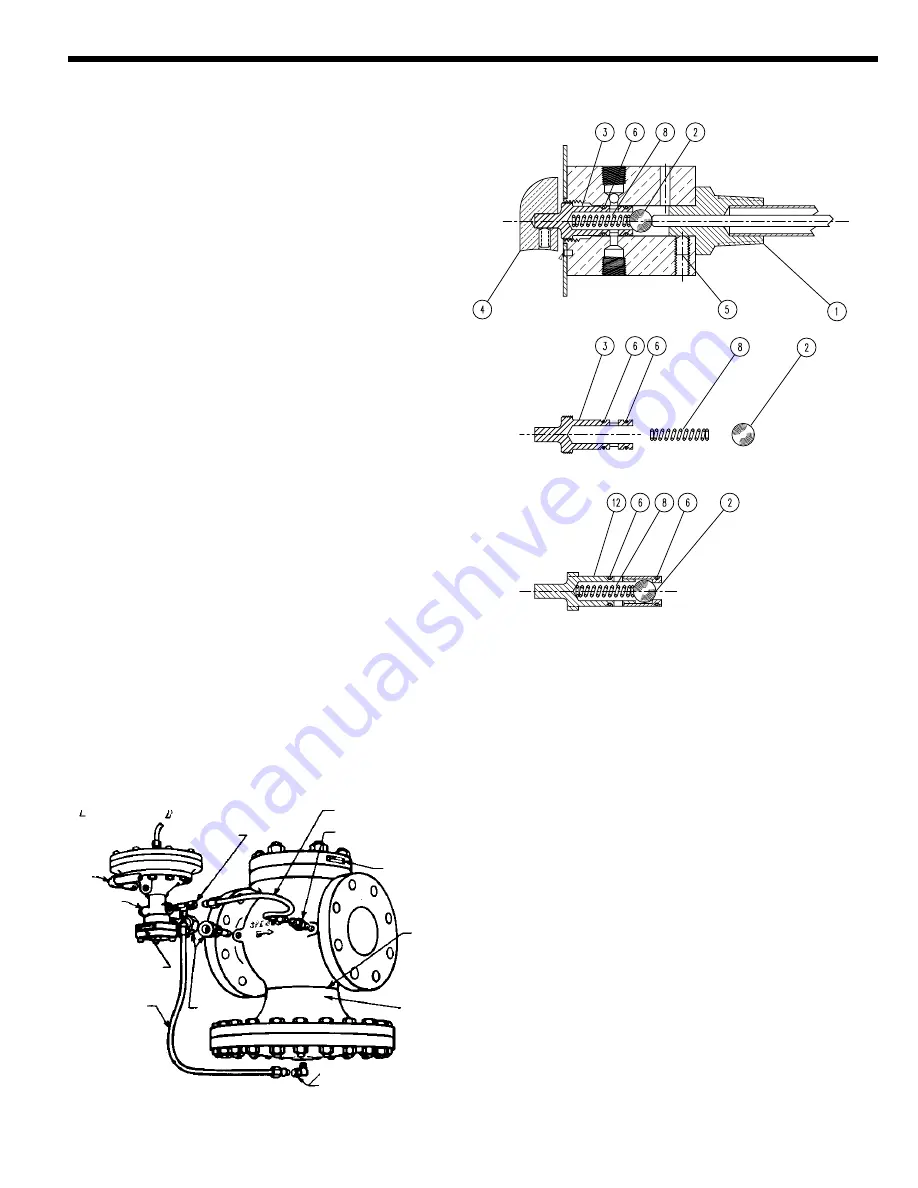
FAILURE TO OPEN
1. Check supply gage to be sure it shows 2 psi higher than the
required signal pressure.
2. Turn adjusting knob to top of temperature range. Pressure
should go to within 2 or 3 pounds of supply pressure. If not,
check for dirt in sensitivity screw and ball seating surface.
FAILURE TO CLOSE OR OVERRIDING
DELIVERY PRESSURE
1. Adjusting knob may have been tampered with.
2. If air pressure will not bleed down when adjusting knob is
turned to bottom of range, it is likely that vent is plugged.
Sensitivity screw (7) improperly adjusted (open too wide).
ERRATIC CONTROL
1. Hunting
2. Gradual wandering over too wide a spread.
3. Fast over and under rides are the result of fast load changes,
usually accentuated by the thermostat being located at a point
where it cannot immediately sense a change in conditions.
INSTALLATION FAULTS
1. Poor circulation through heater. Constant circulation should be
employed.
2. Traps on the return may be discharging erratically or may be
improperly installed.
3. Sticky check valve.
4. High lift to condensate hot well. Gravity drainage from heater
should be arranged or return pump installed.
DISMANTLING
1. Remove sensitivity screw (7) and clean.
2. Unlock knob set screw. Loosen and move adjusting knob (4)
out to clear stop on dial plate and lock to shaft. Unscrew
spool (3) from body by rotating adjusting knob
counterclockwise.
3. Care should be taken not to damage O-rings (6). Examine for
nicks and other defects.
4. Examine spool (3) and ball (2) for defects.
5. Clean spool and ball with air pressure.
6. Reassemble.
TESTING & CALIBRATING
Reverse or Direct Acting
1.
Plug the pilot control air port and apply supply pressure 2 psi
above the control range to the supply air port.
2.
Open the sensitivity screw (7) one turn while establishing a
steady system temperature.
Reverse Acting (T61 & T63) Pilots Only
(Control pressure decreases with increasing temperature)
1.
Turn the spool (3) clockwise to the point where the invar rod,
ball and seat are in contact. The control gauge should show
pressure near the top of the control range.
2.
Turn the spool counter-clockwise until the control pressure is
at the middle of the range.
3.
Continue to turn the spool counter-clockwise until the low
end of the range is reached. Adjust the sensitivity screw as
required so this occurs within a 5° change on the dial. The
control pressure should vary from the minimum to the
maximum (15 or 30 psi) with a 10° change of the dial setting.
When used with an A-pilot the minimum is 3 psi, when used
with a control valve the minimum is the lower end of the
bench range.
FIGURE 3
FIGURE 2
3
Bleedport Bend
No. 5A Restriction
Elbow—Type E
No. 5B Open
Elbow—Type E2
No. 4A Bleedport
Serial No. Plate
Do not
insulate
below
this line
Main Valve
Type E or E2
Control
Pipe
Pilot
Type A85
No. 8B Tee
Serial
No. Plate
Restriction
Bend
1/4" Union
TROUBLE SHOOTING
TYPE T61, T63
TYPE T62