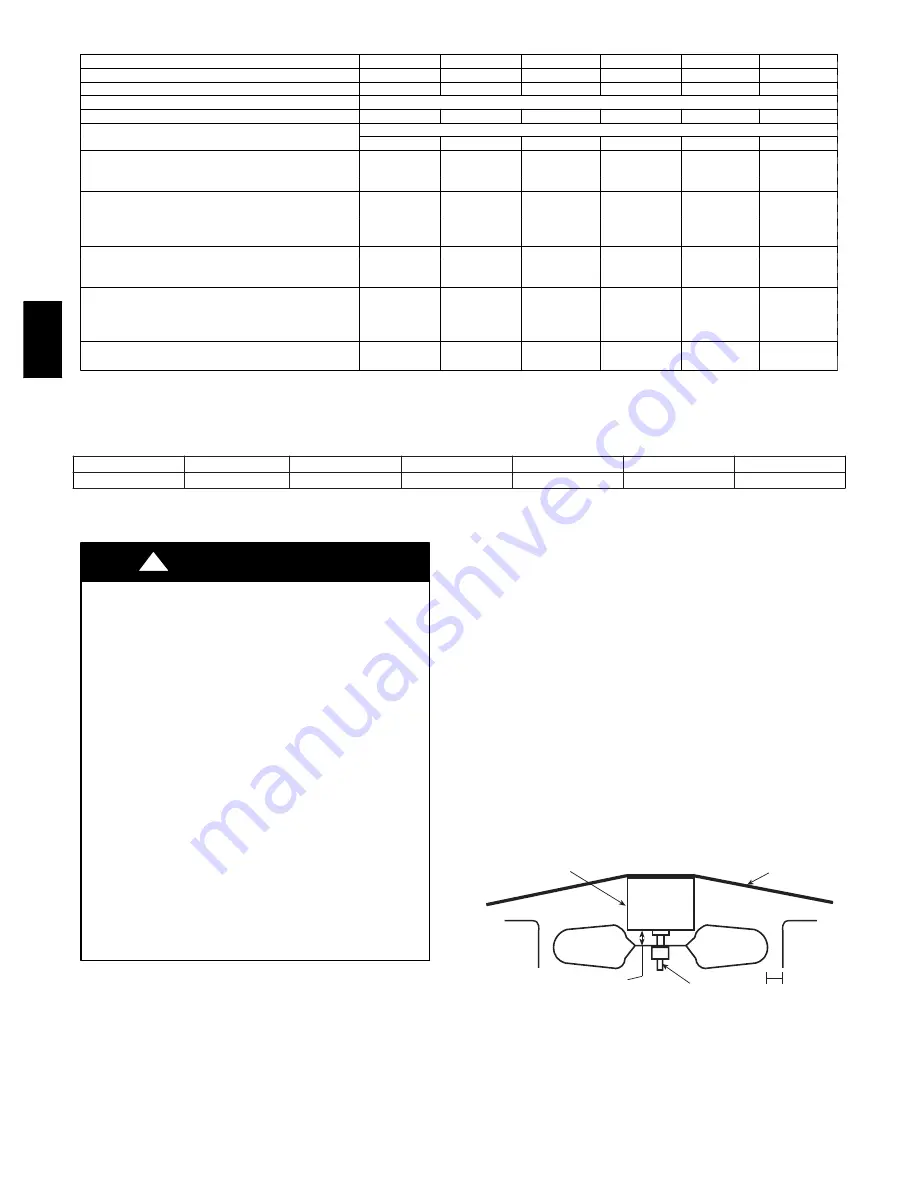
10
Table 1—
Physical Data--Unit PA3P
UNIT SIZE
024
030
036
042
048
060
NOMINAL CAPACITY (ton)
2
2--1/2
3
3--1/2
4
5
OPERATING WEIGHT (lb.)
420
425
432
553
559
564
COMPRESSOR
Scroll
REFRIGERANT (R--22) Quantity (lb.)
5.9
6.0
7.2
7.8
12.4
12.0
REFRIGERANT METERING DEVICE
AccuRater
®
ORIFICE OD (in.)
0.065
0.070
0.080
0.084
0.088
0.098
OUTDOOR COIL
Rows
…
Fins/in.
2
…
21
2
…
21
2
…
21
2
…
21
2
…
21
2
…
21
Face Area (sq. ft.)
10.2
11.9
13.6
19.4
19.4
19.4
OUTDOOR FAN
Nominal Cfm
2200
2800
3000
3500
3500
4200
Diameter
22
22
22
22
22
22
Motor HP (RPM)
1/8 (825)
1/8 (825)
1/8 (825)
1/8 (825)
1/4 (1100)
1/4 (1100)
INDOOR COIL
Rows
…
Fins/in.
3
…
17
3
…
17
4
…
17
3
…
17
3
…
17
4
…
17
Face Area (sq. ft.)
3.7
3.7
3.7
4.7
5.7
5.7
INDOOR BLOWER
Nominal Airflow (Cfm)
800
1000
1200
1400
1600
1750
Size (in.)
10x10
10x10
10x10
11x10
11x10
11x10
Motor HP (RPM)
1/3 (1050)
1/3 (1050)
1/2 (1000)
1/2 (1075)
1/2 (1075)
1.0 (1040)
RETURN--AIR FILTERS (IN.)*
20x24x1
20x24x1
20x24x1
24x36x1
24x36x1
24x36x1
Throwaway
*Required filter sizes shown are based on the larger of the ARI (Air Conditioning and Refrigeration Institute) rated cooling airflow or the heating airflow velocity
of 300 ft/minute for throwaway type. For permanent filters, follow filter manufacturer’s recommendations for filter size based on allowable face velocity. Air filter
pressure drop for non---standard filters must not exceed 0.08 in. wc.
Table 2—Minimum Airflow for Safe Electric Heater Operation (Cfm)
SIZE
024
030
036
042
048
060
Cfm
800
1000
1200
1400
1600
1750
PRE--START--UP
FIRE, EXPLOSION, ELECTRICAL SHOCK HAZARD
Failure to follow this warning could result in personal injury
or death and/or property damage.
1. Follow recognized safety practices and wear protective
goggles when checking or servicing refrigerant system.
2. Relieve and recover all refrigerant from system before
touching or disturbing anything inside terminal box if
refrigerant leak is suspected around compressor terminals.
3. Never attempt to repair soldered connection while
refrigerant system is under pressure.
4. Do not use torch to remove any component. System
contains oil and refrigerant under pressure.
5. To remove a component, wear protective goggles and
proceed as follows:
a. Shut off electrical power to unit and install lockout
tag.
b. Relieve and reclaim all refrigerant from system
using both high-- and low--pressure ports.
c. Cut component connecting tubing with tubing
cutter and remove component from unit.
d. Carefully unsweat remaining tubing stubs when
necessary. Oil can ignite when exposed to torch
flame.
!
WARNING
Proceed as follows to inspect and prepare the unit for initial start--up:
1. Remove all access panels.
2. Read and follow instructions on all DANGER, WARNING,
CAUTION, and INFORMATION labels attached to, or
shipped with unit.
3. Make the following inspections:
a. Inspect for shipping and handling damages, such as
broken lines, loose parts, disconnected wires, etc.
b. Inspect for oil at all refrigerant tubing connections and on
unit base. Detecting oil generally indicates a refrigerant
leak. Leak test all refrigerant tubing connections using
electronic leak detector, or liquid--soap solution. If a
refrigerant leak is detected, see following
Check for
Refrigerant Leaks
section.
c. Inspect all field-- and factory--wiring connections. Be
sure that connections are completed and tight.
d. Ensure wires do not touch refrigerant tubing or sharp
sheet metal edges.
e. Inspect coil fins. If damaged during shipping and
handling, carefully straighten fins with a fin comb.
4. Verify the following conditions:
a. Make sure that outdoor fan blade is correctly positioned
in fan orifice (See Fig. 12).
b. Make sure that condensate drain pan and trap are filled
with water to ensure proper drainage.
c. Make sure that all tools and miscellaneous loose parts
have been removed.
FAN GRILLE
MOTOR
1/8" MAX BETWEEN
MOTOR AND FAN HUB
MOTOR SHAFT
1/2ý
C99009
Fig. 12 -- Fan Blade Clearance
PA
3P